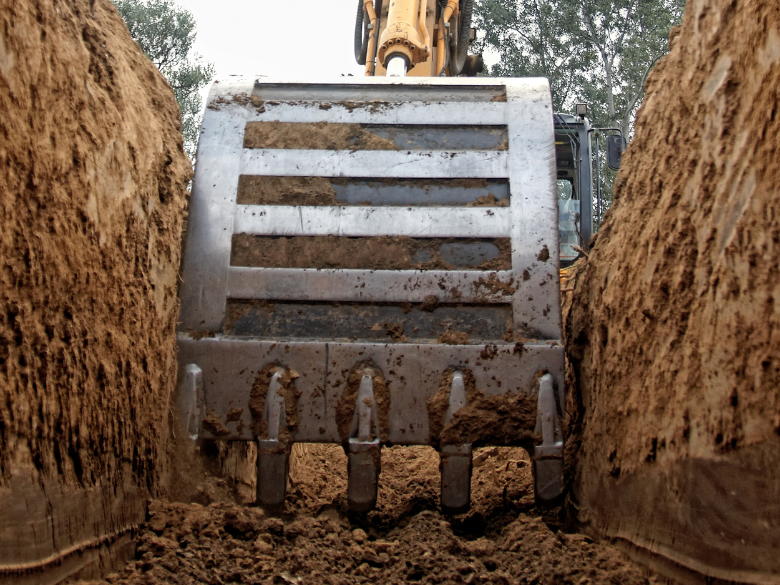
This strategic partnership brings together two leading systems, as construction companies across Australia and New Zealand are increasingly adopting on-site technology to ease their administrative burden and work more efficiently.
We make health and safety simple, giving more than 10,000 companies the confidence they are keeping their team and their business safe, while reducing the time they spend on paperwork. Our system provides guided digital tools as well as incident support and health and safety advice when it is needed. We’re most well known for our simple and effective site induction and scan-in solution.
“We’re pleased to be able to integrate Procore with our unique site induction and scan-in solution, making it faster and easier than ever for Procore customers to know who is on-site, and when,” said Nick Halley, Head of Product at HazardCo. “Members receive a hazard board with a unique QR code for their site fence, and everyone uses the free app to scan into site, induct themselves and accept the safety plan, with H&S docs seamlessly flowing back into Procore.”
“Our goal is to make health and safety simple. This exciting partnership between HazardCo and Procore connects construction management and health and safety together, giving building companies an out-of-the box digital WHS system that seamlessly connects with their existing workflows,” said Iain Dixon, Chief Executive at HazardCo.
He concludes, “we regularly speak to builders that are passionate about building scalable and efficient processes for their business, but health and safety continues to be a very manual and paper-heavy activity for them. There are large gains to be made by digitizing health and safety, with HazardCo members telling us they have halved the time they spend on WHS admin using our simple system. This partnership will make it easier for building companies to streamline their processes and give them the confidence they are on top of their health and safety requirements.”
Health and safety issues arise from a worker raising concern about health and safety at the workplace and that concern remains unresolved after consultation with the worker/s and the PCBU/Employer, it then becomes a health and safety issue
For example, an issue could include a difference in opinion on whether something is a potential risk to health and safety or whether a particular control measure is suitable. .
There are issue resolution requirements in Health and Safety legislation across Australia which outline how a health and safety issue can be resolved, with the aim to agree on how to fix the problem as soon as possible to avoid further dispute or a similar future issue.
PCBUs/Employers are to agree on the issue resolution procedure with their workers. If this does not occur, the default procedure for issue resolution under the relevant State/ Territory WHS Regulations must then be followed.
Multiple people will be involved in the issue resolution process to ensure adequate consultation and the best outcome occurs. This means it could be:
If you or your worker would like to involve representatives in the issue resolution process you are able to do so. A representative does not necessarily need to have health and safety expertise. This could include people such as a designer of a piece of equipment at the workplace, or a person with workplace consultation and negotiation skills. Depending on the nature of the H&S issue, advice or assistance from a range of experts may be required to reach an appropriate and informed resolution between the involved parties.
Things to remember:
It’s an agreed process or steps for resolving health and safety issues in the workplace.
You can establish an agreed procedure for a workplace. To do this, make sure the procedure:
The various State/ Territory Regulations set out the default procedure for issue resolution.
The default procedure provides for any party to the issue to commence the procedure by informing the other parties involved that there is an issue to be resolved and the details of the issue.
In attempting to resolve the issue, the default procedure requires the parties to have consider and review relevant matters, including:
If the issue is resolved, details of the issue and the resolution must be set out in a written agreement, if any party to the issue requests this. If a written agreement is prepared:
If you’ve got a question about Health and Safety issue resolution or any other health and safety matter, the HazardCo Advisory Team is here to help. Give us a call on 1800 954 702.
Phew, what a year 2022 was. With continued labour shortages and skyrocketing supply increases it certainly wasn’t an easy year for residential builders in Australia.
The reality is that no one knows what 2023 has in store, so the best bet is to take stock of the things in your control. With a deep understanding of your business and some rock-solid processes, you can build a strong, resilient building company that is prepared for anything!
Check out this list of construction apps and technology that can help you stop scrambling around with paperwork and manual time-wasting tasks. Go digital and build a resilient business that gets ahead in 2023.
BuiltGrid is Australia’s supplier-connected project management system. The platform empowers builders to manage existing trades and find new trades & suppliers who want work. BuiltGrid will ensure your construction business completes your next project on time and under budget.
With no supply chain connectivity material and trade pressures are likely to continue into 2023, Toby Loft, co-founder at BuiltGrid says, “We’re dedicated to improving project visibility to reduce costly waste and rework; with real-time connection to your supplier’s builders save tens of thousands for every house built. Builders using BuiltGrid achieve a cost reduction of 8.75% in time, work and materials, giving them a significant boost in profits. With BuiltGrid, you can manage existing or find new trades & suppliers, compare quotes and automate your admin.”
Find out more about BuiltGrid.
Buildxact is easy to use construction management and estimating software designed for small builders and contractors. It will help you to run your construction projects, from take off to invoice.
“With all of the current challenges in the market, building companies can really benefit from putting a system in place that helps them to deal with last minute schedule changes and price increases on the fly. Buildxact is really flexible. It will help you to stay on top of each job, giving you a clear picture of income and outgoings so you’ll know exactly where your job profit stands. Buildxact also now integrates directly with your supplier to get the latest prices to you to make your quoting quicker and more accurate”, says Julian Krishnan Nair from Buildxact.
“Our customers often tell us that using Buildxact cuts the time spend on take offs by 80%. You can upload the PDF and do your takeoff on-screen in minutes, you don’t need paper plans or scale rulers. Measure in a few clicks and price jobs in one step.”
Find out more about Buildxact.
HazardCo is a digital health and safety management system for home builders. It makes health and safety simple, giving you the confidence you’re keeping your crew and business safe, while cutting the time you spend on paperwork.
“When small builders want to move away from paperwork and digitize their processes, the first place they often start is health and safety. It’s an easy win that’s quick to implement and delivers instant results. You can create a site specific safety plan in minutes and have everyone scanning into your site in no time. As well as saving time, automating your contractor management processes helps to deal with labour shortages and provides flexibility,” says Luke Williams, from HazardCo.
HazardCo is trusted by 10,000 businesses across Australia and New Zealand
Getter has created an on-demand procurement platform for all tools and materials, bridging the gap between wholesaler and construction site. Getter has an extensive supply chain that can tip the scales to your competitive advantage as project margins fall and programs tighten.
Sam Hatty from Getter explains, “Getter is the answer to one of the greatest productivity killers all builders and tradies face in their day-to-day – supply procurement. We were founded by a group of tradies so we’re well aware of the constraints that sourcing and procurement can put on a project, both economically and time-wise. What makes us different is our unique technology backed by an enthusiastic team and an extensive supply chain. We have a heavy focus on customer service and precision delivery by our own inhouse fleet.”
The platform consists of 2 sourcing options; ‘Shop and Deliver’ and the recently launched ‘Getter Quotes’.The Shop and Deliver service offers an online catalogue boasting over 100,000 products categorised into trade-specific genres with an intuitive product availability filter according to location. Getter Quotes simplifies a traditional material sourcing process from clunky emails, phone calls & over the phone prices to an easy to use, transparent, itemised quotation process. Giving customers access to a much wider range at incredibly competitive pricing.
Landchecker brings over 300 sources of information into one place so you see the full story of any property.
Craig Heaven from Landchecker says, “When a potential client calls you up about a site and they’re wanting to know the possibilities, you can quickly put the address into Landchecker and view up to date property information about the site in one place. Landchecker is fast, accurate and easy to use so you will look like a pro to the potential client and ensure the build aligns to your company”
Information includes land size, planning zones, overlays, and previous planning permits for the property and surrounding area. Turn on high-resolution aerial imagery to get a good look at the site and to see what it looks like now and historically to see what’s developed around the property. Landchecker is currently available in Vic, NSW, Qld,WA, Tas and SA with more than 3000 builders regularly using the platform.
Find out more about Landchecker.
Xero is online accounting software for your business that connects you to your bank, accountant, bookkeeper, and other business apps. It’s made for small businesses, so you can automate admin and work from anywhere, any time.
The thing about construction accounting is that you have to do it regularly. If you fall behind in your accounts, things can quickly get out of hand. So it’s vital to build accounting into your workflow. Xero is cloud based and simple to use. Whether you are on site or in the office you can access Xero on your smartphone or tablet so you’ll never get behind.
PSI Global specialises in property information for builders and trades.
“We know builders are busy managing their business, so we make it our mission to do the grunt work”, comments Samantha Whitmore, PSI Global.
“Our process is simple – we have great relationships with local government authorities, we gather all the information for you and we even do all the chasing up! We proactively keep you updated on how your job is tracking through our online portal and you can opt to receive your property information as we get it or at the very end in a neat package. We then provide you with one easy-to-manage invoice when your job is complete, no monthly subscriptions and no hidden fees.”
You can order Certificate Of Title, DP Plan (Title Plan), Instruments 88B, Sewer Drainage Diagram, Planning Certificate 10.7(2), Planning Certificate Section 10.7(5) and more.
Find out more about PSI Global.
There’s an easier way to kick off projects, and it’s with HazardCo. Cut the time you spend on health and safety admin, without cutting corners!
If you’re the principal contractor, you need to have a clear plan in place that everyone is aware of (including your workers and contractors).
Get tradies, contractors and anyone else stepping foot on-site to download the HazardCo app and you’re all set. Did we mention it’s free to download?
A quick scan of the onsite QR code with the app allows everyone to induct themselves as they turn up.
Start your project the right way. HazardCo will help you to nail your health and safety before you start the build and throughout the life of the project – giving you one less thing to worry about and helping you get your team and contractors home safe at the end of every day.
Our Advisory Team gets a heap of questions about near misses and if they should be recorded. Let’s look at what’s considered a near miss, when they should be recorded and how to go about it.
Tradies know all too well how regularly they have a close call on-site. But is a “close call” the same as a near miss?
Put simply, yes. A near miss is a dangerous event that occurred without causing personal injury or on-site damage of any kind.
Examples could be anything from a worker tripping over stacked material, dropping a hammer off the scaffold onto the ground, or backing the truck and narrowly missing the boss’s ute. While these seem fairly innocent, they could have been more serious and it’s important that they are all reported. Evaluating what could have been done differently ensures on-site health and safety remains a priority, with near-miss prevention at the top of the list.
Ignoring a near miss might not seem like a big deal, but it can create a culture on-site where safety isn’t taken seriously. We tend to find that when incidents aren’t reported, these are some of the common reasons why:
Look at near miss reporting as a second-chance educational tool. It’s not about blame or singling anyone out, it’s about discussing and emphasising a safer environment on-site. Combined with encouraging near miss reporting, it could mean the difference between change or injury.
Are there patterns in near misses occurring? Are there lots of reports of tools falling from height?
Investigate and ensure controls like the below are in place:
Near misses should never be overlooked. With a swipe and a few taps of the HazardCo App, on-site incident reporting couldn’t be easier. Every tradie deserves to knock off injury-free after a hard day on the tools. Follow up on near misses, discuss the possibilities and take action with HazardCo.
With the introduction of the new work health and safety regulations in WA that came into effect on 31 March 2022, we are pleased to be able to support home builders to understand these new WHS laws and put in place a simple and effective system that will help them to feel confident they are protecting both their team and their business.
Executive Director of Master Builders WA, John Gelavis says we are really excited about this partnership, as it will help provide Master Builders members with the opportunity to access reliable safety tools and advice, which will build a better and safer industry for all.
“The WA building and construction industry relies on safety advice, and with the recently changed Work Health and Safety Laws, this partnership with HazardCo will be an extremely useful tool and service for our members”, says Mr Gelavis.
Alongside discounted access to the HazardCo system and advisory services, Master Builders WA members are also entitled to a free WHS check-up to take stock of what should be done on-site and off-site to provide a safer site and work environment. We will help you evaluate your current systems in light of the new WHS laws in WA and will provide guidance on what’s being done well and areas of improvement.
Chief Executive and Director of HazardCo, Iain Dixon says HazardCo is proud to partner with Master Builders WA.
“Master Builders WA is one of the most recognised and respected brands in the industry. This partnership reflects our desire to collaborate with companies who share the common goal of helping builders to keep their teams and their businesses safe. We look forward to meeting more builders throughout WA and introducing them to a better, simpler way to manage their health and safety”, says Mr Dixon.
To find out more about the partnership and get your H&S sorted click here.
Summer is here, are you prepared for the heat?
Summer is here – longer days, sunshine, and the outdoors sound like the perfect conditions to get all that work done. It doesn’t matter what time of year it is, hazards and risks are forever present and summer brings with it its own risks.
Have you thought about what you are doing to protect your team from the effects of the summer sun and heat?
“Slip, Slop, Slap, Seek and Slide” to minimise the obvious risks of sunburn and skin cancer, but we also need to be aware of the risk of heat exhaustion, dehydration and fatigue.
Check out this resource from the Cancer Council that gives some handy tips for working outdoors.
Heat exhaustion
Heat exhaustion occurs when our bodies overheat from the loss of water and salt due to sweating. If left untreated it can lead to heat stroke.
Heat stroke
Heat stroke occurs when the body is no longer able to keep itself cool causing a high body temperature of 39.4 degrees or more.
Heat rash and heat cramps are earlier stages of the onset of heat exhaustion. Knowing the signs and what to do will help prevent the onset of heat exhaustion or worse, heat stroke.
Managing the risks
First Aid recommendations
If someone is showing signs or symptoms of a heat-related illness, Safe Work Australia has a great resource that gives some handy tips on first aid treatment options. Click here to learn more.
Note: Workers who have underlying medical conditions or health issues can make them more susceptible to heat related illness.
Need Help?
As always, if you have any questions or would like to discuss your work hazards, give our Health and Safety Advisory team a call on 1800 954 702.
When we hear the term “red flags”, we often think of warning signs when it comes to a particular situation. In the way of a construction site, this could be anything from a messy site, to using out of date H&S paperwork.
Some red flags are more visible or obvious than others, however it’s important to eliminate red flags on your site as they can cause injuries and other issues for you and your crew.
Not having a fence around the property perimeter could invite unauthorised entry. If your site isn’t secure, members of the public or children can enter the site, which could lead to injuries, property damage or stolen items.
Easy, ensure your site has adequate fencing set-up around the perimeter to prevent unauthorised entry. Take into consideration the height and ensure it’s not only high enough, but also check that the gap at the bottom isn’t too big where people including children could squeeze through underneath.
A messy site can lead to all sorts of problems. Waste and other objects left lying around can create obstacles for you and your crew. These in turn could cause slip and trip injuries, something we want to avoid!
Make sure your team is regularly cleaning up after themselves. Waste materials like cardboard, general rubbish and other lighter material to be placed/stored in such a way to eliminate tripping hazards and prevent them from flying off site especially during strong winds. Having a skip or bins available will make this task easier for everyone to get done.
The site sign provides all of the important details including an after hours contact number. If something happens on site and the principal contractor needs to be contacted, it needs to be easy to find.
Display a Principal Contractor sign in a visible location which includes the following information:
If there is no process for identifying the hazards, assessing the risks and what controls are required for a task, it could pose a significant risk to workers onsite.
SWMS are required for all high risk construction work. Ensure SWMS are accessible to the workers performing the task.
It’s important that SWMS are regularly reviewed. If the SWMS is not being followed due to a variation of work or conditions have changed, then work must stop until the SWMS is reviewed and updated.
There’s a few reasons why. When people are unaware of incidents or near misses occurring on site, it could lead to the same incident occurring repeatedly. The other issue is that some incidents legally need to be notified to WorkSafe/SafeWork. A fine can be given if this does not occur.
Reporting injuries is also important when it comes to making sure the worker receives appropriate treatment, (e.g. medical treatment) and other support, (e.g. return to work).
When incidents, near misses, injuries and illnesses occur on-site it’s important they are reported and investigated. By recording an incident via the HazardCo App, it automatically populates an incident register on your Hub so that all the incidents are recorded in one central location.
Investigations are important as they look at why the incident occurred and what controls can be implemented to prevent them from occurring again.
H&S paperwork needs to be kept up to date to help keep your workers safe. If yours is out of date, it could contribute to an incident on-site.
Additionally, lack of H&S documentation (e.g. SWMS) could mean you’re not complying with Legislation so you could be liable for certain prosecutions and/or fines.
If you’re old school and don’t mind filling out H&S paperwork by hand, make sure you are using something that is current e.g. SWMS is specific for the high risk task.
If you’re like us and love using a digital system, use the HazardCo App to get your H&S done quickly and simply. All of our features including the SWMS and site review are regularly reviewed and kept up to date including when legislation changes.
Click here to download the Builder checklist. If you’re a trade, email our team at info@hazardco.com and we’ll send you the Trade checklist.
Most cement, lime, mortar, concrete, and plaster products are hazardous substances that contain strong alkalis.
As seen in the image above, alkalis are on the opposite end of the PH scale from acids, however, can be equally as dangerous, being extremely destructive to your eyes. The way you handle the first seconds, minutes, and hours after you get the dry powder or wet mix in your eyes, will determine the outcome.
Alkalis may start their damaging work in your eye without much pain or symptoms, but over time the damage gets worse. So beware, follow the first aid steps below even if you don’t feel pain.
Don’t become one of the statistics: in 2019 – 2020 there were 197 injury claims resulting from chemical or other substances to the eye.
Every second counts! Run to the closest tap, eye wash station or water bottle and start flushing your eye. You are aiming to dilute the alkali to lessen the damage.
Wash your face and hands, you don’t want to get more cement product in your eyes. Flush your eye with a steady stream of running water. Let it pour into your eye while lifting both eyelids to rinse out all the cement granules underneath. Do not reuse the water and do not let contaminated water run into the unaffected eye.
If you do not flush your eye, or stop before you are told to do so, you may suffer from permanent eye damage, dry eyes, vision loss and more.
You can create a Hazardous Substances Register using the template available in your HazardCo hub. You can attach the SDS’s to the register and share it with your team.
If you have an incident where someone gets cement/concrete in their eye, remember to report this as an incident in the HazardCo App. This will automatically be added to your incident register in the HazardCo Hub, and the Advisory team will be in touch with you to discuss next steps if it is deemed to be notifiable.
For questions or support, contact the friendly advisory team at HazardCo on 1800 954 702 or info@hazardco.com.
Timber frame standing and truss erection can be back-breaking work! It is often high risk work with some serious potential injuries. We recommend these three steps are completed prior to every install. Ensure that everyone understands the process and their role, from when frames and trusses arrive on-site all the way through to standing.
The development of Risk Assessments and SWMS are crucial to your workers to ensure their safety throughout the build. To make these processes easy, you can complete these on the HazardCo App.
Some things to think about when creating a Risk Assessment and SWMS for frame and truss delivery and erection are:
Is the work area secure?
Clients, visitors, and members of the public cannot enter the area and workers are aware that they should only enter if they are required for the tasks.
Have all site inductions been carried out and an emergency plan developed for any at height work?
Have all workers who work at height been trained to do so? Is access to height suitable and is fall protection in place?
Have all workers been provided with the correct PPE? Are all tools and equipment available and in suitable working order for the task?
The purpose of a SWMS is to go into detail for each of the tasks to be carried out. Thinking about the hazards at each step and how they can be appropriately controlled.
You should think about:
Prior to work starting, workers should be involved in developing a SWMS. Consulting workers is important so they understand the detail of the SWMS and what they are required to do to implement and maintain risk controls. Sharing information and using the knowledge and experience of workers will help make sure the work is performed safely and in line with the SWMS.
On paper, this sounds like a lot of work – but it is made simple by using the HazardCo App, and using SWMS templates that you can save as templates and amend again and again. You’re not having to start from the beginning for tasks that you complete regularly. Do remember to check over your templates before approving them as different sites can present different hazards that you don’t want to miss, (overhead power lines as an example).
When working at height, either on a second story or setting trusses you need to ensure that your workers are safe, not just from falling, but from tools, equipment, or materials falling too.
Scaffolding
Once the lower level frames have been stood/braced appropriately, safe working platforms should be installed such as scaffolding. Scaffolding over 4m must be erected by a licensed scaffolder and all scaffolding should be checked by a competent person regularly.
Edge protection
If the potential of a fall cannot be eliminated when working on a roof, some form of edge protection should be used to isolate workers from a fall. This includes working on single-story buildings and structures. Using the existing scaffolding as edge protection is often the simplest solution. If this is not practicable, then elevating work platforms or temporary work platforms should be used. Toe boards should be fixed to temporary edge protection as a way of containing all materials, including debris and loose tools.
Worksite traffic can be a major cause of harm on work sites. When it’s close to having your frames and trusses delivered to site and you’re considering dates with the delivery company, it is essential to communicate the traffic management plan with them. This provides the company and drivers involved with a clear picture of how the site has been structured and can assist the delivery company in selecting the correct sized vehicle for the delivery, taking into account the site size and structure.
Ensuring that you implement the above can prevent many injuries on site, as well as regular toolboxes, making plans for ‘what if’ situations (rescue plans) and discussing these with your workers to keep them alert so they’ll know what to do if an incident occurs on-site.
For some useful information on the safe installation of roof trusses and framing please view these resources:
WorkSafe Victoria: Safe erection of roof trusses
WorkSafe Victoria: Preparing to erect timber wall frames
SafeWork Australia Managing the risks of falls in housing construction