If an incident happens at work and your first thought is paperwork, you’re doing health and safety wrong.
Reporting incidents and near misses is vital to good business, and that begins with a ‘safety differently’ approach. A prevention before cure attitude. One that sees incidents reported immediately and investigated thoroughly.
Time and time again we see incidents happen and fingers pointed. What is absolutely vital for your business is a health and safety culture that involves no blame, is open, honest and educated. How do you nurture this culture? You need the right tools.
Where to document and register all incidents
You don’t need to over complicate matters here. Incidents and near misses should be registered in one convenient place that is easy to manage and draw upon when needed.
The HazardCo App has been designed with just this in mind. Simply login, report who was involved in the incident, what treatment was required, and the details surrounding what happened.
All of this information is then stored automatically as an incident register on the HazardCo Hub for you to access and view anytime.
What incidents should you report
You should report all health and safety incidents or near misses that happen at work. These can be incidents that affect you, your workers, or anyone on-site.
Why you should be reporting incidents
Every single worker plays a part in protecting ourselves and one another in the workplace. By reporting incidents you are helping identify areas where you can work together to improve health and safety, and potentially save lives.
Learning from Incidents
It’s important that when incidents occur, time is taken to review and learn from them.
Depending on the complexity of the incident, learning from it might be as simple as meeting with the team afterward to figure out what went wrong, and what can be done to stop it from happening again. Some incidents may need more investigation to help find out exactly what happened and why.
Not your job?
Yes, it is. And that’s why we are so proud of what we do. The HazardCo App and Hub puts health and safety in everyone’s hands, so everyone is protecting their workforce and working safely.
By reporting and investigating an incident, you will find the cause, but you are also likely to identify other areas where improvements can be made. Investigations aren’t about blame and punishment but learning and improving.
No workplace is perfect, and failure will occur. Let your workers know this, and that blame is off the table. This is about making sure everyone is safe and able to get on with the job at hand.
Educate to empower, and enable your workforce to sort their safety today.
HazardCo incident support: When the going gets tough, we’ll be there
All Complete, Premium and Standard HazardCo members receive incident support as part of their plan.
If you have an incident on-site, get in touch and we will help you work out if it’s notifiable to your State/ Territory Regulator and guide you through the next steps. Incidents on-site are stressful for everyone involved, so we will make sure you are following the right processes.
We’re here to help. Reach out to our team if you have any questions or need health and safety advice.
1800 954 702 | info@hazardco.com
If a worker performs an activity that is carried out alone, in isolation or in a remote location, without close or direct supervision, this is commonly referred to as lone working.
Lone working can increase the health and safety risks of any job. Workers may be isolated from support and assistance because of where or when they’re working, or the nature of the work they are doing.
While working alongside your team may not be an option, looking out for your workers should be a top priority.
Lone working includes:
- Traveling alone as part of the job
- Traveling long distances
- Working in remote or isolated locations
- Working unsupervised for an extended period of time – this includes in a separate area away from other workers on larger sites.
- Working late night or shift work
If this sounds like your workforce, then it’s important you minimise the risks associated with lone working. This can be achieved by effective planning and consultation with your lone workers.
Identify the hazards and understand the risks
- Have a look at your site/s to determine when work may be undertaken alone, in isolation or in remote locations.
- Think about the specific tasks / activities that may be undertaken
- Consider what special work considerations may occur e.g. irregular work, breakdown and emergency work that may result in lone working
- How long and what time of day will lone working take place, considering factors such as fatigue and focus
- Have a think about what types of incidents could occur and the access to emergency services
- Are there medical conditions and/or restrictions to the worker/s
- Consider the risks to mental health due to lone working
- Think about dangerous conditions, environmental impacts and other contributing factors that may make the work more hazardous
Agree on suitable control measures
We have put together some recommendations for you to consider, in consultation with your team, when looking at ways to ensure workers can perform their job safely:
- Try and eliminate the need for lone work in the first place. Identify tasks that don’t need to be conducted alone or in isolation. Look at frequency, duration, time of day and look at suitable ways that may make it possible to have supervision or a co-worker.
- Provide information and instruction, such as safe work procedures, on how to perform a task safely whilst lone working
- Ensure workers are trained and competent in the task being completed (not an apprentice or inexperienced worker).
- Agree on a way to regularly check in on your lone workers. Ensure it’s discussed and agreed to prior to the work commencing. This could be a simple phone call, group messages or video calls at agreed intervals. Don’t underestimate the power of human interaction in these times.
- Make sure you arrange regular catch-ups with lone workers by keeping the lines of communication open with everyone. Just because they aren’t next to you on-site, doesn’t mean they should be less informed. Depending on the duration and work involved, consider getting them to check in virtually to a toolbox meeting for example so they still receive team updates and can feel connected.
- Establish limits / restrictions to work activities e.g. what tasks are prohibited from being authorised to perform – like no high risk construction work will be performed by lone workers.
- Provide First Aid training, first aid kit, correct tools/equipment and PPE to lone worker/s. If a fire extinguisher needs to be made available, check that it has been inspected within the last 6 months.
- Emergencies can be more serious if there’s no one around to assist, give first aid or call for help. Ensure emergency protocols are established, such as creating an emergency plan, and that it is suitable considering the types of emergencies which may arise. Determine how the worker/s can raise the alarm / alert someone e.g. providing duress alarms or alert systems so workers can call for emergency assistance or need to discreetly raise an alarm. Two way radios and mobile phones may also be considered.
- Establish security procedures to protect workers from violence or other factors, where applicable
- Look at GPS or location trackers for those working in isolated or remote locations.
Being proactive and prepared will help you to better manage the risks associated with lone working. The biggest tip we can give you is to look out for your team as if they were still with you on-site, or in the office.
Nail guns are used frequently on construction jobs, including in residential construction. Like all power tools, nail guns can cause serious injury. Nail gun injuries can happen due to accidental discharges whilst moving, carrying, and repositioning. Injury can also happen when fired nails strike other nails or timber knots causing them to ricochet. Incidents also occur when workers accidentally place themselves into positions where they are directly exposed to the projectile path of a nail gun.
The risk of a nail gun injury is greatly increased when using a contact trigger (bump fire or multishot) compared to using a full sequential trigger (single-shot). Most injuries occur when the nail gun is set to ‘bump fire’ mode, resulting in penetrating wounds to the operator or nearby workers.
It’s important you review the type of nail gun trigger system and the extent of information,instruction and training given to workers, particularly inexperienced and young workers.
Tips for managing the risks on site
There are a number of ways to reduce the risk of injuries. We have put together a few suggestions below and we encourage you to consult with your workers about how you can work together to ensure safe nail gun use on-site :
- Replace bump fire nail guns with full sequential trigger guns, where possible. A full sequential trigger is always the safest trigger mechanism for the job. It reduces the risk of unintentional nail discharge and double fires.
Note: Bump-fire nail guns potentially may be used to reduce the risk of musculoskeletal injuries (e.g. strains and sprains) for jobs that involve high volume production and repetitive tasks. In these circumstances, ensure only highly experienced and skilled workers use these types of nail guns and implement other additional control measures to reduce the risk of injury.
- When working at height, operators should work from a platform as nail guns are designed to be used with two hands and recoil when fired
- Ensure nail guns are not held above the line of the workers shoulders
- Keep other workers well away from the area where the nail gun is being used
- Maintain nail guns to ensure correct operation of the actuation mechanism. If any problems occur, have it repaired by a competent person or replace it. Do not continue to use a malfunctioning nail gun.
- Inspect timber surfaces for cracks or knots prior to their use
- Provide workers with training and instruction in their safe operation and any other specific direction provided in the manufacturer’s manual including what to do if the nail gun malfunctions. in addition:
- Carpenters should only use nail guns once adequately trained and deemed competent to use them.
- Apprentices should only use nail guns under direct supervision
- Provide suitable PPE such as eye protection, hearing protection and additional personal protective equipment
While many industries seem to have recovered post-pandemic, the construction sector is still battling tough conditions.
It’s important to keep on top of your business processes to reduce headaches later down the track. Whether it’s your invoicing, your insurance, or your health and safety, neglecting these things can really hurt later on. Some businesses are choosing to take this time to invest in their current systems and processes, to help them to build a more resilient business that can respond to the market.
Scaled back?
If your business has scaled back a bit, such as cutting back on help, switching to smaller renovation projects, or you plan to really tighten the belt on the budget for a while, we’re here to remind you to prioritise your H&S. As long as you or your team are on the tools, you need to manage health and safety effectively. This means:
- Ensuring processes and controls remain in place
- Frequently reviewing risk management procedures
- Continuing accurate and compliant record-keeping habits
HazardCo is the simplest, best way to nail health and safety
The HazardCo system helps you to manage your health and safety in the simplest way possible, so you’ll feel confident you are keeping your team and your business safe. The system is designed especially for home builders, and comes with all the reports and templates you need, loaded up with advice provided by experts
Key benefits include:
- Site-specific safety plan generator – Create a site specific plan in minutes
- Hazard board with QR code – Workers on site scan in and complete induction, so you know who is on-site at all times
- On-site App – Workers can complete and collect SWMS, incident reports and more
- Automated contractor management – Collect insurances, proof of WHS and more
- Unlimited WHS advice – Advice and assistance over the phone
- 24/7 incident support – Support throughout the incident reporting process
The Key Takeaway
Health and safety should never take a back seat. It’s still as crucial as it’s ever been and HazardCo’s here to keep you out of strife.
Get a free 7-day trial of the HazardCo health and safety system.
As a plumber, you know your business runs better when you’ve got a good process to manage your jobs. But keeping your job management in top form can be a hard task when you’re on the tools everyday.
Time is money, so the less time you spend making calls to confirm service details or buying materials, the more billable hours you have to complete work. To run your business in a more efficient and profitable way you need to be making the most of your time, instead of getting bogged down by admin.
Here’s how a job management app can streamline your daily processes to bring maximum benefit to your business:
No more hunting for documents
If your team is using paper quotes or sending ad hoc emails, you’ll be wasting precious time every week trying to find this information when you need it. An app-based job management solution stores all of the information you need in one place so you can find all the details you need, when you need them.
Know exactly where your team is
Do you find you’re frequently making calls to your team to stay on top of what they’re working on and what jobs have been completed? On the flip side, do you find your team calling throughout the day wondering where they should be and when?
Remove the need for these calls with a job management app that shares all job information automatically between you and your team members. Simply log on and you’ll see exactly where your team is, what jobs have been completed, and any other info that you need for the day. All in one convenient place.
Never double up again
A top-tier job management solution cuts down on double data entry and saves you time transferring data between quotes, accounting systems, timesheets, and payroll. By housing all of your information in one central location, all of your data populates where it needs to be so you can say goodbye to unnecessary manual data entry.
Create happier customers
From staying current on all projects to collecting invoices, keeping on top of your customer data is a huge part of your business. A job management solution does more than just keep your contact list in order, it also connects all the information you need to run your business such as current quotes or invoices and past jobs. That way, you can keep your customer history in order, as well as being able to easily check in on outstanding items.
The time you save when you partner with a leading job management system will not only benefit your efficiency but also increase your bottom line. Ultimately, it helps you direct your time and energy to where it’s needed most. Luckily for you, we have just the guys in mind.
Introducing FieldPulse
FieldPulse is a job management tool with a bucketload of slick features. They give plumbers the tools they need for customer management, quoting, scheduling, and invoicing. You’ll even be able to search the entire Reece product catalogue with live pricing information and submit purchase orders directly to Reece without having to leave FieldPulse.
With FieldPulse’s system, you can save yourself 10+ hours of admin a week. Plus, FieldPulse members have seen a 60 percent increase in customer enquiries converting into paying customers resulting in an average of five new jobs being scheduled each week. Sounds good? Yeah, we thought so.
Sounds like a plan?
As a HazardCo member, you’ll receive 20% off a month-to-month Fieldpulse membership. Sign up for a yearly membership and receive 25% off!
Get on top of your health and safety with HazardCo and keep track of job management in FieldPulse. It’s a win-win!
Get a free trial of Fieldpulse.
As part of our ongoing partnership with Buildxact, we’ve recently built a connection between our two systems to help residential building companies and renovators further simplify their business processes.
Buildxact is a Software-as-a-Service company specialising in residential construction management systems. Buildxact is headquartered in Melbourne Australia and is used extensively throughout Australia and New Zealand.
We share a common goal of wanting to simplify home construction by offering easy-to-use digital tools. We are excited to bring together two leading systems and help our members work more efficiently. Our shared vision is to empower builders by helping them to transition to digital systems and reduce their paperwork burden.
There has been strong market demand to build a connection between HazardCo and Buildxact. The first version of this connection automatically uploads important health and safety documents created using the HazardCo system directly to Buildxact. By storing project documents, such as estimates, quote letters, invoices, alongside safety documents like SWMS or safety induction notes in one easily accessible location, builders can save time. We are continuing to work with our members to get their feedback on these tools and discover what other functionality would be valuable.
The integration between HazardCo and Buildxact comes at no additional cost to builders who are already using both systems.
An estimate being created using BuildXact:
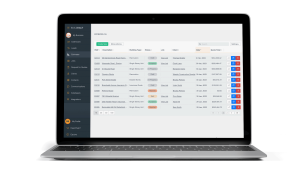
At HazardCo, the safety and well-being of every person on the job site is our top priority. By connecting our leading health and safety system with Buildxact’s residential construction management system, we are providing builders with an integrated solution that enables them to complete their projects efficiently while ensuring a safe working environment.
Learn more about Buildxact and the integration here
Inductions are mandatory on all construction sites and are essential for both yours and your team’s safety. We want to make sure you get home safe at the end of the day, so prioritising your H&S is a must.
Why should I be carrying out site inductions?
A site induction is necessary to inform workers of the dangers and risks associated with their work at the start of each project. No two projects are alike, and each has its own set of teams, tasks, work types, environments, risks, activities, and layout.
It’s important for everyone on-site to have a clear understanding of the risks involved. Site inductions are designed to protect people, so it’s crucial we all do them.
How do I carry out a site induction?
At times, a supervisor may not be available on-site to perform an induction. That’s why we’ve made it easy for everyone to conduct an induction on-site. The HazardCo app allows you to complete a site induction easily and digitally, and it be accessible to your entire team.
Our site induction process includes a QR code that can be scanned on-site, acknowledging and reading the site-specific safety plan. With all the necessary information in one place, workers will know what the site/task-specific arrangements and regulations are.
Conducting site inductions properly can save time, stress, and lives. Get in touch with the HazardCo Team to see how we can help you.
If you’re a HazardCo member, click here to find out more on scanning on-site and completing an induction.
If you’re not, click here for a 7-day free trial.
Angle grinders are versatile hand-held tools that are used regularly in the residential construction industry.
Serious incidents can occur when using grinders onsite. The most common causes of injury to operators and nearby workers from angle grinders are:
- Serious harm if caught by cutting/grinding wheel.
- lacerations from angle grinder kickbacks.
- lacerations from attachments that break and become projectiles.
- Hearing damage from wheels cutting through material.
- Burns from sparks and workpiece surfaces.
What are some control measures to reduce the risk of injury?
Here are some control measures to consider when it comes to managing the risks associated with grinders:
- Determine if an angle grinder is actually the best tool to perform the task, because another tool may be just as, or even more, effective.
- Prior to purchasing a grinder, look at ones with adjustable handles that can be moved to suit both left and right-handed operators.
- Select a grinder that has an automatic cut-off or dead-man switch as part of the handgrip. This is designed to cut off power as soon as finger pressure is released.
- Only use angle grinders that are an appropriate size for the task. Do not use a grinder that is larger, heavier or more powerful than is necessary, as it is much easier to control a lighter tool.
- Ensure guards are never removed. The guard usually covers half of the disc and is positioned between the disc and the operator.
- Ensure that the correct type of disc is used for the task being performed. The wrong disc potentially can shatter or ‘grab’ the workpiece causing kickback.
- Regular maintenance and inspection of the grinder and cutting disc by a competent person, as per the manufacturer’s specifications.
- Provide operators with appropriate information, training, and instruction to ensure the grinder is operated safely and competently.
Before use
Before using an angle grinder, it’s important to check that:
- Guard and handles are secure.
- There are no defects or damage to the disc (a disc that has been dropped may have developed cracks and should not be used).
- Use only the tightening tool supplied by the grinder manufacturer to tighten the disc as other methods can damage the disc and grinder.
- The spindle’s correct disc diameter and central disc hole size are used.
- The correct type of disc is used for the material being cut or ground.
- Make sure the disc is the right way up.
During use
Consider the following safe practices when an angle grinder is in use:
- Always ensure that your work area is well ventilated.
- Position the tool so that the power cord always stays behind the machine during operation.
- Make sure the wheel is not contacting the workpiece before the switch is turned on.
- Before using the grinder, test run the tool at the highest no load speed, and stop immediately if any vibration or wobbling occurs.
- Look out for flying sparks. Hold the tool so that sparks fly away from you, others, and flammable materials.
- Use both hands to operate the grinder. One hand should grip the handle and dead-man switch (if provided), while the other hand supports the weight of the tool.
- Allow the grinder to ‘run up’ to operating speed before applying it to the job.
- Position the grinder against the workpiece with minimum pressure, so the disc does not ‘grab’ and cause it to kickback.
- Keep the grinding disc at a 15 – 30 degree angle to the object. Check that the workpiece is held firmly, either as part of a larger item or in a bench vice.
- Keep the work at waist height during grinding where possible.
- Angle grinders must have stopped turning completely before they are put down or moved around the workplace.
- Before changing discs, remove the plug from the power point.
- Never use a grinding disc for cutting or a cutting disc for grinding.
- Do not touch the workpiece immediately after operation. It may be extremely hot and could burn your skin.
- Ensure correct PPE is worn for the task/ job and review what can get caught in a moving part of the tool. For example:
- Ensure workers do not wear loose clothing or jewelry.
- Long hair is to be tied back so nothing can become caught
- Workers should wear protective clothing such as safety glasses, leather aprons, gloves, face shield (if required), safety boots, RPE (if required) and hearing protection as they will be better protected.
If you’ve got a question about safe grinder use or any other health and safety matter, the HazardCo Advisory Team is here to help. Give them a call on 1800 954 702.
We’re proud to announce the partnership between HazardCo and Mitre 10 Australia to help more builders feel confident they are nailing their health and safety.
We know that many builders need to get on top of their health and safety. In fact, the 2023 State of Residential Construction Industry report stated that 45% of building companies in Australia don’t have an established health and safety system in place at all.
We’ve partnered with Mitre 10, one of the leading trade hardware stores in Australia, to make it easier than ever for builders, renovators and trades to protect their crew and their business with the HazardCo system.
With this Mitre 10 partnership, you can now charge HazardCo to your Mitre 10 trade account, so it’s super easy to get on board.
We pride ourselves on making health and safety easy to understand and simple to action on-site.
Have a chat to your local Mitre 10 trade rep or store, or get in touch with us below.
Email info@hazardco.com | Call 1800 954 702
SWMS templates are great, most of the time. A template will provide a structure so that you don’t miss any important steps, help you to save time, and a good template will even help you to learn more about what controls to put in place to manage the hazards involved in completing the task.
To be effective, your SWMS needs to be specific to the task, the site and the workers carrying it out. Generic SWMS templates don’t cut it. The SWMS needs to lay out the steps that will be taken to carry out the task and then those steps need to be followed. If work is being carried out in a way that doesn’t match the task steps in the SWMS, the work needs to stop.
One SWMS can be prepared to cover various tasks as long as it takes into account the dynamic nature of the work environment and can be easily read and understood by the workers involved. You might find it easier to create a separate SWMS for each high-risk construction work activity, but remember you need to think about how different activities taking place at the same time or how one activity after another could impact each other.
We recommend looking for a SWMS template that will help you to spend less time writing (as that’s the bit that takes the most amount of time). The template should be guided, rather than just an empty shell that needs to be filled in from scratch. Make sure it’s quick and easy to customise. You should be able to easily adjust the hazards, controls and task steps to reflect how the work will be carried out. It should also use simple language everyone understands.
Digital SWMS templates that you can create, review, edit, sign and save on your phone are a great way to get into the habit of doing your SWMS each and every time you are completing high risk construction work. By using a SWMS App, you’ll know you’ve always got the template ready to go in your back pocket and you’ll know you’ve got a full record of all your completed and signed SWMS saved online.
The HazardCo App includes 25-easy to edit templates, or you can use the template builder to create a SWMS. It only takes a few minutes, and it will suggest controls to put in place, based on the common hazards you identify. If you have a similar job coming up, you can save the SWMS as a Favourite and update it on the go to be task and site-specific. Easy as!
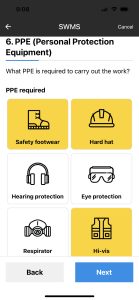
Get a free HazardCo trial.
Learn more about HazardCo SWMS templates and health and safety App.
Looking for something in particular?
Working with heavy machinery and managing traffic on-site can be risky. But with the right checks and planning, we can keep everyone safe.
Daily machinery checks
Before starting work each da...
Demolition machinery
Working with heavy machinery can be dangerous. Incorrect use or untrained operators can lead to serious injuries or worse.
Training and supervision
Machinery sho...
Digging into the ground might seem straightforward, but excavation work is actually one of the most dangerous parts of construction. That’s why it’s important to plan ahead and put the right s...
When you're able to get back on site after a flood or storm, here are the hazards, risks and control measures you should consider to help reduce the risk of injury and illness to yourself, you...
Dust is a common hazard in the construction industry, especially during demolition or refurbishment. When buildings are demolished they can release materials that create hazardous dust (airbor...
The holiday season is over and now it’s time to get back into the swing of things. Coming back to work and reopening your site is just as important as shutting it down. The New Year is the per...
The holiday season is almost upon us, and we’re all eager to have a bit of a rest, recharge, and spend quality time with our families. As we wind up 2024, it is a demanding time for constructi...
When you have an incident on-site, whether it’s a near miss, an injury, or a work-related illness, it’s important to document an incident report.
Incident reports don’t need to be time-cons...
Anything with wheels and an engine should be at the forefront of your mind on site.
From delivery trucks to excavators, if it moves, and it’s got some weight… then that means power! it’s g...
Electricity is essential on construction sites, but if the risks are not managed properly, it can pose serious dangers to people and property. Proper controls must be in place wherever electri...
Health and safety is a core part of any business but incidents and injuries on the job can still happen. According to SafeWork Australia, in the construction industry alone there were 15,877 s...
The HazardCo App has a new Plant/Machinery Pre-Start tool! It’s a quick and easy way to do pre-start checks on various plant and machinery such as scissor lists, boom lifts and excavators. Jus...