Working with Silica – Important Update
Aug 26, 2024
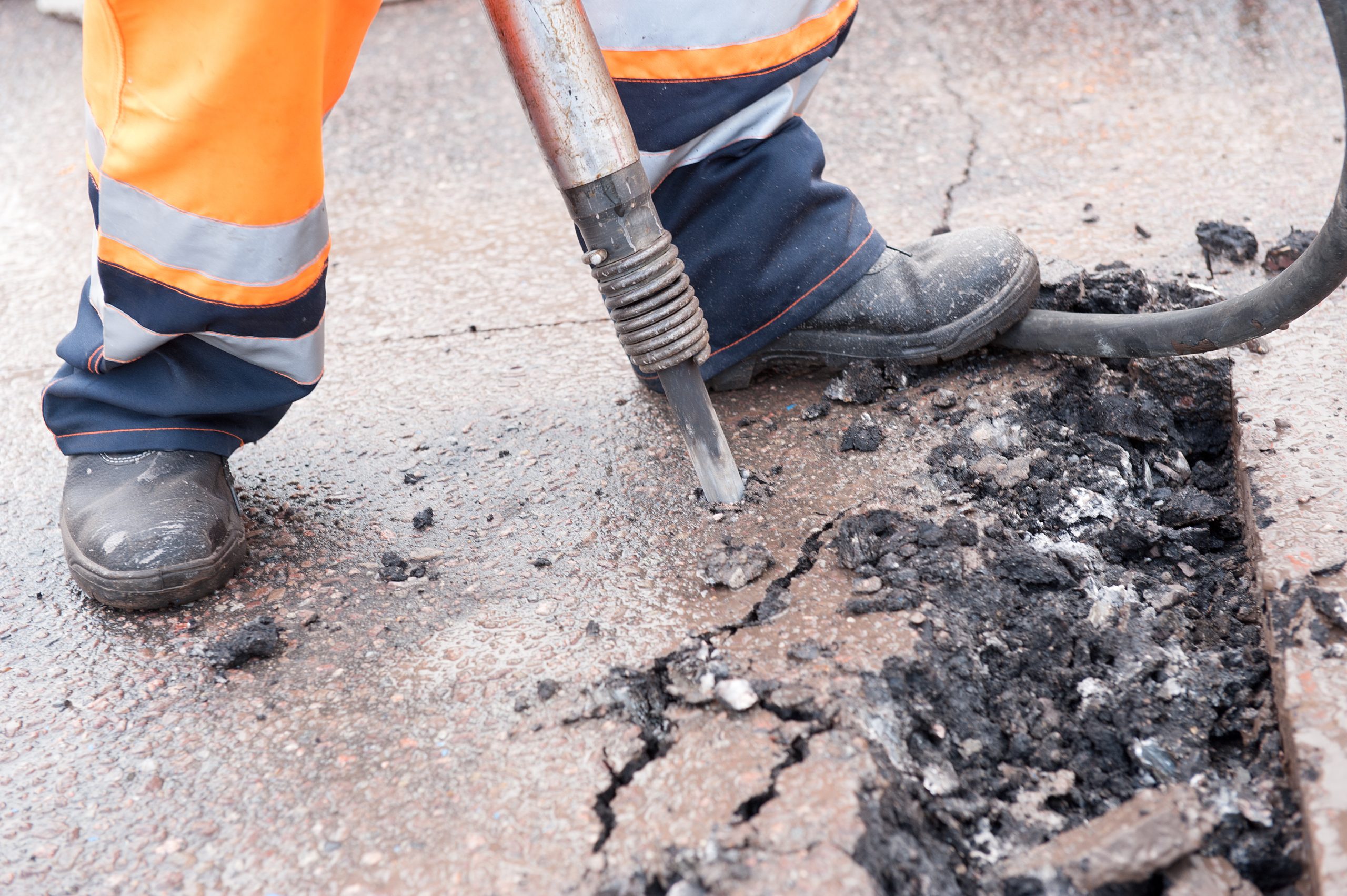
You’re probably across the recent engineered stone ban, but did you know SafeWork Australia has just come out with new rules to further protect workers from crystalline silica found in other building materials? These new rules begin on 1st September this year and apply to all states except Victoria whose rules are already in place.
Crystalline Silica Substances (CSS) include stuff like sand, stone, concrete, and mortar that contain at least 1% crystalline silica. When you cut, crush, drill, polish, saw or grind these materials, they release tiny dust particles called respirable crystalline silica (RCS). These particles are so small they can get deep into your lungs, which can lead to serious health issues, like silicosis—a lung disease.
What you need to do:
Risk Assessment
If silica dust is generated, assess if the work is high-risk. Document this using the handy Form in the HazardCo Hub, and if you determine the work is not high risk, you must explain why. If you’re unsure, assume it is high-risk. When assessing if processing CSS is high risk, consider these factors:
-
- The process
- Type and amount of silica (you can find this on the safety data sheet or product information sheet)
- Exposure duration
- If the work exceeds half the exposure standard (likely examples include grinding concrete, cutting concrete or bricks, jackhammering concrete or sandstone, and tuck-point grinding)
- Previous monitoring results
- Any past incidents or health issues related to silica dust
Put control measures in place (this applies to both low risk and high risk work)
Eliminate or minimise the risks from processing the CSS as much as possible and use at least one of the following measures during the processing:
- Isolate workers from dust exposure
- A fully enclosed operator cabin fitted with a high efficiency air filtration system
- An effective wet dust suppression method
- An effective on-tool extraction system
- An effective local exhaust ventilation system
If workers are still at risk of being exposed to silica dust after you’ve put one or more of the above controls in place they need to be provided with respiratory protective equipment (RPE) and wear the respiratory protective equipment while the work is carried out.
If you think it’s high-risk work:
Silica risk control plan
Avoid high-risk tasks when possible. If unavoidable, create a silica risk control plan outlining tasks, risks, and controls. This plan must be developed with workers, shared with them before starting work, and regularly reviewed for effectiveness.
What needs to be in a silica risk control plan?
- The processes you are doing that are high risk
- A copy of the information used to assess the risk
- What control measures will be used to control the risks and how those measures will be implemented, monitored and reviewed
Keep it simple and easy to understand—no need for lengthy explanations.
We suggest using the SWMS tool in the HazardCo App if the processing creates a contaminated atmosphere or involves high-risk construction work. Just ensure all the Silica Control Plan requirements are covered.
Training
Ensure that any worker involved in or at risk of RCS exposure due to high-risk CSS processing receives crystalline silica training. This training must be nationally accredited or approved by the WHS regulator and should cover health risks and the correct use of control measures.
Air monitoring
Conduct air monitoring if you’re unsure whether silica levels exceed the Workplace Exposure Standard (WES) or need to assess if there are health risks from RCS processes. Hire a certified expert like an occupational hygienist, to perform the monitoring and ensure it meets standards. If levels exceed limits, report it to the Regulator within 14 days. Keep records for 30 years and make them available to affected workers.
Health monitoring
Provide health monitoring for workers at significant risk from ongoing silica exposure, including those near high-risk processing. Keep records for 30 years and give a copy to the worker.
Review controls
Regularly review safety measures, especially after workplace changes.
If you need guidance, reach out to our advisory team at 1800 954 702 for assistance.