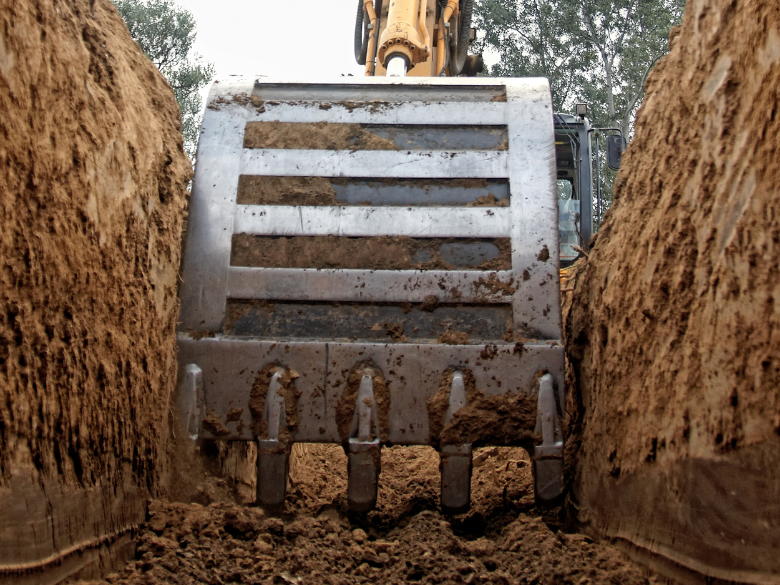
Running a safe site isn’t just about wearing hard hats and harnesses; it’s about effective communication and staying aware of what’s going on on-site. One of the most powerful tools is the humble toolbox meeting. These gatherings are the backbone of ensuring everyone on site is up to speed with hazards and safe working practices.
Download the Simple Guide to toolbox meetings to get tonnes of ideas for toolbox meeting topics.
Toolbox meetings are a forum to highlight safety expectations and encourage participation from everyone on site. They don’t need to be lengthy; a quick stand-up meeting will do – maybe even with a side of chocky biscuits to sweeten the deal! We recommend holding these meetings weekly, or at least twice a month, to keep safety at the front of everyone’s minds.
Some building companies take it a step further by incorporating toolbox meetings into their daily routine. Starting each day with a brief safety discussion helps to make safety a daily habit, rather than an afterthought.
The success of a toolbox meeting hinges on a few key factors:
Here are some prompts to kickstart discussions in your toolbox meetings:
Toolbox meetings help with communication, collaboration, and continual improvement. Remember, safety is a team effort, and toolbox meetings are where that effort begins.
The HazardCo App includes all the on-site safety reports you need, such as a handy tool to record toolbox meetings.
We all know subcontractors need to complete their SWMS before starting any high-risk construction work but did you know that as the principal contractor, you also need to ensure that a SWMS has been prepared before their work starts?
With HazardCo, it’s easy to stay on top of health and safety activity from your subbies.
Project Plus unlocks the HazardCo app for all of your subbies and it automatically shares the required reports with you, taking the hard yakka out of health & safety for everyone.
With HazardCo, your subbies can easily complete and share their SWMS and other on-site health and safety activity with you. The SWMS form guides your subbies through a step by step creation process. It gives you both confidence that potential hazards have been thought through and controls put in place to avoid harm.
With every report digitally stored on the Hub, you don’t need to chase paperwork or file it away… all your site’s health and safety documents are kept in the one place, which you can access from anywhere, at any time.
When all of your subbies are using HazardCo your on-site management becomes easier, you’re not bogged down with paperwork and all SWMS are in the same format making it faster to review than having to wrap your head around different templates.
SWMS are an essential part of managing health and safety on your site. HazardCo’s clever app makes it even easier for your subbies to create their SWMS and share it with you quickly – keeping your site safe and saving you time every day.
For help getting your subbies signed up, call the HazardCo team today on 1800 954 702.
It’s never good to find out the hard way that there’s a gas, power, water or communications line buried right where you need to put something on your site. When planning for excavation works, it is important to implement safe excavation practices to minimise the risk of injury and hitting critical services.
Digging blind can result in construction delays, increased costs and serious incidents.
Excavation work is referred to as any work involving the removal of soil or rock from a site to form an open face, hole or cavity, using tools, machinery or explosives. This includes open excavations, potholing, pit excavations, trenches, retaining walls and shafts and tunnels.
Employers have a legal duty of care to take reasonable actions to protect both the people and the services which may be affected by their work. Getting and using the appropriate information on the services is an important part of ensuring safe excavation on your site. There is a large range of options this can cover, so we will cover the basics in this article. If you have more complex excavations and want advice then get in contact with us.
Remember any ground disturbance regardless of depth can damage infrastructure networks like gas, water, electricity so you need to get the right information to keep you & the underground services safe.
First, you need to get information on what the assets in the area may be. You can get this information from Before You Dig Australia. This online system is the easiest way to request known plans from the asset owners. It is important to know that not all Asset Owners are members of Before You Dig Australia, so it cannot show you everything that is in the area of your excavation. You may need to contact any other asset owners directly to get hold of plans, drawings and information regarding their assets known positions prior to starting your work.
Wait to receive all information on the assets before commencing work, and only refer to plans that are current.
Once you have information on the assets, make sure the plans are with the workers on-site and that they have appropriate health and safety information and instruction. This information must also be made available to the principal contractor and other subcontractors, and be easily available for inspection for the duration of the work. If you have a notifiable incident the information must be kept for at least 2 years. You should also isolate work around the underground assets from the public.
Pay attention to the clues around your site such as marker posts, inspection points and metres. Never assume pipes and cables run underground in a straight line or are at their correctly specified depth, and always assume all lines are live, even if they look as though they are abandoned or decommissioned.
Remember all digging activities can damage underground infrastructure. You should conduct a risk assessment for the task so that you can identify the hazards to focus on, and put in place suitable controls. Workers involved in the excavation need to be trained and competent to do their part of the work e.g the Excavator operator is appropriately licensed.
To minimise the risk of damage and potential loss of life, it’s best practice to follow the 5 P’s for safe excavation:
Plan – Plan ahead by lodging your Before You Dig Australia enquiry at least two business days before your project begins, and make sure you have the correct information required to not just carry out the work but how to respond to any possible emergencies.
Prepare – Prepare by reviewing all available plans from the asset owners and ensure you conduct a visual inspection of the site for any items such as put lids, marker posts, external vents and any other visual clue for service location prior to commencing works. If you need further verification you could have Ground Penetrating Radar (GPR) carried out to show exactly where buried things are.
Pothole – To confirm the exact location of the underground infrastructure(s), pothole if permitted using the asset owner’s stated method as specified on the asset owner’s plan and information pack. Work slowly on this as you’re actually trying to “hit” it but without damaging it.
Protect – If potholing has occurred, protect the infrastructure by using various methods; such as communicating to all working on site, erecting barriers and marking the location of the exposed infrastructure.
Proceed – You should only proceed with your excavation work after you have planned, potholed (unless prohibited) and have your necessary protective measures in place.
Remember to stay vigilant and watch for changes in the ground/soil as you dig.
If you’ve got a question about safe excavation or any other health and safety matter, our HazardCo Advisory Team is here to help. Give us a call on 1800 954 702.
Before You Dig Australia has resources available for your state or territory and best practice guidelines. Read our blog on Managing the health and safety risks associated with excavation work.
Get your team involved in health and safety, and watch your workplace become a safer, happier place for everyone.
Under health and safety legislation, businesses have a duty to engage with workers and enable them to participate in improving health and safety. The business must:
Remember that your subbies are also considered your workers when they are working for you.
Together with your workers, you can determine the best way to meet these requirements. What is reasonable and practicable will depend on your workers’ views and needs, the size of your business, and the nature of its risks.
Businesses must:
You will need to engage and consult with workers who are directly affected by a matter relating to health and safety. This includes when:
It’s important to have meaningful and effective health and safety talks. It’s good for people and for business. This doesn’t mean hour-long talks or lots of documentation, it’s simply about approaching H&S with the right attitude and aiming to get everyone involved.
HazardCo makes it even simpler to do this with our ‘Toolbox Meeting’ feature on our HazardCo App – handy for making sure everyone on-site is keeping on top of what’s going on.
If you need a hand getting started or would like more information, get in touch with the friendly HazardCo team today.
Any work undertaken near live overhead electric lines carries the risk of electric shock. Touching a live overhead line with any part of the body, tools or any other equipment can cause serious injury and even fatality.
Make sure that you and your team are aware of the following steps that can be taken to manage the risk of an electric shock.
You must prepare a SWMS before work starts and make sure it includes all the potential hazards and expected controls. Collaborate with your workers in developing the SWMS, ensuring they understand how the task is to be performed.
The safest option to eliminate the risk of electric shock is to temporarily disconnect a property’s electricity supply from the electricity distribution lines so that the overhead line to the property is no longer live.
Find out who needs to know that the electricity supply will be temporarily disconnected. Such as:
Anyone who could be affected by the disconnection of the electricity supply should be told:
If work needs to take place near an overhead electric line then the worker’s body, their tools, and their equipment must be kept a safe distance away from the overhead line, or else the electrical supply must be disconnected by the approved electrical supplier. This is known as the safe approach distance, or SAD.
More information on Safe Approach Distances can be found on your state Regulator’s website or contacting the energy supplier.
Keeping you and your team safe at work is a priority, so make sure you are aware of the requirements of working near power lines. The HazardCo App Site Review resource has a list of electrical controls that should be in place to mitigate the risk of electrical hazards. If in doubt, you can give our team of Health and Safety Advisors a call on 1800 954 702.
Worksites tend to be filled with constant noise from tools and machinery.
While noise often means things are getting done, there is a downside to it. Hazardous noise can affect a worker’s physical and mental wellbeing including hearing loss, stress, and lower productivity. So to help you protect your hearing, here are a few helpful tips to keep your ears in tip-top-shape.
Understanding what makes noise on-site and how it impacts people and different areas on site is critical. Ask yourself and your workers:
Once you understand the answers to the above, you can start putting actions into place to control noise on-site.
Be sure to monitor and review the controls throughout the project, as different stages will create varying levels of noise.
The easiest way to decrease the effect of excessive noise on your site is to eliminate the source of noise completely. But, chances are this isn’t possible on a busy site.
The next best thing is to reduce noise.
A couple of easy ways to do this include:
Isolation involves creating a dedicated space for ‘noisy work’. This could be an enclosed room or area of site where all noisy work and machinery is used or placing workers in an enclosed cabin when operating mobile plant. This helps to block the path of noise and reduce the levels that reach your team.
Having a good understanding of how machinery and tools operate can help modify processes to reduce noise at the source. Engineering controls can include choosing attachments or parts that are noise reducing, or changing the way machinery and tools are used.
With noise comes vibrations. These vibrations can be just as harmful as the noise itself.
Here are a few strategies to help decrease vibrations when using machines or power tools:
It’s not possible to escape noise on-site, however we can put steps in place to help reduce the effect that noise has on us while we’re working.
Safe Work Method Statements (SWMS) are an important tool to use within the Construction Industry for High Risk Construction Work (HRCW). We’ve listed the common myths we hear across the industry to help you get a better understanding of what really matters when it comes to using a SWMS, and how you can make sure your SWMS is going to help keep you and your workers safe.
Myth – You need to include all the relevant Health and Safety Legislation, Standards and Codes of Practice/Compliance Codes on the SWMS
Fact – It isn’t a legal requirement to include all the relevant Health and Safety Legislation, Standards and Codes of Practice/Compliance Codes on the SWMS. Some companies, particularly larger ones, might ask their contractors to include this information. You might want to consider using a SWMS template.
Myth – A SWMS has to be on paper
Fact – The SWMS should be kept at the workplace where the work is being carried out. It can be in electronic format (such as a SWMS App) or in a paper format as long as it is readily available to workers involved in the work, and for the entire time they are doing the work.
Myth – You need to include a Risk Matrix and score the hazards and controls on the SWMS
Fact – It isn’t a legal requirement to include a Risk Matrix or score the hazards and controls on the SWMS, however some companies (particularly big ones) might ask their contractors to do this.
Myth – A SWMS doesn’t need to be kept after the HRCW has finished
Fact – In most cases, a SWMS doesn’t need to be kept after the HRCW has finished, however if you have a notifiable incident it’s likely you will need to keep a copy of the SWMS for two years after the incident date. Notifiable incidents are incidents where there is a serious injury or illness, or a dangerous incident and there are certain criteria which can help to identify these types of incidents. If you have a notifiable incident we recommend you check with your Regulator (e.g. WorkSafe, Safe Work) about your requirements or HazardCo members can reach out to our Health and Safety Advisory team for incident support and advice.
Myth – Once a SWMS is developed, you don’t need to review or change it
Fact – Not true! If the control measures don’t adequately control the risk, it needs to be reviewed and changed. This might happen when:
At any stage, if work is not being carried out in line with the SWMS make sure work stops immediately (or as soon as safe to do so) and only resumes after the SWMS has been reviewed.
Remember, if you’re using a SWMS template, it needs to be specific to the site and the HRCW being conducted. Find out if your SWMS templates are up to scratch.
Myth – A SWMS can only include content relevant to the HRCW
Fact – Only hazards and risks that are directly related to HRCW activities need be included in a SWMS. You can add non HRCW hazards and risks if it makes sense, but don’t overdo it. We suggest removing anything unrelated to the high risk construction work to keep it simple.
Myth – A SWMS is required for all high-risk work
Fact – A SWMS is only required for the following High Risk Construction Work (HRCW) :
You must complete a SWMS before undertaking any high-risk construction work, so we’ve made it as simple as possible. The HazardCo App includes 25 easy-to-edit SWMS templates as well as all the other health and safety tools you need to protect your crew and your business. Get a free trial.
Reinforcing steel can be used in many ways on a building site. Terms commonly used are rebars and mesh. They are steel bars or mesh wires used to strengthen walls, concrete, or other stone structures.
Workers can fall on the protruding bars which can result in deep lacerations or even life-threatening injuries, so it’s important that preventive measures are in place to reduce the risks.
Some of the hazards include;
Safety Caps
Safety caps are made of plastic so they are a cost-effective way of covering the protruding steel rods. Even though they are small, the safety caps effectively protect against injuries and potential impalement.
Their bright fluorescent colour increases visibility which lessens the chance of the worker walking into, or tripping over them by accident. They are also quick and easy to install.
Control access
In addition to using safety caps, access should be restricted to areas where there are protruding ends.
Injuries can happen when workers are not paying attention to the hazards around them, so ensure that your workers are aware of their surroundings, or physically prevent them from entering the area altogether by using barricades or tape to control access to those areas with hazards.
Keep a clean and tidy site
Ensure that you have a clean and tidy worksite. Gather and remove debris to keep the site free from scraps, and potential trip hazards.
Reinforcing steel scraps lying unattended can rust and pose a safety risk for workers, therefore, make sure you arrange prompt and proper disposal of the scrap materials.
PPE
PPE for people working with reinforcing steel may include;
Best Practices
Construction can be dangerous. There are hazards in all worksites, which can result in life-threatening injuries. Carry out regular site reviews using the HazardCo App to ensure that hazards presented by reinforcing steel are correctly controlled.
Of course, reach out to HazardCo and speak to one of our Health and Safety experts if you have any questions or need more support on avoiding reinforcing steel hazards.
We don’t need to tell you that asbestos is a big deal. The dangers of the substance are common knowledge. And knowledge is power, in this case, more so than most: the power to save lives.
With this in mind, we’d like to give you some basic information on the dangers of asbestos, where it can be found and what you can do to avoid it.
There are two types of asbestos:
Inhaling asbestos fibres can cause a range of irreversible damage and diseases. Damage may occur in as little as five years or as long as 40-50 years later. Many people will not realise they have been exposed until it’s too late.
Approximately one third of all homes in Australia contain asbestos products. On 31st December 2003 asbestos was banned in Australia. Therefore any building constructed up until then has a high probability of containing asbestos. Remember, if you’re planning to renovate or partially demolish a building, have a survey done first to identify if asbestos containing material is present. If it is, contact your local Licensed asbestos removalist.
Yes – as long as strict guidelines are followed. Bagging and wrapping asbestos pieces is essential in any sort of removal – and dumping asbestos-containing materials can only be done on authorised sites. We advise you to leave this to the Licensed asbestos removalists.
Recognition means everything when it comes to asbestos. From sticking up posters on-site to equipping your team with knowledge of asbestos dangers through the HazardCo app, educating your workers could be the difference between life and death.
There are many asbestos awareness and training courses available online and face to face for further education and training.
Got Questions? Reach out to the HazardCo Health and Safety Advisory Support Team on 1800 954 702 to talk it over.
WorkSafe Vic
WorkSafe QLD
SafeWork NSW
SafeWork SA
WorkSafe TAS
WorkSafe NT
Worksafe ACT
WorkSafe WA
The more often you are exposed to a risk, the less your brain perceives the significance of the risk. The level of risk has not changed. Remember how your first time on a busy worksite felt, all those things going on around you. That level of danger is still there. As you have become constantly exposed to it your mind starts to ignore things it thinks are no longer relevant so you have to consciously pay attention to the ever-changing worksite environment. This is how many of the common injuries happen, the brain switches off and you go into ‘autopilot’.
Hit body on object
Manual handling
Nail gun
Hand Tools
Slip/trips
Of course, reach out to HazardCo and speak to one of our expert Health and Safety Advisors if you have any questions or need more support on ways to combat common incidents on-site. You can contact us on 1800 954 702.