You may have heard about the dangers of silica dust. And that it causes a progressive, irreversible, untreatable and potentially fatal disease of the lungs called silicosis.
You may know that dry sandblasting, grinding, cutting, sanding, polishing, and drilling of silica-containing materials like concrete, rock, glass, asphalt, cement and particularly engineered stone are hazardous tasks in construction. Why? Because you create silica dust that is too small to settle. It floats around undetected in the air that is breathed in by you and those around you.
WorkSafe Victoria’s free “stonemans’ screening project” diagnosed 29% of engineered stone workers with silicosis in 2019/2020, and a similar campaign in 2021 in Queensland, Australia, diagnosed 20% of engineered stone workers with silicosis – some are young, and some are without symptoms as yet!
Am I protected if I’m wearing a respirator?
Tiny silica dust particles can penetrate your respirator if you aren’t careful. Make sure your respirator has been fit-tested and isn’t worn over a beard. You must also have the correct filters, as Silica dust is 100 times smaller than sand and can penetrate some filters.
Prevention sounds like a better option! What steps can I take?
Step 1: Understand what happens when you inhale silica dust.
Knowledge will empower you to make wise choices:
- Watch the two-minute video here.
- Thankfully your lungs have built-in traps that catch most impurities and dust. The nose, windpipe and air tubes are lined with mucus membranes. Dust that was not sneezed out, sticks to the mucus and is coughed out, spatted out or swallowed.
- But some respirable crystalline silica/RCS dust escapes these traps and is tiny enough to enter the deepest destination in the lungs where they cause irritation, inflammation and scar tissue formation, even after silica dust exposure is stopped. Widespread, ongoing scar tissue formation reduces the surface area that is left for gas exchange, reducing your oxygen levels.
Step 2: Know the silica content of your construction materials and substitute for less hazardous materials!
- The higher the silica content of the material, the more silica dust is created. For instance the extremely high silica content of engineered stone causes “accelerated silicosis”.
- Stop exposure: the Australian Government has an engineered stone ban. Strict rules now apply if you need to work with already installed engineered stone.
- Lessen exposure: substitute high-silica-content materials for no/low-silica-content materials.
- Examples of the silica content of some of your construction materials:
- Engineered stone: up to 92%!
- Fibre-cement sheeting: 5-40%.
- Concrete and slate: 20-40%.
- Granite/natural stone: 25-60%.
- Silica contents of products like cement can be found in their Safety Data Sheets (SDS).
Are there symptoms to look out for?
Damage to the lungs from silica dust and symptoms of disease may not appear for many years. Workers may not show any symptoms, even at the point of initial diagnosis, which is why prevention and health monitoring are critical. Often workers are diagnosed during routine health monitoring, as chest x-rays may show scar tissue formation even if you are without symptoms. Silicosis symptoms may include a dry cough, shortness of breath, fatigue, fever, chest pain and unexplained weight loss. Silicosis also increases your risk for other conditions like lung cancer, chronic bronchitis, kidney disease and some auto-immune diseases.
What if I’m experiencing some of these symptoms?
Tell your doctor about your current or previous exposure to silica dust. To rule out silicosis, respiratory questionnaires, lung function tests, chest X-rays and CT scans may be required.
Why is health monitoring important?
Early detection of silicosis, before symptoms develop, can motivate you to stop further exposure, and thereby improve your health outcome.
How do I organise health monitoring?
If you were exposed to silica dust currently or in the past, even if you wore respirators and even if you have no symptoms, you need routine health monitoring. Talk to your employer. Tell your doctor about your exposure. Engineered stone workers must see specialist occupational health doctors. Early detection is most important!
Treatment
Treatment is limited to relieving symptoms. For instance, oxygen therapy and bronchodilators will allow you to breathe more easily. Advanced silicosis requires lung transplants.
More Information on how to protect yourself from the risk of inhaling silica dust:
It is important to understand that depending on the State/Territory you are working in, there are very likely specific requirements you need to meet to ensure you are appropriately managing the risks. The state regulators have plenty of information available to learn more. We have provided a few key links below for you:
Call 1800 954 702 or email info@hazardco.com to get in touch with the HazardCo team.
Even if you are self-employed you still carry the same duties under the legislation as the main contractor.
If a contractor, in turn, engages other businesses then they too must assume some of the responsibility for their work. A contractor is most likely to have the greatest influence and control of their own work activities and workers (or contractors).
There should be a way of recording your planning and the ways in which you share this information. All businesses should have access to information to keep themselves or their workers safe.
Your primary duty remains to prevent harm arising from your work. Identify risks that could arise and share information between relevant parties.
The following key steps should be followed by contractors:
Scope
- Engage with the main contractor to identify risks
- If engaging your own contractors share information relating to risks, safety plans and expectations
Prequalify
- Provide the main contractor with evidence to demonstrate your health and safety procedures eg Task Analysis, Safe Work Method Statements, Training Registers
- If engaging contractors of your own, prequalify their procedures. Make sure you are happy with how safely they will work.
- Find out more about HazardCo’s Pre-Qualification Tools here, or get in touch with the team to find out if it’s right for you.
Select
- If engaging your own contractors, select them based Select the contractors based on prequalification outcome and any other factors including availability, skills etc.
Appoint
- Complete risk assessments (e.g. Risk Assessment on the HazardCo App, Task Analysis or other risk management plans).
- Agree these with your workers and other businesses
Monitor
- Complete Risk Assessments/Site inspections/Observations at the start of the day to make the work area is safe to work in
- Hold regular toolbox meeting, so all workers are aware of safety expectations, share this with other contractors on-site where they are affected by your work
- Investigate any incidents and share the findings with the team and the main contractor
Review
- Review health and safety performance with your own workers and contractors
- If engaging contractors, review during the project and post-project review
Working along other businesses is a natural part of residential construction. Everyone on-site has a duty to open up the lines of communication and look out for each other.
Businesses (PCBUs) that work together will often share health and safety duties in relation to work done. Businesses have a legal duty to consult, cooperate with, and coordinate activities with all other businesses they share overlapping duties with.
What does this mean and how can you ensure that people are not harmed, and you are complying with your legal obligations? Here are some expectations:
- Work with designers to reduce risks
- Set clear health and safety expectations and incorporate these into your agreements with contractors
- Ensure contractors have appropriate health and safety procedures in place
- Prepare a Site Safety Plan for the job and share with all workers and contractors
- Establish health and safety reporting requirements with your contractor. A great tool for this is to use the HazardCo App to complete Risk Assessments, Incident Reports and more.
- Ensure site inductions take place. Coordinate and communicate site rules and procedures to everyone who accesses the work site, this can be done via the HazardCo App by scanning the QR code located on your Hazard Board.
- Set up clear requirements for information sharing for the duration of the project
- Ensure that there is effective communication between all parties (e.g. Toolbox Meetings through the HazardCo App)
- Monitor your workers and/or contractors you hire
The following key steps should be followed by Principal Contractor:
Scope
- Consider health and safety risks prior to selecting contractors.
- Discuss the project with potential contractors to make sure they are capable.
- Document the process and store in the HazardCo Hub.
Prequalify
- Ensure prospective contractors have effective health and safety procedures in place.
- Keep records of contractors’ prequalification.
- Get peace of mind your contractors are good to go, with an automated system to pre-qualify your contractors, check insurance, trade qualifications and more with HazardCo’s Pre-Qualification Tools. Find out more here, or get in touch with the team to find out if it’s right for you.
Select
- Select the contractors based on prequalification outcome and any other factors including availability, skills etc.
Appoint
- Create a Project in the HazardCo Hub, which creates a Site Specific Safety Plan, QR code and Hazard Board. Share the information with contractors.
- Ensure induction expectations are understood by all workers, contractors and visitors.
- Ensure all contractors have reviewed the information and agreement is reached and documented.
Monitor
- Regular communication regarding health and safety performance (e.g. toolbox meetings, site reviews, site inductions etc.)
- Investigate any incidents and follow up on any outstanding issues.
- Regular review during the assignment (e.g. Site Reviews)
Review
- Post contract review – It’s good practice to review the performance of your contractors at the end of the project. Look back at areas that were monitored during the project such as communication, incidents, Site Reviews, etc.
Working along other businesses is a natural part of residential construction. Everyone on-site has a duty to open up the lines of communication and look out for each other.
You can read more about contractor management and overlapping duties here or if you have any questions about working with other businesses on-site, give our expert Advisory Team a call on 1800 954 702.
What is Contractor Management?
“Contractor management” is a WHS / OHS term used by building companies. It’s referring to the process of checking if your contractors are competent and work safely.
As a building company, what do I need to do?
Your obligations as the principal contractor are pretty straightforward. First, you need to make sure contractors have the right skills and experience to do the job, and second, you need to make sure they are going to carry out the work safely. Once they are on board, you also need to monitor if the contractor is following good health and safety practices on-site.
Collecting evidence of this process is important so we recommend putting a system in place so nothing falls through the cracks.
What you should be asking your contractors for:
Pre-qualification company checks once a year:
- ABN number and company details
- Insurance (work cover / income protection / public liability)
- A health and safety policy and evidence they follow good processes
Pre-site induction of workers:
- White card
- Trade qualifications and experience
- High Risk Work License
On-site induction of workers:
- Have they read and agreed to the site specific safety plan?
- Have they been made aware of any hazards on-site?
- Are they bringing any hazards on-site?
On-site health and safety:
As a yardstick, good health and safety on-site would be your contractor completing at least two Toolbox Meetings and four Risk Assessments a month plus a SWMS any time high-risk construction work is carried out.
How to stay on top of all these checks:
Stay on top of these checks with an automated system.
Get peace of mind your contractors are good to go, with an automated system to pre-qualify your contractors, check insurance, trade qualifications and more. Because it’s automated, you won’t have to chase contractors for outstanding documents, and you’ll even get a notification if someone scans-in who hasn’t been approved.
Find out more about HazardCo’s Pre-Qualification Tools here, or get in touch with the team by giving us a call on 1800 954 702 or email info@hazardco.com
We’re pleased to announce our partnership with Procore, a digital large-scale construction management software solution.
This strategic partnership brings together two leading systems, as construction companies across Australia and New Zealand are increasingly adopting on-site technology to ease their administrative burden and work more efficiently.
We make health and safety simple, giving more than 10,000 companies the confidence they are keeping their team and their business safe, while reducing the time they spend on paperwork. Our system provides guided digital tools as well as incident support and health and safety advice when it is needed. We’re most well known for our simple and effective site induction and scan-in solution.
“We’re pleased to be able to integrate Procore with our unique site induction and scan-in solution, making it faster and easier than ever for Procore customers to know who is on-site, and when,” said Nick Halley, Head of Product at HazardCo. “Members receive a hazard board with a unique QR code for their site fence, and everyone uses the free app to scan into site, induct themselves and accept the safety plan, with H&S docs seamlessly flowing back into Procore.”
“Our goal is to make health and safety simple. This exciting partnership between HazardCo and Procore connects construction management and health and safety together, giving building companies an out-of-the box digital WHS system that seamlessly connects with their existing workflows,” said Iain Dixon, Chief Executive at HazardCo.
He concludes, “we regularly speak to builders that are passionate about building scalable and efficient processes for their business, but health and safety continues to be a very manual and paper-heavy activity for them. There are large gains to be made by digitizing health and safety, with HazardCo members telling us they have halved the time they spend on WHS admin using our simple system. This partnership will make it easier for building companies to streamline their processes and give them the confidence they are on top of their health and safety requirements.”
Health and safety issues arise from a worker raising concern about health and safety at the workplace and that concern remains unresolved after consultation with the worker/s and the PCBU/Employer, it then becomes a health and safety issue
For example, an issue could include a difference in opinion on whether something is a potential risk to health and safety or whether a particular control measure is suitable. .
There are issue resolution requirements in Health and Safety legislation across Australia which outline how a health and safety issue can be resolved, with the aim to agree on how to fix the problem as soon as possible to avoid further dispute or a similar future issue.
PCBUs/Employers are to agree on the issue resolution procedure with their workers. If this does not occur, the default procedure for issue resolution under the relevant State/ Territory WHS Regulations must then be followed.
Who is involved in resolving a work health and safety issue?
Multiple people will be involved in the issue resolution process to ensure adequate consultation and the best outcome occurs. This means it could be:
- the PCBU/Employer with whom the issue has been raised or their representative (e.g. Supervisor)
- any other PCBU (e.g. Contractors, trades) or their representatives who is involved in or potentially impacted by the issue
- where at least one worker in a work group is affected by the issue, their Health and Safety Representative (HSR) (if there is one)
- where at least one worker who is not in a work group is affected by the issue, the worker(s) or their representative.
How to involve representatives in the issue resolution process?
If you or your worker would like to involve representatives in the issue resolution process you are able to do so. A representative does not necessarily need to have health and safety expertise. This could include people such as a designer of a piece of equipment at the workplace, or a person with workplace consultation and negotiation skills. Depending on the nature of the H&S issue, advice or assistance from a range of experts may be required to reach an appropriate and informed resolution between the involved parties.
Things to remember:
- At any stage in the resolution of an issue, a party may nominate a person or organisation to represent or support them while resolving the issue (a ‘representative’).
- Where a party invites a representative to participate in the process, they should notify the other parties of their involvement in a timely manner, especially if their representative is authorised to act on their behalf.
What is an agreed Health and Safety Issue Resolution procedure?
It’s an agreed process or steps for resolving health and safety issues in the workplace.
You can establish an agreed procedure for a workplace. To do this, make sure the procedure:
- Outlines a process or steps for resolving issues
- Relates to health and safety issues only and is not a procedure for other purposes, such as a grievance or complaint procedure.
- Is agreed to, meaning that there has been genuine consultation and agreement between the PCBU/Employer and workers (including HSRS where in place)
- Is documented in writing
- Is communicated to all workers affected by those procedures.
- Include the requirements set out in your State/Territory Legislation.
What is a default Health and Safety Issue Resolution procedure?
The various State/ Territory Regulations set out the default procedure for issue resolution.
The default procedure provides for any party to the issue to commence the procedure by informing the other parties involved that there is an issue to be resolved and the details of the issue.
In attempting to resolve the issue, the default procedure requires the parties to have consider and review relevant matters, including:
- The potential consequence (severity) and likelihood of the risk to workers or other persons
- the number and location of workers and other persons affected by the issue
- the measures, both temporary and permanent, that must be implemented to resolve the issue
- who will be responsible for implementing the resolution measures.
What should happen after an issue has been resolved?
If the issue is resolved, details of the issue and the resolution must be set out in a written agreement, if any party to the issue requests this. If a written agreement is prepared:
- all parties to the issue must be satisfied that it accurately reflects the resolution
- the agreement must be provided to all people involved with the issue
Need Help?
If you’ve got a question about Health and Safety issue resolution or any other health and safety matter, the HazardCo Advisory Team is here to help. Give us a call on 1800 954 702.
Phew, what a year 2022 was. With continued labour shortages and skyrocketing supply increases it certainly wasn’t an easy year for residential builders in Australia.
The reality is that no one knows what 2023 has in store, so the best bet is to take stock of the things in your control. With a deep understanding of your business and some rock-solid processes, you can build a strong, resilient building company that is prepared for anything!
Check out this list of construction apps and technology that can help you stop scrambling around with paperwork and manual time-wasting tasks. Go digital and build a resilient business that gets ahead in 2023.
BuiltGrid
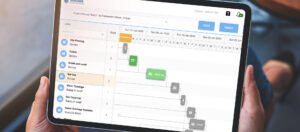
Supplier-connected project management
BuiltGrid is Australia’s supplier-connected project management system. The platform empowers builders to manage existing trades and find new trades & suppliers who want work. BuiltGrid will ensure your construction business completes your next project on time and under budget.
With no supply chain connectivity material and trade pressures are likely to continue into 2023, Toby Loft, co-founder at BuiltGrid says, “We’re dedicated to improving project visibility to reduce costly waste and rework; with real-time connection to your supplier’s builders save tens of thousands for every house built. Builders using BuiltGrid achieve a cost reduction of 8.75% in time, work and materials, giving them a significant boost in profits. With BuiltGrid, you can manage existing or find new trades & suppliers, compare quotes and automate your admin.”
Find out more about BuiltGrid.
Buildxact
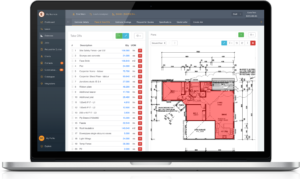
Construction management and estimating software
Buildxact is easy to use construction management and estimating software designed for small builders and contractors. It will help you to run your construction projects, from take off to invoice.
“With all of the current challenges in the market, building companies can really benefit from putting a system in place that helps them to deal with last minute schedule changes and price increases on the fly. Buildxact is really flexible. It will help you to stay on top of each job, giving you a clear picture of income and outgoings so you’ll know exactly where your job profit stands. Buildxact also now integrates directly with your supplier to get the latest prices to you to make your quoting quicker and more accurate”, says Julian Krishnan Nair from Buildxact.
“Our customers often tell us that using Buildxact cuts the time spend on take offs by 80%. You can upload the PDF and do your takeoff on-screen in minutes, you don’t need paper plans or scale rulers. Measure in a few clicks and price jobs in one step.”
Find out more about Buildxact.
HazardCo
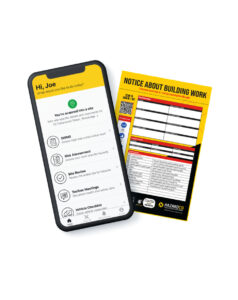
A simple health and safety system
HazardCo is a digital health and safety management system for home builders. It makes health and safety simple, giving you the confidence you’re keeping your crew and business safe, while cutting the time you spend on paperwork.
“When small builders want to move away from paperwork and digitize their processes, the first place they often start is health and safety. It’s an easy win that’s quick to implement and delivers instant results. You can create a site specific safety plan in minutes and have everyone scanning into your site in no time. As well as saving time, automating your contractor management processes helps to deal with labour shortages and provides flexibility,” says Luke Williams, from HazardCo.
HazardCo is trusted by 10,000 businesses across Australia and New Zealand
Find out more about HazardCo.
Getter
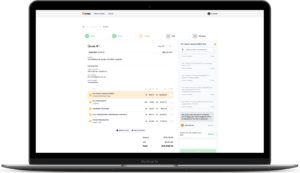
Supply procurement
Getter has created an on-demand procurement platform for all tools and materials, bridging the gap between wholesaler and construction site. Getter has an extensive supply chain that can tip the scales to your competitive advantage as project margins fall and programs tighten.
Sam Hatty from Getter explains, “Getter is the answer to one of the greatest productivity killers all builders and tradies face in their day-to-day – supply procurement. We were founded by a group of tradies so we’re well aware of the constraints that sourcing and procurement can put on a project, both economically and time-wise. What makes us different is our unique technology backed by an enthusiastic team and an extensive supply chain. We have a heavy focus on customer service and precision delivery by our own inhouse fleet.”
The platform consists of 2 sourcing options; ‘Shop and Deliver’ and the recently launched ‘Getter Quotes’.The Shop and Deliver service offers an online catalogue boasting over 100,000 products categorised into trade-specific genres with an intuitive product availability filter according to location. Getter Quotes simplifies a traditional material sourcing process from clunky emails, phone calls & over the phone prices to an easy to use, transparent, itemised quotation process. Giving customers access to a much wider range at incredibly competitive pricing.
Find out more about Getter.
Landchecker
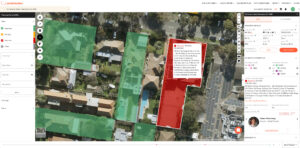
Instant property and land data, in one place
Landchecker brings over 300 sources of information into one place so you see the full story of any property.
Craig Heaven from Landchecker says, “When a potential client calls you up about a site and they’re wanting to know the possibilities, you can quickly put the address into Landchecker and view up to date property information about the site in one place. Landchecker is fast, accurate and easy to use so you will look like a pro to the potential client and ensure the build aligns to your company”
Information includes land size, planning zones, overlays, and previous planning permits for the property and surrounding area. Turn on high-resolution aerial imagery to get a good look at the site and to see what it looks like now and historically to see what’s developed around the property. Landchecker is currently available in Vic, NSW, Qld,WA, Tas and SA with more than 3000 builders regularly using the platform.
Find out more about Landchecker.
Xero
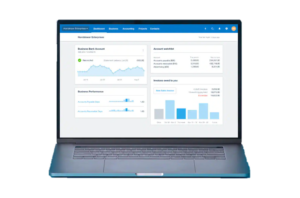
Accounting software
Xero is online accounting software for your business that connects you to your bank, accountant, bookkeeper, and other business apps. It’s made for small businesses, so you can automate admin and work from anywhere, any time.
The thing about construction accounting is that you have to do it regularly. If you fall behind in your accounts, things can quickly get out of hand. So it’s vital to build accounting into your workflow. Xero is cloud based and simple to use. Whether you are on site or in the office you can access Xero on your smartphone or tablet so you’ll never get behind.
Find out more about Xero.
PSI Global
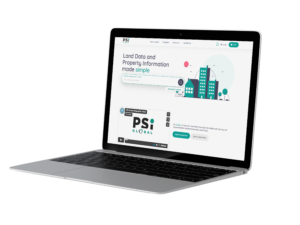
Property information
PSI Global specialises in property information for builders and trades.
“We know builders are busy managing their business, so we make it our mission to do the grunt work”, comments Samantha Whitmore, PSI Global.
“Our process is simple – we have great relationships with local government authorities, we gather all the information for you and we even do all the chasing up! We proactively keep you updated on how your job is tracking through our online portal and you can opt to receive your property information as we get it or at the very end in a neat package. We then provide you with one easy-to-manage invoice when your job is complete, no monthly subscriptions and no hidden fees.”
You can order Certificate Of Title, DP Plan (Title Plan), Instruments 88B, Sewer Drainage Diagram, Planning Certificate 10.7(2), Planning Certificate Section 10.7(5) and more.
Find out more about PSI Global.
There’s an easier way to kick off projects, and it’s with HazardCo. Cut the time you spend on health and safety admin, without cutting corners!
If you’re the principal contractor, you need to have a clear plan in place that everyone is aware of (including your workers and contractors).
Get started with all corners covered:
- Answer a couple of questions and a personalised site-specific safety plan will be automatically generated for you
- Set-up your new project in minutes, add your contractors and the site-specific safety plan can be automatically be sent to them
- Receive site signage for your site
- Get stuck into it
What does my team have to do?
Get tradies, contractors and anyone else stepping foot on-site to download the HazardCo app and you’re all set. Did we mention it’s free to download?
A quick scan of the onsite QR code with the app allows everyone to induct themselves as they turn up.
Start your project the right way. HazardCo will help you to nail your health and safety before you start the build and throughout the life of the project – giving you one less thing to worry about and helping you get your team and contractors home safe at the end of every day.
Our Advisory Team gets a heap of questions about near misses and if they should be recorded. Let’s look at what’s considered a near miss, when they should be recorded and how to go about it.
Near misses matter
Tradies know all too well how regularly they have a close call on-site. But is a “close call” the same as a near miss?
Put simply, yes. A near miss is a dangerous event that occurred without causing personal injury or on-site damage of any kind.
Examples could be anything from a worker tripping over stacked material, dropping a hammer off the scaffold onto the ground, or backing the truck and narrowly missing the boss’s ute. While these seem fairly innocent, they could have been more serious and it’s important that they are all reported. Evaluating what could have been done differently ensures on-site health and safety remains a priority, with near-miss prevention at the top of the list.
Why near misses are often brushed aside
Ignoring a near miss might not seem like a big deal, but it can create a culture on-site where safety isn’t taken seriously. We tend to find that when incidents aren’t reported, these are some of the common reasons why:
- Fear of standing out or blame – near misses may be swept under the rug to avoid blame.
- Leaders don’t set an example – the crew on site won’t report small risks and near misses if managers don’t set a good example by doing it themselves.
- Chalking it up to tradie culture – showcasing a ‘get over it and get on with it’ attitude is leading by poor example. Every near miss matters and the whole team can record them super fast with the HazardCo App.
Near miss reporting – it’s serious business
Look at near miss reporting as a second-chance educational tool. It’s not about blame or singling anyone out, it’s about discussing and emphasising a safer environment on-site. Combined with encouraging near miss reporting, it could mean the difference between change or injury.
Are there patterns in near misses occurring? Are there lots of reports of tools falling from height?
Investigate and ensure controls like the below are in place:
- Can the work be done on the ground?
- Only take the tools you need up at height
- Can work be done with no one below?
- Are toe / kickboards in place on scaffolding?
- Put in place a exclusion zone below the work above
Near misses should never be overlooked. With a swipe and a few taps of the HazardCo App, on-site incident reporting couldn’t be easier. Every tradie deserves to knock off injury-free after a hard day on the tools. Follow up on near misses, discuss the possibilities and take action with HazardCo.
We’ve partnered with the Master Builders Association of Western Australia (MBA WA) to provide their members access to our leading health and safety system.
With the introduction of the new work health and safety regulations in WA that came into effect on 31 March 2022, we are pleased to be able to support home builders to understand these new WHS laws and put in place a simple and effective system that will help them to feel confident they are protecting both their team and their business.
Executive Director of Master Builders WA, John Gelavis says we are really excited about this partnership, as it will help provide Master Builders members with the opportunity to access reliable safety tools and advice, which will build a better and safer industry for all.
“The WA building and construction industry relies on safety advice, and with the recently changed Work Health and Safety Laws, this partnership with HazardCo will be an extremely useful tool and service for our members”, says Mr Gelavis.
Alongside discounted access to the HazardCo system and advisory services, Master Builders WA members are also entitled to a free WHS check-up to take stock of what should be done on-site and off-site to provide a safer site and work environment. We will help you evaluate your current systems in light of the new WHS laws in WA and will provide guidance on what’s being done well and areas of improvement.
Chief Executive and Director of HazardCo, Iain Dixon says HazardCo is proud to partner with Master Builders WA.
“Master Builders WA is one of the most recognised and respected brands in the industry. This partnership reflects our desire to collaborate with companies who share the common goal of helping builders to keep their teams and their businesses safe. We look forward to meeting more builders throughout WA and introducing them to a better, simpler way to manage their health and safety”, says Mr Dixon.
To find out more about the partnership and get your H&S sorted click here.
Looking for something in particular?
Working with heavy machinery and managing traffic on-site can be risky. But with the right checks and planning, we can keep everyone safe.
Daily machinery checks
Before starting work each da...
Demolition machinery
Working with heavy machinery can be dangerous. Incorrect use or untrained operators can lead to serious injuries or worse.
Training and supervision
Machinery sho...
Digging into the ground might seem straightforward, but excavation work is actually one of the most dangerous parts of construction. That’s why it’s important to plan ahead and put the right s...
When you're able to get back on site after a flood or storm, here are the hazards, risks and control measures you should consider to help reduce the risk of injury and illness to yourself, you...
Dust is a common hazard in the construction industry, especially during demolition or refurbishment. When buildings are demolished they can release materials that create hazardous dust (airbor...
The holiday season is over and now it’s time to get back into the swing of things. Coming back to work and reopening your site is just as important as shutting it down. The New Year is the per...
The holiday season is almost upon us, and we’re all eager to have a bit of a rest, recharge, and spend quality time with our families. As we wind up 2024, it is a demanding time for constructi...
When you have an incident on-site, whether it’s a near miss, an injury, or a work-related illness, it’s important to document an incident report.
Incident reports don’t need to be time-cons...
Anything with wheels and an engine should be at the forefront of your mind on site.
From delivery trucks to excavators, if it moves, and it’s got some weight… then that means power! it’s g...
Electricity is essential on construction sites, but if the risks are not managed properly, it can pose serious dangers to people and property. Proper controls must be in place wherever electri...
Health and safety is a core part of any business but incidents and injuries on the job can still happen. According to SafeWork Australia, in the construction industry alone there were 15,877 s...
The HazardCo App has a new Plant/Machinery Pre-Start tool! It’s a quick and easy way to do pre-start checks on various plant and machinery such as scissor lists, boom lifts and excavators. Jus...