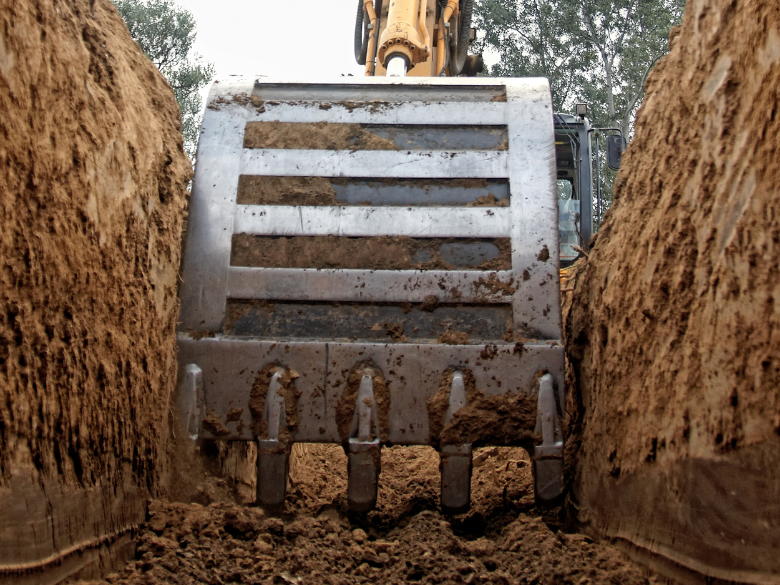
It’s important for young people starting out in construction to understand how to stay safe at work. Young workers lack experience and might not know about all the hazards yet, which could put them in danger of getting hurt. Sometimes young people might feel like they have to impress others, or they might think they’re better at the job than they actually are, they may also forget about safety rules or be afraid to speak up if something seems unsafe. Because of this young workers have additional needs and should be supervised when working on-site.
Positive safety culture onsite comes from the top down, supervisors should be actively modeling and training young workers about safety rules, make sure they have the right gear, and encourage them to speak up if they see any problems.
There are some jobs that young workers shouldn’t do because they might not have enough experience or strength yet. Supervisors need to make sure young workers can handle their tasks and keep an eye on them until they are sure they are able to do the work safely. Young workers also need to think about their own safety, listen to instructions and follow safety rules.
When everyone works together to stay safe, it helps make sure everyone goes home safely at the end of the day.
Now, let’s delve deeper into some specific measures that can be taken to ensure the safety and well-being of young workers in the construction industry:
Employing young workers in the construction industry has benefits for the young person, the company and for the industry as a whole as the next generation of builders learn and grow into future roles. By prioritising safety and investing in the well-being of young workers, employers can create a culture of safety that benefits everyone involved. Together, we can build a safer and more secure future for the next generation of construction workers.
If you have any questions, get in touch with the HazardCo team today
Tools, vehicles, and heavy equipment all create vibrations that can affect your body. This is a normal part of any tradie’s day, whether you’re picking up power tools or jumping in the ute. It’s so common that many don’t realise the potential harm these vibrations can cause. However, it’s something you should start thinking about and being aware of.
How are workers harmed?
Vibrations are a natural part of working on any construction site but they do create a risk to you and your workers. Repeatedly using vibrating hand and power tools, or being around vibrating vehicles and machines can lead to serious and lasting harm to your blood vessels, nerves, and joints. Many of the most commonly used items give off some form of vibration. Here are the most common ways tradies are exposed to vibrations:
While these are the most common forms of exposure, the below should also be considered as they increase the risk of overexposure to vibrations:
Early warning signs
We understand that for many tradies, working with vibrations is a natural and unavoidable part of the job. With that in mind, there are a few warning signs and symptoms of overexposure to keep an eye out for:
If you are continually exposed to vibrations especially in your hands and arms you can develop hand-arm vibration syndrome (HAVS) or carpal tunnel syndrome (CTS).
What you can do to manage risk
It is up to everyone on-site to look out for each other. Consultation with your team should take place to make sure an environment can be created where excessive exposure to vibrations are eliminated or minimised.
Below are simple yet effective ways to either eliminate or minimise the effects.
Above all else, be aware that vibrations can be extremely harmful, especially when you’re exposed for lengthy periods of time.
Your best tool for minimising the effects of vibrations is to start a conversation with your boss, or your team, and put steps in place to look out for each other and your equipment.
If you have any questions please reach out the the HazardCo team
Updated on 26 August 2024
On 1st July 2024 an engineered stone ban will take effect in all states and territories. The ban prohibits the use, supply, manufacture, processing or installation of engineered stone benchtops, slabs or panels.
Further information is yet to come on:
Until now, the focus has been on engineered stone, however crystalline silica can be found in many other building materials. It has just been announced from 1st September 2024 changes to the crystalline silica regulations will be made to further protect workers.
This includes working out if the processing of the crystalline silica substance is high risk and putting in place additional control measures if it is. Read our summary of the Crystalline Silica rules.
A new Code of Practice will be released in all states to reflect these changes. During its development, Safe Work Australia will provide guidance to help businesses and workers understand and comply with the new regulations.
Engineered stone is an artificial product that:
If you need to repair, remove, dispose of or make any minor modifications after 1st July 2024, you will need to notify your state regulator first. Notification forms will be available from your state regulator along with any other specific information such as timeframes and re-notification requirements.
VIC – A licence is no longer needed to work with engineered stone from 1st July 2024 and no notification will be required to work with already installed stone.
NSW, SA, WA, TAS, QLD – Notification forms will be available from your state regulator before 1st July 2024 and you will need to submit the form before starting any work.
NT – Written notification will be required every 12 months. The form will be ready before 1st July 2024.
ACT – Notification is required from 1st November 2024 and you will only need to notify once.
Remember, before starting any of the work you must have control measures in place to minimise the dust and you must wear respiratory protection.
Creating a SWMS in the HazardCo App can help you with selecting the right controls for the task such as using water suppression or on-tool dust extraction, and a minimum P2 dust mask or respirator.
There are plenty of silica-free options out there to suit every budget such as timber, stainless steel, and laminate options have come a long way, such as these Contact Sheet options from Laminex.
https://www.safeworkaustralia.gov.au/esban
https://www.safeworkaustralia.gov.au/esban/faq
https://www.worksafe.vic.gov.au/frequently-asked-questions-engineered-stone-ban
Information correct as of: 24th June 2024
Respiratory Protective Equipment (RPE) is essential gear for protecting you from inhaling hazardous substances. In this blog, we’ll explore the important role of RPE, whether you are dealing with airborne contaminants like asbestos, fumes, dust, or working in a confined space, RPE is an essential personal protective equipment (PPE) that makes sure you can breathe safely. Join us as we deep dive into the different types of RPE, their applications, and how they can protect you from potential health risks.
Before you even get started with RPE, make sure you have other practical control measures in place first; such as local exhaust ventilation or direct dust-extracted tools with a vacuum catchment to get rid of the majority of contaminants in the air. You should also be keeping an eye on your team’s health and workplace conditions to ensure that, over time, they aren’t being made sick or getting injured by their work.
Remember, there is no such thing as a healthy dust, even if you are outside!
We’ve gone ahead and put together a quick guide of factors to consider when providing your workers with RPE.
Disposable respirators are good for short term or one-off use and when you have existing controls in place to give you extra protection. When using a disposable respirator you need to make sure a seal has been created to protect you from harmful particles such as dust, fumes and fibres.
Respirators use replaceable filters to remove contaminants to clean the air for the wearer. They come in half-face and full-face versions. The cartridge filters are specific to certain types of contaminants, ask your manufacturer exactly which cartridge you should be using for the respirator you have and the contaminants you will be facing.
Remember if you have stubble or any facial hair you may not be getting the seal and the protection you think you are! So if you love your bread as much as your lungs read on to find out what you can do
Powered air purifying respirators (PAPRs) consist of headgear and fan assembly that take contaminated air, filters it, and then delivers the clean air to the user. These are also known as positive pressure systems. These not only keep you nice and cool, but offer the highest protection there is for people who have facial hair. Something to note with these is that the visors and headset can be impact rated if you need it, and don’t fog up because of the airflow.
Supplied air respirators provide a supply of clean air to the wearer from a source such as an air compressor or cylinder. It’s important to note that the air supply needs to be checked regularly to make sure that it is safe to use – just think about what you see coming out of your air compressor when you release the valve under the air tank! The user must also be trained in how to use the system.
It’s important for your workers to be trained in using and maintaining their RPE. They should visually check their RPE for signs of damage before each use to identify any issues, including whether it needs to be cleaned or decontaminated.
Make sure your team keep their RPE on while working in the hazardous area. Removing it for even a short period of time is a risk to their health.
Did you know that they come in different sizes? One size does not fit all!
If your workers are using RPE then make sure they are fit tested, this way you will know who needs what size, otherwise it may not work and give the protection your workers need.
The manufacturer of the RPE can tell you who can do this testing.
There are two checks which you need to do each time you use and RPE:
1 – check for damage visually to the sealing surfaces and straps
2 – check the valves are functioning correctly like WorkSafe images below
Image Source: Worksafe New Zealand
Keep in mind that if your worker’s safety glasses fog up while they are wearing a half-face respirator, this is a sign that there is a leak at the top of the respirator which means they are not getting full protection.
When your workers are wearing respiratory protective equipment at work, they must be clean shaven to ensure it is forming a seal and protecting them from breathing in hazardous materials. Even a small amount of stubble can prevent RPE from sealing correctly which means your workers will still be inhaling harmful materials which may cause health concerns. A clean shave goes hand in hand with the correct RPE for the job.
It’s your legal responsibility to monitor your workers’ health. Make sure that you are completing regular Site Reviews on the HazardCo App, as this will help you to identify potential hazards and put effective plans in place. Your HazardCo Advisory Team is available throughout the day to guide you through this – call 1800 954 702 to talk it over.
Image source WorkSafe
Lithium batteries are common in everyday life and on the worksite, their lightweight, long life, interchangeability and quick charge benefits mean that they are now used in everything from laptops to power tools to EVs. But did you know that they pose a significant risk and need to be a part of your health and safety plan?
What’s the risk?
Lithium batteries of all sizes have the potential to overheat and catch fire. The fire is hotter, harder to put out and the smoke from these fires is incredibly toxic. Lithium batteries generally overheat if they get wet, damaged or are used with incorrect charging equipment.
Damaged batteries can explode at any time giving off flames that burn anywhere between 500 and 1000 degrees celsius. These fires are very difficult to extinguish as both water and CO2 will only suppress the fire, not extinguish it. Even if the fire has been suppressed it can still ignite again if the battery still contains energy to burn. Because of this, lithium batteries need to be properly cared for according to the manufacturer’s instructions to minimise the risk, aside from that, you need a plan in place in case of a fire.
Hot tip: The bigger the battery the bigger the risk
Ways to minimise the risk:
Safe lithium battery disposal
Never dispose of Lithium batteries in general rubbish as it can result in a fire in your bin or on the way to a transfer station, creating a risk to those transporting them. The manufacturer should be able to advise safe disposal or check out your local battery recycling centre.
Lithium batteries are going to continue playing a crucial role in our workplaces and lifestyles, so it’s necessary to recognize the potential hazards associated with them. By having awareness of these risks and good practices, we can work together to reduce the potential dangers, resulting in safer working environments where Lithium batteries are used.
If you have any questions, give the Hazardco team a call today!
Making sure your scaffolding is safe and ready for action is key. Here are the times you have to give it a good once over:
All scaffolds must be checked by a competent person before handover and scaffolds taller than 4m must be erected and inspected by someone who holds a high risk work license. Handover checks can involve completing a handover certificate and should be kept at the workplace until the scaffold is taken down. Scaffold tags are a great way to identify whether a scaffold is safe to use or not, and are used after it has been checked. Tags should be clearly displayed where workers can see as they approach the scaffold. The tags should be at every access point to the scaffold or at least at eye level on the ladders.The tag should include the following:
If there’s no tag, it might not be safe to use! Get in touch with your scaffold installer to sort it out and get it tagged.
Every 30 days a licensed scaffolder (if over 4m) or competent person (under 4m) should be checking the scaffolding to make sure it is safe. If the inspector has found any damages or non-compliant areas of the scaffold, then access needs to be stopped and the tag updated stating the scaffold is not compliant and should not be used.
A thorough inspection of your scaffolding should also be conducted after any tweaks, fixes, or wild weather. And don’t forget to keep records of all these inspections.
If you have any questions get in touch with the team at HazardCo or have a look at our other working at heights blog here
Hazardous substances are chemicals or substances which can be toxic, corrosive and can cause harm. So it makes sense that we document what’s on-site and how much we have.
If you have hazardous substances on-site, there are legal requirements you need to follow to ensure they are stored, used, and disposed of correctly to reduce the risk to anyone that uses or comes into contact with them.
There are a number of chemical specific hazards that could potentially be present on a building site but these are the most likely ones that you will come across:
These are some of the hazards that can occur from hazardous substances
Remember to check the SDS (Safety Data Sheet) for your specific chemical when addressing the hazards it might present.
To capture what hazardous substances you are using you must by law have a hazardous substance register along with the relevant safety data sheet (SDS).
This is a list of all your hazardous substances (including hazardous waste) that is used, handled, or stored at any of your sites or workplaces. Having a register will ensure you know the substances you have on-site, the requirements you need-to-know, and what to do in case of an emergency.
Keeping your register in a central location on your site means that in case of an emergency, it can be accessed quickly by anyone who needs it. There are some key bits of information that need to be included on your hazardous substance registers. Not only do you need the information below, but you must also make sure that the register is up to date and available on-site.
Because the register represents the maximum amount of the substance held, it means it’s not going to be a daily task to keep it up-to-date. But if the maximum quantity changes, the register needs to reflect this. We recommend that you review your register each time you make a change to ensure it’s up to date and accurate.
Creating your hazardous substance register is made much simpler with our Hazardous Substances Register, HazardCo members can access this via the HazardCo Hub in the templates section.
The purpose of a safety data sheet (SDS) is to provide key information about hazardous substances to the people who handle, use or store them or who could be exposed to them.
Remember it is the business owner’s responsibility to have an up to date SDS for each hazardous substance and that their workers have access to it. You can ask your supplier for a copy of the SDS when you place an order or on the product website. The SDS should be less than 5 years old.
If you need a hand getting started or would like more information, get in touch with the friendly HazardCo team today – we’re always happy to help.
When it comes to construction sites, ensuring the safety and wellbeing of everyone on-site is the top priority. It’s more than just wearing hard hats and high-vis vests. It involves careful planning and preparation of the specific needs, hazards and risks of each project. That’s where Site-Specific Safety Plans (SSSPs) come into play.
A SSSP sets out the arrangements on how certain health and safety matters are managed on-site. A SSSP is designed to keep everyone informed on site specific details. It includes:
All construction projects need a SSSP. A construction project is when the cost of your job reaches a certain value and it is the Principal Contractor’s responsibility to have a SSSP in place before the project begins.
Setting up health and safety with HazardCo Projects is quick and simple. All you need to do is log in to the HazardCo Hub and “create a Project”. You receive the completed SSSP straight away while the physical scan-in board will be sent out for you to display on-site.
Not only does HazardCo’s Project save you time at the start of your project, it saves time for everyone on the site. Once the project starts, everyone entering the site inducts themselves on-site using the QR code on the site scan-in board, and the QR scanner in the free HazardCo App. That’s right, everyone inducts themselves using their smartphone, no lengthy induction meetings or paperwork required, and you get a record of every completed induction too.
Make sure you request a SWMS from each of your contractors so you can check they have included all the relevant hazards and controls in your SSSP. This will help ensure you and others on site are well informed of all the hazards from start to end of the project.
Share the SSSP with the team. Anyone scanning into the site using your QR code and the HazardCo App will have immediate access. Every worker who sets foot on-site needs to know and understand the SSSP. This can be done during the site induction, where the workers learn about the project, potential hazards, and safety protocols, which they can do using the App. If you need more information on working with contractors you can check out this blog.
While there’s no one-size-fits-all approach to creating a SSSP, using digital tools like HazardCo can offer great time saving and streamlining benefits. Among many other benefits of using HazardCo, using it for SSSP means that you have:
Going digital with the HazardCo App means information flows more efficiently and this allows your teams to better collaborate with one another.
So, whether you’re building a multi-dwelling residential, a new build or doing a big reno, remember: safety first, always. And with a solid SSSP in place, you’re one step closer to a successful and safe construction project.
For health and safety sorted in a flash, right from the very start of your new build, look no further than HazardCo Projects. It’s the smart way to maintain a safe site and have more time to focus on the job at hand.
If you would like to discuss your upcoming project please give our team a call on 1800 954 702.
Long gone are the days of “she’ll be right mate”. Staying on top of your health and safety makes your site safer – simple as that. We all want our team members to get home safely at the end of the day, and now there are smart systems to help you to get the job done there and then, without fuss or delay.
HazardCo was created with this in mind – because it’s all online, you make updates in real-time from anywhere on-site, all from the palm of your hand. The HazardCo App allows you to complete a SWMS, site review, toolbox meeting or incident report, all on your smartphone – so it’s done straight away. No delays, no forgetting details, you can even take photos so you capture everything you need to. Taking a smart approach to your workplace health and safety and staying on top of updates, can be a real weight off the shoulders.
The HazardCo App is free for everyone to complete their initial site induction, and to scan in/out of site every day. Because they’re on the App whenever they walk on to site, health and safety is kept top of mind – a key part of creating a safer site. An added bonus, If one of your crew or subbies were to sign up and become a HazardCo member, you can also get a copy of all of their on-site safety activity, giving you the complete picture. When you have a safer site, everyone can keep working at full speed, and your project isn’t slowed down by injuries hampering your team or the wider crew. It’s a complete win-win.
Do the right thing by your people and prioritise health and safety on-site. HazardCo is all about making health and safety quick and easy, without cutting any corners – helping you to protect your people and your business for the longer term.
The reality is unsafe work at heights can have devastating consequences. Falls from heights are one of the leading causes of fatalities and injuries in the construction industry within Australia. Preventing falls should be actively managed so that people working at heights are kept safe.
Identifying a task that could lead to a fall is the first step to keeping people safe. Before commencing, put in place the highest level of protection possible to prevent falls.
Consider how long the job will take: The duration of the job will impact how you select the level of protection. If the job is ongoing, the structures chosen need to remain stable throughout the job. You may need to reassess things like ladders and scaffolds throughout the job.
The hierarchy of controls outlines the various controls in order from the highest level of protection to the lowest level of protection. Select the safest, most appropriate control measure from the below hierarchy to prevent injuries or fatalities from falls from heights on your site.
Work on the ground or solid construction
If you can avoid working at height it should be your first option and is always the safest option. Some examples of eliminating the fall risk include using long-handled tools, relocating the task to the ground, and using extension poles for tools.
Use fall-prevention measures
If working from a height is necessary, you need to manage the risk of a fall. Fall prevention measures could be something like an elevated work platform, scaffolding, or guard railing.
Use a work positioning system
Check if a work positioning system like a travel restraint system can be used. A travel restraint system enables a person to work in a way that prevents the person from falling e.g. fixed-length lanyards and static line systems
Use a fall arrest system
Check if a fall arrest system like an industrial safety net, a catch platform or safety harness can be used. This system doesn’t prevent the fall but arrests the fall so you don’t come into contact with the ground e.g. shock absorber on lanyard or anchor point.
Ladder use
It may be appropriate to use a ladder. Ladders do not provide fall protection and as such should only be looked at as a last option when selecting the level of protection. Ladders should only be used for short duration works such as changing a light bulb or paint touch-ups.
Below is a great image from WorkSafe Victoria which has summarised the hierarchy of control measures for the prevention of falls. Click on the image below to view
Important: Where high-risk construction work includes a risk of a person falling more than 2 metres (3 metres in South Australia), a safe work method statement (SWMS) must be developed prior to work commencing.
Seek professional assistance
Working at height can often be high risk and there are experts who make it their job to complete this work safely. It is often safer and more cost-effective to use height specialists even for shorter jobs.
Make sure everyone knows what to do
Give your workers all the info they need to stay safe.. Conduct toolbox talks and remind them the importance of procedures and completing a SWMS (when required). Encourage them to watch out for each other and speak up if something doesn’t seem right.
Consistency is key
It’s important you and your team are actively involved in ensuring any heights related work is carried out in the safest way possible.
Resources
There are various WorkSafe / SafeWork websites, resources, and support tools on managing the risk of falls. Some examples include:
If you’ve got a question about working at height or any other health and safety matter, the HazardCo Advisory Team is here to help. Give them a call on 1800 954 702.