We know chatting to your team about health and safety isn’t the most exciting topic, however it is the most important! Health and safety is the responsibility of everyone on-site, so it’s important to get your team and subbies involved. Thankfully it’s easy to get started, simply scan in/out of site every day.
As the main builder on-site, one of the timesaving HazardCo tools at your fingertips is the site-specific QR code located on your HazardCo Hazard Board. Getting everyone to scan in and out every day benefits you because:
- Even if you’re not on-site you still know who is – and it’s all saved in your HazardCo Hub so you can check the site history whenever you need to.
- Anyone scanning in for the first time can complete a site induction where the worker is made aware of important site specific information such as emergency contacts and site safety rules.
- Gives workers quick and easy access to the Site Specific Safety Plan (SSSP) which covers important information around some key things like:
- health and safety roles and responsibilities
- Key hazards and control measures onsite
- Incident and emergency management
- On Project Plus sites, HazardCo’s Digital Site Noticeboard feature enables workers scanning in the ability to view site specific notices on their HazardCo App, where you can communicate any hazards or risks that may be present on-site.
- Simply scanning in gives people an important daily reminder to be aware of health and safety – and we all know the more we think and talk about safety , the more we look out for hazards and ways to control the risks on-site.
- Getting everyone’s participation shares the health and safety responsibility with everyone on-site.
If previously you’ve had subbies or team members who don’t use the QR code to scan in/out daily, here are a few ideas to get them using the QR code regularly:
- Use your next Toolbox Meeting to walk everyone through the process of scanning in and out using the QR code on your Hazard Boards, making sure the team has the HazardCo App downloaded and set up.
- If you need to use some incentive, you could shout the team pizza and a cold beverage on Friday afternoon if everyone scans in and out every day that week… it gets the team working together to remind each other.
- You could make it part of your contract with any new subbies, and add it to the employment agreement you have with your own team. Or, go a step further and require subbies to be HazardCo members in order to win contracts on your projects.
There are lots of good reasons to get everyone scanning that QR code so get your team on board with it today.
Construction work involves many businesses and undertakings involved in the same task or activity (for example suppliers, contractors, and building owners). This means there may be multiple businesses that owe a duty to workers and other persons.
There may be multiple people or businesses that are responsible for the duty of care to workers and others on-site. Therefore, more than one person can have the same duty. When it comes to sharing duties, all parties have responsibility. In these situations, all parties need to consult, coordinate and cooperate so they can all meet their shared responsibilities.
Some examples of duties you are likely to share include*:
- Managing risk
Identifying hazards, assessing, and controlling the risks. If the risk cannot be eliminated, minimise it. Regularly review your controls to ensure they are effective
- Worker consultation, engagement, participation, and representation
Ensure that workers are consulted. This involves sharing information, giving workers a reasonable opportunity to express views, and taking those views into account before making decisions on health and safety matters. Consultation may also occur through the builder talking to subcontractors and asking them to share information with the subcontractors’ workers and pass any feedback back to the builder.
- Information, Training, and Instruction
Ensure that workers receive relevant information, training, and instruction to protect every individual from risks to their health and safety arising from construction work carried out.
- Notification
If a notifiable event occurs, you must notify the Regulator as soon as you become aware of the event.
- First aid
Ensure that your workers have access to first aid equipment and trained first aiders. If you share a workplace with other businesses, you can coordinate sharing first-aid resources with them.
- Emergency plans
You have a duty to prepare, maintain and implement an emergency plan at your work. Consult, cooperate and coordinate with other businesses that you share overlapping duties with to coordinate emergency procedures.
What are some ways you can ensure that people are not harmed, and that you are complying with your legal obligations?
- Set clear health and safety expectations and incorporate these into your agreements with contractors
- Ensure contractors have appropriate health and safety procedures in place
- Prepare a Site Specific Safety Plan (SSSP) for the job and share it with all workers and contractors. A SSSP, also known as a WHS Management Plan or Health and Safety Coordination Plan, may be required by your relevant state/territory (based on a contract value or in the case of WA, the number of persons likely to be on-site)
- Establish health and safety reporting requirements with your contractors. A great tool for this is to use the HazardCo App to complete SWMS, Risk Assessments, site reviews, Incident Reports, and more.
- Ensure site inductions take place. Communicate site rules and procedures to everyone who accesses the site.
- Get workers to sign in and out of the site. This can be done via the HazardCo App by scanning the QR code located on your Hazard Board.
- Set up clear requirements for information sharing for the duration of the project
- Ensure that there is effective communication between all parties (e.g. Toolbox Meetings through the HazardCo App)
- Monitor your workers and/or contractors you engage
* This is not a full list of duties, it is important to make yourself familiar with health and safety duties for your relevant state/territory or talk to our Advisory team if you have any questions.
The Toolbox Meeting feature on the HazardCo App means you’ll no longer have to carry around paperwork for your meetings. Our app makes it easy for you to keep energy levels high and hold everyone’s attention with short and focused talks. With the HazardCo App running on your smartphone, you can easily move the meeting to the most relevant place on-site. One man band? No worries, you can use the toolbox feature to capture conversations when you talk to other subbies on-site.
On the HazardCo App, the Toolbox Meeting feature guides you through a team chat with an easy to follow guide that helps you cover all the necessary points and capture key details as you go. It means you don’t need to do any special preparation for your toolbox meeting, just make the time, follow the app, and you’ll get a completed report on the Hub at the end which you can download or email to others. Plus, save yourself some time by using your voice to text feature on your phone which comes as part of most Android and iPhone devices, look for the microphone icon on the keyboard pop up. You can also record attendees with a photo.
Using HazardCo Toolbox Meetings gives you another easy way to keep the team involved too – simply get someone different to run the meeting each week. It keeps everyone thinking more about health and safety, and it shares the admin around. And did you know that the Toolbox Meeting feature isn’t just for toolboxes, you can also use it to conduct safety meetings, pre-start meetings, and committee meetings.
Toolbox Meetings are a vital component of keeping your site safe, and with HazardCo in the palm of your hand, you have all the tools you need for great toolbox meetings with your wider crew.
You might have heard some rumblings that Western Australia is introducing new Work Health and Safety (WHS) laws. Work started on modernising the WHS laws way back in 2017, and after a heap of industry consultation, the new rules will be in place from 31st March 2022.
It’s a bit to get your head around, so we’ve summarised the main things you need to know as a residential builder in WA.
What is happening?
The new laws are largely based on the national model used in other states and territories, so companies will now have similar obligations and requirements across Australia (except Victoria who like to be a bit different and do their own thing).
The WHS Act is supported by three sets of industry specific regulations to suit WA’s unique conditions. One is the “Work Health and Safety Regulations (General)” which applies to all workplaces including the residential building industry. The other two are for Mining and Petroleum industries so we won’t focus on them.
Why the change?
The new WHS laws are intended to improve the protection of workers by factoring in modern employment agreements, higher penalties for companies and individuals, and introducing the term ‘person conducting a business or undertaking’ (PCBU).
Did WA adopt all the clauses from the national model WHS laws?
Some sections of the WHS laws were tailored for WA following extensive consultation. The term ‘Not used’ has replaced any clauses that don’t apply in WA.
Will there be a transition period for businesses to adopt the new laws?
Transitional arrangements will be put into place where duties are new or are substantially changed from existing requirements.
Keep in mind, the systems for identifying, assessing and controlling known hazards should already be in place, as both the WHS legislation and the previous occupational safety and health legislation already focused on the elimination or minimisation of risks.
What are some of the key changes to what is currently in place?
Based on extensive consultation and recommendations, key changes by the government include:
- Terms and definitions including the new term PCBU
- Industrial manslaughter and increase in penalties
- Prohibition on insurance for monetary penalties;
- Union right of entry was retained in the Industrial Relations Act 1979 and not included in the WHS Act; and
- A specific duty is included for providers of work health and safety services to ensure those services do not pose a risk to persons at the workplace.
What the heck is a PCBU?
PCBU is a new term and stands for Person Conducting a Business or Undertaking. This term is used throughout WHS legislation to describe all forms of modern working arrangements. As well as an employer, a PCBU can be a:
- A builder (including principal contractors and sub-contractors)
- Corporation
- Association
- Partnership
- Sole trader
PCBUs have a duty to ensure the health and safety of their workers and others like visitors and volunteers.
PCBUs have the equal duty of care to a worker, even if there are multiple PCBUs involved. For example, if you employ a contractor who brings in a labour hire worker, you, the contractor and the labour hire company all share the same duty of care to that labour hire worker. So if an incident occurs, you can all be prosecuted under the WA WHS Act.
What is Management of Control?
Management of control (MoC) is when the PCBU has MoC of the workplace, where they are required to ensure that the means of entering and exiting the workplace and anything arising from the workplace are without risks to the health and safety of any person.
Who is the Principal Contractor (PC) on a construction site?
A PCBU that commissions a construction project is the Principal Contractor for the project. That person can engage another PCBU as the Principal Contractor and authorise them to have MoC of the workplace.
A construction project can only have one Principal Contractor at any specific time.
Find out more about how how you can work with other PCBUs as the principal contractor
What are the changes to Industrial Manslaughter?
The new offense of industrial manslaughter provides substantial penalties for PCBUs where a failure to comply with a WHS duty causes the death of an individual, in circumstances where the PCBU knew the conduct could cause death or serious harm.
The criteria for convicting someone for industrial manslaughter under the WHS Act is the same as convicting someone under the current WA gross negligence law. But the WHS Act states that prosecutors no longer have to convict the company to be able to convict individual company officers.
The WHS Act includes a penalty provision for industrial manslaughter. The maximum penalty for an individual for industrial manslaughter is $5 million and up to 20 years in prison, but penalties vary based on many factors.
What are the changes to Insurance?
If you’re prosecuted under the current OHS Act, your insurance can pay for your legal fees and your penalties.
Once the WHS Laws comes into effect, your insurance can still pay for your legal fees, but when it comes to paying the penalty, company officers and PCBUs cannot take out insurance to cover fines for breaches.
What does this mean for me?
Both the old laws and the new laws require you to have systems in place to identify, assess and control hazards.
These new laws are a good prompt to take stock of your current health and safety practices and make sure you’re protecting both your crew on site as well as your business. Here is the WHS laws checklist with advice on the key things you should be ticking off when it comes to your project site.
If you’re not yet a HazardCo member, sign up for a free trial today. We can help you get your health and safety sorted – making it simple and easy to manage but without cutting corners.
We’re here to support you, so don’t hesitate to get in touch for a chat if you have any questions or concerns. Give us a call on 1800 954 702 or email info@hazardco.com.
More information
Whenever you have an incident on site, whether it be big, small, or a near miss, you should record it in your incident register for your records, which is included in your HazardCo App. By reporting and investigating an incident, you will find the cause, but you are also likely to identify other areas where improvements can be made.
In some cases, you may also need to notify your state regular about the incident. WorkSafe Victoria has recently announced changes to the threshold of what is considered notifiable. Your HazardCo membership includes 24/7 incident support with the advisory team, so if you have an incident on site and you’re not sure if you need to notify the regulator, just give us a call and we will provide advice and walk you through the steps you need to take.
What is changing?
WorkSafe Victoria has revised the threshold for incidents that are notifiable.
When an incident occurs that doesn’t result in a serious injury, the threshold for whether it is notable was “incidents exposing a person in the immediate vicinity to an immediate risk”. The threshold is changing to incidents “exposing a person to a serious risk to the person’s health or safety emanating from an immediate or imminent exposure to a hazard”.
What is considered a serious risk?
WorkSafe considers that the term ‘serious risk to the health or safety of a person’ means:
- that exposure to the incident created a risk which, if it had eventuated, could have resulted in death or a serious injury or illness of a person (seriousness of potential harm), and
- the level of risk was not minor, in that there was a real likelihood of the risk eventuating (likelihood of incident occurring)
We now need to notify WorkSafe of incidents involving imminent exposure to hazards, why is this?
The amendments allow regulations to include certain illnesses as incidents for the purposes of notification. Illnesses could include large-scale, infectious diseases posing a serious health risk, like COVID-19, serious illnesses acquired in workplaces, like silicosis, and, potentially, work-related transmissible diseases.
Any other changes I need to know about?
WorkSafe has also stated that “Incidents relating to the collapse, overturning, failure or malfunction of, or damage to, plant will become notifiable if that plant is prescribed under regulations. The current provision that prescribed plant can only be used if licenced or registered is now outdated because Victoria no longer has a plant licensing regime.” This will be relevant to you if you use boom type mobile elevated work platforms and concrete placing booms.
How does this impact me?
Long story short, keep reporting all incidents (big and small) into your incident register using the HazardCo app so that you can learn from these experiences and you have proper documentation. If you have an incident on site, give us a call and we will provide advice on whether you should notify the regulator. If you do, we will walk you through the steps and be available for advice along the way.
When does this change come into play?
Effective from 17 March 2022.
We’re here to support you, so don’t hesitate to get in touch for a chat if you have any questions or concerns. Give us a call on 1800 954 702 or email info@hazardco.com.
For more information about these changes, visit the WorkSafe Victoria website.
WorkSafe Victoria has announced the reasons for issuing a prohibition notice have changed. Here’s what you need to know.
What’s changing?
WorkSafe inspectors in Victoria will now issue a prohibition notice if they think an activity “involves or will involve a serious risk to the health and safety of a person from an immediate or imminent exposure to a hazard.”
Under these circumstances WorkSafe inspections will also be allowed to give verbal or written directions. The directions are effective immediately and will be used to stop dangerous activity while the prohibition notice is being processed.
How is this different to what happened before?
Previously, WorkSafe could only issue a Prohibition notice if the risk had an “immediate health and safety risk or consequence”. WorkSafe inspectors can now issue a prohibition notice or give a direction relating to non-immediate yet serious health and safety risks and prohibit an activity until satisfied the risks have been addressed and the workplace made safe.
Does this mean businesses will shut down?
Prohibition notices are only issued in relation to a particular activity. If the risk is confined to a specific activity the entire workplace won’t be shut down.
I’m a small building company doing a handful of builds a year, do I need to worry about this?
Yes, all duty holders may be impacted.
Activities that pose a serious risk to health and safety of a person, arising from an immediate or imminent exposure to a hazard, can be prohibited by WorkSafe until the activity no longer poses that risk.
You need to be aware of these changes and to comply with any notices issued.
When is this happening?
Changes are effective from 17 March 2022.
We’re here to support you, so don’t hesitate to get in touch for a chat if you have any questions or concerns. Give us a call on 1800 954 702 or email info@hazardco.com.
For more information about these changes, visit the WorkSafe Victoria website.
FieldPulse, a powerful job management app for service providers, today announced its partnership with HazardCo, a top health and safety management company.
This strategic partnership brings together two leading systems that are revolutionising the way tradies do business. The partnership will feature comprehensive integrations for both the FieldPulse and HazardCo apps.
“FieldPulse’s partnership with HazardCo provides a solution for health and workplace safety that no other job management software can compete with. We’re very excited to begin this new chapter with the HazardCo team, and look forward to expanding our partnership offerings as FieldPulse continues to meet the wide-ranging needs of tradies everywhere,” said Bobby Shuey, Vice President of Channel Partnerships and Strategy at FieldPulse.
FieldPulse users can now access their important SWMS documents via the FieldPulse app, while HazardCo users can utilise FieldPulse’s job management software to better organise and structure their businesses.
Iain Dixon, Chief Executive at HazardCo says “Our goal is to help builders and tradies to feel confident they are keeping themselves, their crew, and their business safe. The new integration between HazardCo and FieldPulse brings health and safety tools into the daily job management process, making it faster and easier to complete H&S administration without cutting corners. We are pleased to be working with FieldPulse and know many trades will benefit from the end-to-end solution we can provide together.”
This partnership is the latest milestone in FieldPulse’s expansion into the APAC market. FieldPulse is a premier partner of Reece, Australia’s largest plumbing supplier, providing users with a direct line to Reece’s immense product catalog. With this latest partnership with HazardCo, FieldPulse expands its already growing list of products and services to best serve trade businesses around Australia and New Zealand.
FieldPulse CEO, Gabriel Pinchev, adds “We’re excited to kick things off with HazardCo, as we continue to build on our vision of containing the entire customer workflow within FieldPulse.”
About FieldPulse
Headquartered in Dallas, Texas, FieldPulse is the premium field service management partner for tradies around the world. FieldPulse makes doing the valuable work of the trades easier, thanks to a robust feature set including one-click customer communication, quick and easy invoicing and quoting, simple job scheduling, and more.
About HazardCo
HazardCo is a digital health and safety management system trusted by more than 10,000 businesses across Australia and New Zealand. HazardCo is designed to help Builders and Trades get home safely at the end of every day, providing members with simple guided tools and the very latest health and safety advice.
The boom in building demand last year coupled with Covid-19 restrictions, issues with labour and widespread material shortages caused an avalanche of paperwork and admin.
We talk to hundreds of building companies around the country each week so we’ve got our ear to the ground when it comes to the tech building companies are using to reduce their paperwork burden, propel their businesses forward and improve efficiency.
Here are some of the trends and tools we keep hearing about that will help you to scale up and go faster in 2022.
Estimating and construction management
Lots of small building companies want a single system and tool that will handle everything from the first takeoff to the final invoice. Buildxact is designed for small builders. It will help you stay on top of each job, giving you a clear picture of income and outgoings so you’ll know exactly where your job profit stands. Buildxact members say the estimating and construction management software cuts time spent on takeoffs by 80%. You can upload the PDF and do your takeoff on-screen in minutes, you don’t need paper plans or scale rulers. Measure in a few clicks and price jobs in one step. Buildxact says it takes just two hours to get started.
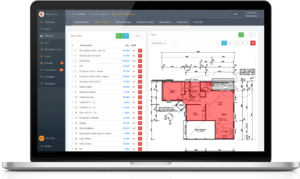
Supplier network platform
Managing your business from an email inbox and sending “quote this” emails to suppliers and trades leads to inaccurate quotes, issues with pricing, rework and delays. BuiltGrid is a supplier network that provides one integrated system for project info, quote comparisons, orders and call ups for all materials, trades and services. If you’re building five projects a year, time gains have been shown to save builders 54 days. That’s 54 days you can use to secure your next project, focus on your craft or hang out with your family. The best thing about BuiltGrid is that it’s free for builders. Yeah, completely free!
Property information
When a potential client calls you up about a site they’ve just purchased or they are talking about wanting to build a house at the back of their property, did you know you can quickly put the address into Landchecker and view all the information about the site in one place.
It pulls property data from more than 300 sources so you can check things like the site size, planning zones, overlays, previous planning permits and more. You can even turn on high-resolution aerial imagery to get a good look at the site, without having to jump into a separate (and expensive) platform like Nearmap. With all this information available at a glance, you will look like a pro to the potential client and will be able to quickly gauge if it’s the type of build that will suit your company.
Landchecker is currently available in Vic, NSW, Qld, Tas and SA and has more than 3000 builders regularly using the platform.
Site deliveries
If you’ve ever had UberEats delivered and thought “I wish it was this easy to get supplies delivered to my site”, there are some excellent platforms available that will do just that.
If the crew on-site run out of nails or need some supplies delivered quickly, just open up an app like DeliverTrade, select what you want, and when you want it delivered. Everyone on site can focus on the task at hand, rather than dropping tools to do a run to Mitre10, and you’ll get less calls to “pick up a few things” while you are out and about.
DeliverTrade is currently available in Melbourne and Adelaide, with plans to roll out availability across Sydney, Brisbane and Gold Coast over the coming months.
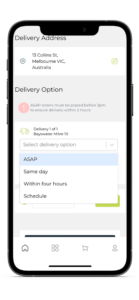
Get supplies delivered to site ASAP with DeliverTrade, or schedule ahead of time.
Qualified lead generation
If you want to scale up but would rather spend time on the tools rather than building your network and looking for new clients, there are lots of ways you can promote your business online. The iBuildNew.com.au is a leading online platform for new home construction that can get your business in front of people actively looking for custom builders. The iBuild New Home Advisor team will qualify the home buyer, so they will be highly qualified and matched to your building company.
Health and safety management system
Cut the time you spend on WHS admin, without cutting corners. In a 2021 survey, HazardCo members said they complete their health and safety admin in half the time since switching from traditional paper-based systems. It’s a fully guided system designed for building companies, that comes with all the reports and templates you need loaded up and ready to go. So even if you’re not a health and safety guru, you will feel confident you are keeping your crew and business safe. HazardCo members also get access to free advisory support, so you will know you have a team of WHS experts on hand to give advice when you need it. If you have an incident on site the team will support you through the process.
HazardCo is used by more than 10,000 businesses across Australia and New Zealand.
Using machinery and equipment for work on-site puts workers in close contact with powerful and fast moving tools. This makes getting the job done easier and more efficient but it does also present some risks to workers health and safety. If a worker comes into contact with machinery or equipment in an unsafe way, it can cause significant harm or injury. It is common practice to use guarding on machinery and equipment to create a barrier between the workers and the moving parts that can cause harm or injury.
Common risks and Hazards
Machinery and equipment guarding is designed to eliminate or minimise the risk of workers being harmed while completing their work. It is important to assess the hazards and risks involved with all the machinery and equipment used in the workplace. If machinery and equipment is not guarded properly, workers can sustain significant injuries due to coming in contact with moving parts.
Some common injuries are:
- Cuts
- Burns
- Electric Shocks
- Degloving
- Amputations
Because there is potential for serious harm when using machinery and equipment, it is necessary to plan a safe approach when conducting a job. This will help identify the hazards of working with machinery and equipment.
The hazard management process includes:
- Identifying hazards
- Assessing the hazard – decide if the identified hazards are significant
- Assessing the risk – decide how likely and seriously a worker could be harmed
- Controlling the hazard – either by eliminating, isolating or minimising the hazard
- Regularly reviewing and monitoring the hazards and risks.
- Create safe working methods like Standard Operating Procedures (SOP)
Choosing the right guarding
There are many different types of guards that can be used to protect workers from being harmed when using machinery and equipment. Here are some common types of guarding and examples of when they are used:
- Fixed – Screwed or fixed in place guarding to protect users from hazards. – E.g. grinders
- Self closing – the cutting edge only opens to the extent necessary to cut the workpiece E.g. drop saw
- Adjustable – Safety guarding that is movable. The guard is in place to protect the user but moves to allow the function of the tool. E.g. drop saws and skill saws
When choosing a guard, It is important to make sure the guard can actually prevent an operator from reaching into the dangerous parts of machinery and equipment. To make sure the operators are protected from the dangerous parts, the safest guarding must take into account an operator’s ability to reach into or come in contact with moving parts.
There are many different types of guards to choose from. It is important to choose guards that eliminate the potential for harm. If this is not possible, then guards should be chosen that isolate or minimise the risk to workers. It is very important that guarding is not removed or tampered with as this will increase the risk of harm to workers.
Control hierarchy
- Elimination involves removing the risk to health and safety from the work site. It is the most effective risk control and should always be prioritised.
- Minimisation is used when a risk cannot be eliminated. This is done using: substitution, isolation, engineering, administration and PPE.
Training/ Competency
Workers should be trained to competently complete the work they are required to do. Workers should be trained and educated on the purpose and function of the different types of guarding in the workplace. Make sure that workers have the appropriate training, supervision, and qualification (if required) to safely use the necessary machinery and equipment. Keep an up-to-date register of what machinery and equipment workers are trained on and competent in using.
If you have any questions about guarding machinery and equipment, give HazardCo a call on 1800 954 702.
Our partners BuiltGrid help residential builders work more efficiently with their suppliers and trades to get projects delivered on time and budget. While you may use estimation software to get rough costings to bid on a customer project or set a budget on a spec home, BuiltGrid comes into play once you have council approval. It allows builders to get competitive quotes matching project needs, side-by-side quote comparisons and lock in materials and labour when you need them. All your supplier admin and communications are together, saving you time and minimising costly errors. Better still, builders don’t pay a cent to use the BuiltGrid platform.
Running a business from an email inbox
Although it’s common practice for small businesses to manage their business from an email inbox, email was never designed to be used that way. Searching years of email history may be useful at times but it’s difficult to find important messages or specific attachments unless you’re super disciplined with folders and labels. BuiltGrid clears your email inbox by linking all of your project docs, quotes, orders, communications and call-ups in one place. Supply partners get selective access to project information and you only get critical notifications.
Select suppliers. Attach a plan. Hit “Send”
“Geez!” is the first response from suppliers and trades when they receive a “Quote this” email with an attached plan and little else. Yet, this is the go-to method used by most builders to request quotes. It’s way too common, attracting inaccurate quotes, pricing issues, delays and rework. The free alternative is to use BuiltGrid’s industry standardised quote request and job scope framework – your suppliers and hip pocket will thank you.
Quote received. Now what?
Admin hassles only start with the “Quote this” email. What about following up suppliers, answering phone calls and questions, making changes, re-quote requests? Quote responses are sent at different times and based on a supplier’s interpretation with varying inclusions, exclusions and terms. It’s messy, time consuming and why most supplier selections are based on a quick view of the quote price! BuiltGrid shows you side-by-side competitive quote comparisons so you can assess where the real value is, beyond price. One-click quote acceptance locks in your supply and notifies unsuccessful suppliers – no more pesky suppliers chasing a deal.
Save 54 days and $39,051 this year
In short, BuiltGrid provides one integrated system for project info, quotes, comparisons, job orders and call-ups. If you’re building five projects a year, time gains have been shown to save builders 54 days. Applying a base hourly rate, that’s $39,051 in your pocket. On top of this, there’s additional profit margins from builders inviting more competition from the broader network. Use the time gained to secure your next project, focus on your craft or hang out with your family.
As a HazardCo member we know you value your time. Now there’s a better way to manage your quoting, ordering and call-ups. And it’s free! Yep, BuiltGrid is free to builders!
Join the free BuiltGrid network now
Looking for something in particular?
Working with heavy machinery and managing traffic on-site can be risky. But with the right checks and planning, we can keep everyone safe.
Daily machinery checks
Before starting work each da...
Demolition machinery
Working with heavy machinery can be dangerous. Incorrect use or untrained operators can lead to serious injuries or worse.
Training and supervision
Machinery sho...
Digging into the ground might seem straightforward, but excavation work is actually one of the most dangerous parts of construction. That’s why it’s important to plan ahead and put the right s...
When you're able to get back on site after a flood or storm, here are the hazards, risks and control measures you should consider to help reduce the risk of injury and illness to yourself, you...
Dust is a common hazard in the construction industry, especially during demolition or refurbishment. When buildings are demolished they can release materials that create hazardous dust (airbor...
The holiday season is over and now it’s time to get back into the swing of things. Coming back to work and reopening your site is just as important as shutting it down. The New Year is the per...
The holiday season is almost upon us, and we’re all eager to have a bit of a rest, recharge, and spend quality time with our families. As we wind up 2024, it is a demanding time for constructi...
When you have an incident on-site, whether it’s a near miss, an injury, or a work-related illness, it’s important to document an incident report.
Incident reports don’t need to be time-cons...
Anything with wheels and an engine should be at the forefront of your mind on site.
From delivery trucks to excavators, if it moves, and it’s got some weight… then that means power! it’s g...
Electricity is essential on construction sites, but if the risks are not managed properly, it can pose serious dangers to people and property. Proper controls must be in place wherever electri...
Health and safety is a core part of any business but incidents and injuries on the job can still happen. According to SafeWork Australia, in the construction industry alone there were 15,877 s...
The HazardCo App has a new Plant/Machinery Pre-Start tool! It’s a quick and easy way to do pre-start checks on various plant and machinery such as scissor lists, boom lifts and excavators. Jus...