Angle grinders are versatile hand-held tools that are used regularly in the residential construction industry.
Serious incidents can occur when using grinders onsite. The most common causes of injury to operators and nearby workers from angle grinders are:
- Serious harm if caught by cutting/grinding wheel.
- lacerations from angle grinder kickbacks.
- lacerations from attachments that break and become projectiles.
- Hearing damage from wheels cutting through material.
- Burns from sparks and workpiece surfaces.
What are some control measures to reduce the risk of injury?
Here are some control measures to consider when it comes to managing the risks associated with grinders:
- Determine if an angle grinder is actually the best tool to perform the task, because another tool may be just as, or even more, effective.
- Prior to purchasing a grinder, look at ones with adjustable handles that can be moved to suit both left and right-handed operators.
- Select a grinder that has an automatic cut-off or dead-man switch as part of the handgrip. This is designed to cut off power as soon as finger pressure is released.
- Only use angle grinders that are an appropriate size for the task. Do not use a grinder that is larger, heavier or more powerful than is necessary, as it is much easier to control a lighter tool.
- Ensure guards are never removed. The guard usually covers half of the disc and is positioned between the disc and the operator.
- Ensure that the correct type of disc is used for the task being performed. The wrong disc potentially can shatter or ‘grab’ the workpiece causing kickback.
- Regular maintenance and inspection of the grinder and cutting disc by a competent person, as per the manufacturer’s specifications.
- Provide operators with appropriate information, training, and instruction to ensure the grinder is operated safely and competently.
Before use
Before using an angle grinder, it’s important to check that:
- Guard and handles are secure.
- There are no defects or damage to the disc (a disc that has been dropped may have developed cracks and should not be used).
- Use only the tightening tool supplied by the grinder manufacturer to tighten the disc as other methods can damage the disc and grinder.
- The spindle’s correct disc diameter and central disc hole size are used.
- The correct type of disc is used for the material being cut or ground.
- Make sure the disc is the right way up.
During use
Consider the following safe practices when an angle grinder is in use:
- Always ensure that your work area is well ventilated.
- Position the tool so that the power cord always stays behind the machine during operation.
- Make sure the wheel is not contacting the workpiece before the switch is turned on.
- Before using the grinder, test run the tool at the highest no load speed, and stop immediately if any vibration or wobbling occurs.
- Look out for flying sparks. Hold the tool so that sparks fly away from you, others, and flammable materials.
- Use both hands to operate the grinder. One hand should grip the handle and dead-man switch (if provided), while the other hand supports the weight of the tool.
- Allow the grinder to ‘run up’ to operating speed before applying it to the job.
- Position the grinder against the workpiece with minimum pressure, so the disc does not ‘grab’ and cause it to kickback.
- Keep the grinding disc at a 15 – 30 degree angle to the object. Check that the workpiece is held firmly, either as part of a larger item or in a bench vice.
- Keep the work at waist height during grinding where possible.
- Angle grinders must have stopped turning completely before they are put down or moved around the workplace.
- Before changing discs, remove the plug from the power point.
- Never use a grinding disc for cutting or a cutting disc for grinding.
- Do not touch the workpiece immediately after operation. It may be extremely hot and could burn your skin.
- Ensure correct PPE is worn for the task/ job and review what can get caught in a moving part of the tool. For example:
- Ensure workers do not wear loose clothing or jewelry.
- Long hair is to be tied back so nothing can become caught
- Workers should wear protective clothing such as safety glasses, leather aprons, gloves, face shield (if required), safety boots, RPE (if required) and hearing protection as they will be better protected.
If you’ve got a question about safe grinder use or any other health and safety matter, the HazardCo Advisory Team is here to help. Give them a call on 1800 954 702.
We’re proud to announce the partnership between HazardCo and Mitre 10 Australia to help more builders feel confident they are nailing their health and safety.
We know that many builders need to get on top of their health and safety. In fact, the 2023 State of Residential Construction Industry report stated that 45% of building companies in Australia don’t have an established health and safety system in place at all.
We’ve partnered with Mitre 10, one of the leading trade hardware stores in Australia, to make it easier than ever for builders, renovators and trades to protect their crew and their business with the HazardCo system.
With this Mitre 10 partnership, you can now charge HazardCo to your Mitre 10 trade account, so it’s super easy to get on board.
We pride ourselves on making health and safety easy to understand and simple to action on-site.
Have a chat to your local Mitre 10 trade rep or store, or get in touch with us below.
Email info@hazardco.com | Call 1800 954 702
SWMS templates are great, most of the time. A template will provide a structure so that you don’t miss any important steps, help you to save time, and a good template will even help you to learn more about what controls to put in place to manage the hazards involved in completing the task.
To be effective, your SWMS needs to be specific to the task, the site and the workers carrying it out. Generic SWMS templates don’t cut it. The SWMS needs to lay out the steps that will be taken to carry out the task and then those steps need to be followed. If work is being carried out in a way that doesn’t match the task steps in the SWMS, the work needs to stop.
One SWMS can be prepared to cover various tasks as long as it takes into account the dynamic nature of the work environment and can be easily read and understood by the workers involved. You might find it easier to create a separate SWMS for each high-risk construction work activity, but remember you need to think about how different activities taking place at the same time or how one activity after another could impact each other.
We recommend looking for a SWMS template that will help you to spend less time writing (as that’s the bit that takes the most amount of time). The template should be guided, rather than just an empty shell that needs to be filled in from scratch. Make sure it’s quick and easy to customise. You should be able to easily adjust the hazards, controls and task steps to reflect how the work will be carried out. It should also use simple language everyone understands.
Digital SWMS templates that you can create, review, edit, sign and save on your phone are a great way to get into the habit of doing your SWMS each and every time you are completing high risk construction work. By using a SWMS App, you’ll know you’ve always got the template ready to go in your back pocket and you’ll know you’ve got a full record of all your completed and signed SWMS saved online.
The HazardCo App includes 25-easy to edit templates, or you can use the template builder to create a SWMS. It only takes a few minutes, and it will suggest controls to put in place, based on the common hazards you identify. If you have a similar job coming up, you can save the SWMS as a Favourite and update it on the go to be task and site-specific. Easy as!
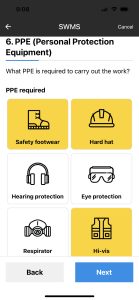
Get a free HazardCo trial.
Learn more about HazardCo SWMS templates and health and safety App.
What is a White Card?
A White Card is proof that you have completed an approved construction induction training course. The training provides basic knowledge of construction work, health and safety laws, common site hazards and how to control the associated risks.
White Cards are also known as Construction Induction Training Cards or General Construction Induction Cards. In some states, a previously issued blue card or red card may still be accepted.
Who needs to have a White Card on a residential construction site?
Everyone carrying out construction work needs to have a valid White Card. This includes people who may not be on the tools, such as Principal Contractors, Site Managers and Site Supervisors. Essentially anyone who enters a construction site that is unaccompanied or not directly supervised by an inducted person needs to have a White Card.
Who is responsible for checking everyone on site has a valid White Card?
Employers must make sure that anyone intending to carry out construction work has completed the required training before they start work. An Employer is required to keep a record of their worker’s training and competencies including White Cards.
White Card holders need to make sure they can show their White Card for inspection while on-site.
As a Principal Contractor, what’s the easiest way to make sure everyone on my building sites has a White Card?
Residential construction sites have people coming and coming all day. The HazardCo system automates the process of checking White Cards and makes it really simple.
When a worker scans into your site they will be guided through a site induction and prompted to submit a photo of their White Card by taking a photo of it. The photo of the White Card will be shared with you and saved for your records.
Does a White Card expire?
A White Card doesn’t expire as long as the worker keeps up their competencies. If they haven’t worked in the construction industry in the past two years, the White Card is not considered to be valid and they will need to complete the training again.
What happens if a worker is on-site without a valid White Card?
White Card training is intended to educate and provide awareness of key hazards and risks within the construction industry. It’s fair to say someone without this training may expose themselves or others to an unsafe work environment.
On top of that, as the White card is a mandatory requirement under Health and Safety legislation, a hefty fine can be imposed, something that no one wants!
How do I get a White Card?
You will need to complete an approved course. Here is more information by state:
Managing Workplace Health and Safety (WHS) on-site is all about identifying hazards and reducing risks to keep everyone safe. The most important thing you can do is make sure that everyone on-site takes WHS seriously, from the supervisor to the apprentice.
If you don’t know where to start with H&S, check out the list of top-priority health and safety actions we’ve listed below. If you’re looking for a detailed list of all the WHS tasks you should be checking off as a home builder, download the Residential Construction Health and Safety Checklist
Key WHS construction requirements in a nutshell:
What does good health and safety look like?
- You provide a safe working environment: Your site is safe and free from hazards that could cause harm to your employees or others.
- You have WHS management system in place: A WHS management system documents how you will manage WHS risks in your workplace. The system includes processes for identifying, assessing, and controlling risks. You have a Site Specific Safety Plan (SSSP) in place for every build. The plan is customised to the unique requirements of the project.
- Your contractors are up to scratch and operate safely on site: You’ve checked contractors have good WHS practices in place and the appropriate insurance to be operating.
- You regularly communicate with workers on-site: Everyone on-site has the appropriate training, instruction and information they need to carry out their work safely. When it comes to health and safety, you can’t communicate too much!
- You collect a Safe Working Method Statement (SWMS) before High Risk Construction Work begins on-site: Importantly, the SWMS is specific to the task and the site at hand.
- You monitor health and safety performance: You regularly monitor your WHS activity and identify any areas where improvements can be made.
- All incidents are reported: Incidents and near misses on site are reported, documented and investigated. Investigating near misses and incidents will help you to understand the cause so you can put corrective actions in place to prevent similar incidents from happening again in the future. If an incident is notifiable, it is reported to the regulator.
- Nailed all these things? Download the full Health and Safety checklist
Take the hard yakka out of health and safety, with simple digital tools and expert advice when you need it. The HazardCo system will give you confidence that you’re doing all the right things on-site, in the right way. It even has a SSSP Generator so you can create a site-specific safety plan in minutes – take it for a test drive.
As a building company, you’re responsible for the H&S of everyone on-site, not just your direct employees. We know that getting contractors involved in H&S is a big challenge for building companies and is exposing you to additional risk.
Of course, building companies often tell us that although they have some influence over contractors on-site, getting them to engage with health and safety is a challenge, as they don’t have the same level of control over contractors compared to direct staff. Too often, contractors arrive on-site without an established H&S system and need a lot of support from the main contractor. If they do have their own system it creates a paperwork nightmare for the building company that is responsible for ensuring reports are completed and collected.
What does good contractor management look like?
First, you need to make sure contractors have the right skills and experience to do the job, and second, you need to make sure they are going to carry out the work safely. Once they are onboard, you need to monitor throughout the build if the contractor is following good health and safety practices on-site.
We’ve created a number of new tools that will help you to manage your contractors before they begin working with you and while they are on-site. We’ve also made it easier to monitor your contractor’s H&S activity, even when you’re in the office. It’s one system for everyone.
How does it work?
Pre-site – Do your homework before you start working with contractors to reduce the risk to your business
- Simple pre-qualification – Hit one button to start the pre-qualification process with a new contractor. From there, they will automatically be sent a questionnaire requesting all the information and documents you need, including public liability insurance, a policy and procedures document, and evidence they follow good H&S practices on-site.
- Automated reminders to save you time – If your contractors don’t respond, they will receive email reminders until they complete the process. You will get a notification when the documentation is ready to check and approve. No more chasing contractors and long no more long email chains.
On-site – Love the HazardCo app? Now contractors can use it too. One H&S tool for everyone under one roof
- One system for everyone – From employees to contractors, everyone on-site will be able to use the HazardCo app to complete H&S reports such as site reviews, SWMS, incident reports, and more. Workers can collaborate on safety by creating and assigning tasks. you’ll know everyone has guided, easy-to-use tools at the ready to manage H&S on-site. All reports will be shared with you. And they will get a copy for their own records too. Finally, kill paperwork on-site.
- Unauthorised worker notification – If a worker scans onto a site that hasn’t been approved yet, you’ll get a notification. So unless you hear otherwise, you can be sure everyone on-site is good to go.
Oversight – Get the big picture view of all H&S activity taking place
- Monitor H&S activity with dashboards – You’ll be able to see all H&S activity at a project or company level. For the first time, you will have full visibility of all H&S activity taking place on-site, from employees to contractors.
- Create a record of good health and safety practices over time – All reports created on-site will be automatically sent to you and stored for safe keeping. Say goodbye to paperwork and filing.
Managing your contractors and ensuring their safety on-site is non-negotiable, so make it simpler, and let our digital and automated tools do the heavy lifting. Get in touch with the HazardCo team to find out more about these pre-qualification tools, and how we can help you to manage contractor safety on-site.
It’s fair to say that there will be various electrical equipment on your Construction site. To ensure your electrical equipment is safe and in good condition you should do daily inspections before use and have your equipment tested and tagged.
What is testing and tagging?
Testing and tagging is checking the safety of portable electrical appliances that get used in the workplace.
It involves two steps: Visually inspecting the appliance for any noticeable damage,
- cracked casings
- missing or damaged guards
- nicked cables; tape covering nicks or cuts
- dry and brittle insulation
- burn marks or signs of overheating
- RCDs not tripping when tested
And secondly, electrically testing it with a Portable Appliance Tester (PAT). Once tested and approved, a tag is attached with the following information:
- who tested it,
- the test date, and
- when the next test is due.
Why do you need to test and tag?
Testing and tagging helps identify any faults or damage in the equipment that could potentially cause harm to workers. Any lead or cord that is damaged or that fails testing is to be immediately taken out of use and removed offsite. If you cannot promptly remove it offsite, consider other means like attaching a durable out of service tag so as to warn workers not to use that piece of equipment.
Who can complete a test and tag?
Inspection, testing and tagging of electrical leads and cords on construction sites are required to be completed every 3 months by a competent person. A competent person is someone who has the relevant knowledge, skills and test instruments to carry out the relevant inspection and testing.
If the testing reveals any issues or something needs fixing then a registered electrical worker will be required.
What type of equipment needs to be tested and tagged?
In short, basically any electrical corded power tool or device. This includes any device or appliance that has a flexible cable, and a removable plug, and also includes both single and three-phase connections.
Keeping you and your workmates safe at work is a priority, so make sure you are aware of the businesses testing and tagging requirements on-site.
The HazardCo App site review resource has a list of electrical controls that should be in place to manage the risk of electrical hazards.
Want more information? Have a look at our other blog on RCDs and Leads – protection against electrical shock.
Near Misses
A near miss is an incident that occurs but doesn’t lead to injury, illness, or damage.
No matter what working environment you are in, work sites nationwide have near misses every day. On-site, a near miss could be tripping over stacked material, it could be dropping the hammer off the scaffold onto the ground or backing the truck and narrowly missing the boss’s ute. While these seem fairly innocent, they could have been more serious.
Like other incidents, these near misses need to be recorded and reported as soon as they occur. Once they have been, you can look into what caused the near-miss and put steps in place to avoid it turning into something more serious.
Reporting near misses
Near misses should be considered the same as an incident. But often they aren’t.
We often find that near misses are very rarely reported, and actually brushed off. Near misses are just as dangerous as actual incidents. If you’ve had a near miss, you might have got lucky but someone else might not. Treat near misses as a free learning tool to put controls in place to prevent more serious incidents from occurring.
By encouraging near miss reporting, you can start to see patterns and gain valuable insights on where to best focus resources into safety.
Reporting all near misses and incidents on-site, is all about helping to prevent harm. Everyone on-site has a right to know of potential threats that may impact them, and everyone plays a role in keeping everyone safe on-site.
Getting everyone to report near misses and incidents creates a culture of open, honest discussions about health and safety.
Encourage reporting and recording
Best practice is that all incidents, whether they cause injury or not, need to be reported and added to your incident register.
The more reporting you have, the more data is available for those in a position to influence change, as it can help them to see areas that require improvement or to see how effective implemented controls have been.
Encouraging the reporting of these incidents is simple with the HazardCo App:
- Everything is completed digitally on your team’s phone and the process is simple and easy to follow.
- With remote reporting in the mobile App, your team no longer has to wait until they get home or to the office to report the incident. They can quickly do it while it’s still fresh.
- Encourages conversation – with the App you can easily record and quickly pull up all incidents through the HazardCo Hub and discuss them in toolbox meetings.
- All incidents are added to your digital incident register which is easily accessible from the HazardCo Hub whenever you need to revisit.
No matter how big or small, report all near misses and incidents so you can all learn from them. Using the Report Incident feature on your HazardCo App, fill out the fields to capture what happened. Your reported incident will be added to your incident register in the Hub, and HazardCo retains this for as long as you’re a member.
Ensure you take incidents and near misses seriously and investigate them. Investigations help you work out the root cause so you can put corrective actions in place to prevent a recurrence.
We all dread an incident occurring, but if anything serious happens on your site it’s important you are prepared, remain calm, and do the right thing. When in doubt, call HazardCo – we are here to support the health and safety needs of all HazardCo members 24/7. If you’d like to learn more about the App and the Reporting Incident tool take a look at our short demo videos
When risks and hazards are recognised early, controls can be put in place to prevent harm to workers, visitors, and the public.
Reporting and controlling hazards/risks is a way of being proactive and helping create a safe environment for everyone to work in.
A key part of Health and Safety legislation across Australia is the need to both identify these hazards, and then manage the risks involved so they are either removed or controlled correctly. Creating a Task in the HazardCo App to report the hazard is a simple and effective way to manage this responsibility.
There are always going to be hazards and risks on construction sites; they are dynamic places. Identifying the hazards that could cause serious injury or harm to both workers’ health and safety helps manage risk as the project moves along and helps those who manage the jobs plan for them better in the future.
For example:
The concrete pumping truck has a blockage on-site, and the team decides to try and rectify the blockage whilst other workers are in close proximity. Joe is aware of the hazards and risks of clearing blockages under high pressure, and that someone could get seriously injured if things go wrong. He recommends that the concrete pumping team stop and do it away from other workers in a safe location. Because no incident or near miss occurred of anyone getting or nearly getting hurt, Joe logs this hazard as a Task in the HazardCo App.
The company reviews all the tasks that have been logged for the project and sees Joe’s reported hazard. With new knowledge of the dangers involved and the controls used to manage the risks of concrete truck blockages. The company decides to use those controls on all sites going forward.
Hazard reporting is an effective and ongoing way for workers to raise concerns or suggest improvements on a day-to-day basis.
How hazards differ from near misses:
Hazard: something could occur.
Near Miss: something did occur but there was no harm caused.
Hazard example:
Joe notices an extension cable has been badly damaged and is still plugged in. He turns off the power and removes the cable from services and logs it as a Task in the HazardCo App before someone could get hurt.
Reporting hazards as a Task in the HazardCo App helps with:
- being proactive by controlling risk before it turns into an incident
- getting workers involved in managing site safety
- identifying and reporting hazards when completing risk assessments and site reviews on-site brings attention to the hazards that need addressing by assigning action and priority to the right team member, and then being able to track progress until the hazard is sorted.
Near miss example:
Joe sees a fellow worker about to roll up a badly damaged extension cord whilst it is still plugged in, he immediately stops the worker before he could have got hurt. Turns off the power and removes the cable from service and logs a near miss as an Incident in the HazardCo App.
Reporting a near miss helps with:
- recording incidents that nearly or could have caused harm
- shows how well or not controls are working
- identifying if too many similar near misses are happening which could indicate that you have an issue that needs controlling
What’s Contractor management?
Contractor Management is simply ensuring your contractors are competent, qualified, licenced and inducted before visiting your site.
How does it apply to me?
If you own a building company, chances are you’re the Principal Contractor of the building site. This means it’s your responsibility to check that all contractors meet the requirements to work on your project. This involves making sure everyone is appropriately licenced, competent and compliant before jumping into any work on-site.
It’s also vital to closely observe contractors, especially anyone unfamiliar with your site, to make sure work is conducted safely.
Digitally documenting everything is the easiest way to avoid landing in hot water over lost paperwork or abandoned inductions.
Here’s what you should check:
Check company info annually
- ABN and company details
- Insurance (work cover, public liability and income protection)
- What’s their current health and safety policy?
- Can they prove they follow good processes?
Induction of workers
- Check white cards are current, as well as any other trade qualifications or licence
- Have they read and agreed to the site specific safety plan?
- Have they been made aware of any hazards on-site?
- Are they bringing any hazards on-site?
On-site health and safety
As a general benchmark, we recommend these steps to stay up to date:
- Start off on the right foot with a Risk Assessment prior to starting a new task or activity: Contractors can check that the work area / site is safe and any new hazards are identified and managed.
- Complete a SWMS before performing high-risk construction work: Contractors completing a SWMS may need to provide a copy to the Principal Contractor before starting work.
- Consult and communicate with a Toolbox meeting once a week/fortnight: Share and capture what’s happening on-site, including hazards, incidents and corrective actions with workers and contractors.
- Report all incidents as they happen, including near misses: Reporting and investigating incidents helps you take action to minimise the chance of it happening again.
- Check your vehicle once a month: Check when your service is due, check the emergency equipment such as the first aid kit and fire extinguisher and the condition of the vehicle.
- Review and monitor: Regularly take stock of your site or work area by completing a Site Review.
How to keep track of it all
When you’ve got a lot of contractors coming and going, it can turn into a bit of a headache trying to stay on top of checking all these documents. We’ve created a simple, automated system to nail the pre-qualification of your contractors before you begin working with them, to reduce the risk to your business.
Find out more about HazardCo’s Pre-Qualification Tools here
Looking for something in particular?
When you're able to get back on site after a flood or storm, here are the hazards, risks and control measures you should consider to help reduce the risk of injury and illness to yourself, you...
Dust is a common hazard in the construction industry, especially during demolition or refurbishment. When buildings are demolished they can release materials that create hazardous dust (airbor...
The holiday season is over and now it’s time to get back into the swing of things. Coming back to work and reopening your site is just as important as shutting it down. The New Year is the per...
The holiday season is almost upon us, and we’re all eager to have a bit of a rest, recharge, and spend quality time with our families. As we wind up 2024, it is a demanding time for constructi...
When you have an incident on-site, whether it’s a near miss, an injury, or a work-related illness, it’s important to document an incident report.
Incident reports don’t need to be time-cons...
Electricity is essential on construction sites, but if the risks are not managed properly, it can pose serious dangers to people and property. Proper controls must be in place wherever electri...
Health and safety is a core part of any business but incidents and injuries on the job can still happen. According to SafeWork Australia, in the construction industry alone there were 15,877 s...
HazardCo understands that on-site first aid is about more than just sending someone on a course every few years. As an employer or principal contractor on-site, you have a legal and moral obli...
Did you know that if you’re carrying out renovation work the same risks apply as a new build? Whether you’re carrying out extensions, renovating, flood remedial work, large landscaping jobs or...
When it comes to construction sites, ensuring the safety and wellbeing of everyone on-site is the top priority. It’s more than just wearing hard hats and high-vis vests. It involves careful pl...
Long gone are the days of “she’ll be right mate”. Staying on top of your health and safety makes your site safer - simple as that. We all want our team members to get home safely at ...
The reality is unsafe work at heights can have devastating consequences. Falls from heights are one of the leading causes of fatalities and injuries in the construction industry within Austral...