HazardCo was created by tradies, for tradies. We understand that on-site risks change, all day, every day, and have experienced what happens when they aren’t well managed first hand. So we formed HazardCo to help tradies get their health and safety sorted – and help you to feel confident that you’re doing the right thing.
HazardCo’s digital health and safety solution uses everyday technology to help you complete all your health and safety requirements – all from your back pocket. Plus, HazardCo helps you to cut back on paperwork and saves you time by using straightforward templates and reports, which are full of tips and suggestions to give you the confidence you have it all covered.
You can use the HazardCo App on your smartphone to create a SWMS, Toolbox Meeting, Site Review, Risk Assessment, Incident Report, Vehicle Checklist, and more. The app is packed with simple-to-use tools that guide you through each of these activities, making them super quick and easy to complete. The HazardCo App enables our members to feel confident that they are on top of their health and safety from anywhere, at any time – whether they’re on-site, taking a coffee break, or even at home after a long day at work.
HazardCo takes the hassle out of getting your team on board because the app is free to download for everyone on-site; this includes subbies, your team, and also visitors to your site. This means that at the site scan-in board all they need to do is use the app or your camera to scan the QR code when they sign in and out which gives you the visibility of knowing who has been on-site and when without having to be there in person. Plus, there’s no need for loads of paperwork and meetings the first time someone arrives on-site – all they need to do is scan in and complete their induction on their smartphone. It’s simple, smart, and time-saving while also giving you the confidence of knowing you have your bases covered.
Along with the app, being a HazardCo member also gives you access to the HazardCo Hub – our digital tool for setting up new projects. All of the information you need is stored online meaning that you can login from anywhere, at any time. Plus, you can use the hub to view, download, and review activity reports, including site reviews, risk assessments, and inductions.
Good health and safety practices are about more than just following the rules; they’re about doing the right thing to keep you and your team safe. HazardCo’s smart digital tools save you time and paperwork, giving you the confidence that you’re doing everything you can to keep your team safe.
We’re proud to announce we now offer WHS / OHS advice and incident support alongside our popular digital tools!
We are offering this service to all members for no additional cost, because we want you to feel confident you are keeping your crew and business safe.
Health and safety is complicated, so whether you are in the office or on-site, if you have a question, are feeling unsure, or have an incident, give our team of experts a call and we will set you right.
Our advisory team is available during working hours to help you with any WHS/OHS questions or problems that may come up. All you need to do is give them a call on 1800 954 702 between the hours of 8am-4pm and they’ll be there to guide you.
These services are available at no additional cost, it’s just another one of the great benefits and features that comes with your standard or premium HazardCo membership. Plus, you’ll receive updates to ensure that your health and safety programme remains fully compliant and up to date.
Our team of advisors has years of experience across multiple industries and will be able to give you a hand with any queries you may have, including:
- What type of documentation is expected from you
- What the controls should be for the task you’re about to do
- Advice for managing contractors on-site
- Understanding WorkSafe visits and notices
- How to keep contractors and visitors safe in your workplace
- Understanding asbestos works, requirements, where to find it, and training
We know that incidents on-site can be stressful and it can be hard to know what you need to report and the right process to follow. Give us a call and we will guide you through what you need to do.
Call 1800 954 702 if you’re in need of a hand.
We’re going to run you through Respiratory Protective Equipment (RPE), which is a type of personal protective equipment (PPE) which protects people from inhaling substances that are hazardous to their health. These hazardous substances include airborne contaminants such as asbestos, hazardous chemicals and dust, fumes (such as welding fumes), and infectious substances, but you should keep in mind that RPE should also be worn to protect the wearer from low levels of oxygen such as working in confined spaces.
But, before you even get started with RPE, make sure you have other practical control measures in place such as local exhaust ventilation to minimise or eliminate contaminants in the air. Also, keep an eye on your team’s health and workplace conditions to ensure that they aren’t injured or made sick by their work.
We’ve gone ahead and put together a quick guide of factors to consider when providing your workers with RPE.
Types of RPE
Respirators that use filters remove contaminants from the air which the wearer will be breathing. Disposable respirators (often called dust masks) are good for short-term or one-off use and protect the wearer from harmful particles such as dust, fumes, fibres, and biological hazards such as bacteria or viruses.
Powered air purifying respirators (PAPRs) consist of headgear and fan assembly that take contaminated air, filters and removes a sufficient portion of these hazards, and then delivers the clean air to the user. These are also known as positive pressure masks, blower units, or blowers.
Supplied air respirators provide a supply of clean air to the wearer from a source such as an air compressor or cylinder. It’s important to note that the air supply needs to be checked regularly to make sure that it is safe to use.
Using RPE
It’s important for your workers to visually check their RPE for signs of damage before each use so that they can let you know if there are any issues, including whether it needs to be cleaned or decontaminated.
Make sure your team stays safe by keeping their RPE on while working in the hazardous area. Removing it for even a short period of time could be a risk to their health.
If your workers are using RPE that requires a tight fit, make sure that they are checking it properly before entering the hazardous area. There are two fit checks which they need to do:
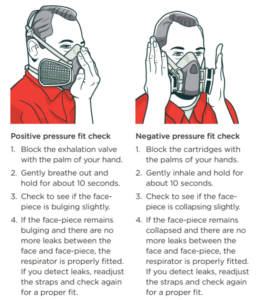
Keep in mind that if your worker’s safety glasses fog up while they are wearing a half-face respirator, this is a sign that there is a leak at the top of the respirator.
Life Shavers: shaving your beard could save your life
When your workers are wearing respiratory protective equipment at work, they should be clean shaven to ensure it is forming a seal and protecting them from breathing in hazardous materials. Even a small amount of stubble can prevent RPE from sealing correctly which means your workers will still be inhaling harmful materials which may cause health concerns. A clean shave goes hand in hand with the correct RPE for the job.
It’s your responsibility to monitor your workers’ health. Make sure that you are completing regular Site Reviews on the HazardCo App, as this will help you to identify potential hazards and put effective plans in place.
Do you know what you need to do before you demolish or refurbish a property, building or structure? Find out what the asbestos regulations mean for you before doing any work.
Identifying Asbestos
Planning is key to identifying all potential hazards and the risks involved when doing any sort of demolition or refurbishment work. Asbestos can be found in buildings constructed or renovated before the year 2000 and as such it is more than likely to be present at your next job.
You can find out more about where asbestos may be in Australian homes here.
Asbestos or asbestos containing material (ACM) must be identified and removed by a competent person before the demolition or refurbishment is started (unless demolition is required to gain access to the asbestos). Things to consider when planning your work:
-
- Are there inaccessible areas that are likely to be disturbed during the demolition or refurbishment?
- What is the type and condition of the asbestos or ACM?
- What is the quantity of asbestos or ACM?
- What is the method of demolition or refurbishment, and how will it affect the asbestos or ACM?
- If asbestos is likely to be disturbed during demolition or refurbishment, can it be removed safely before work starts; if so, how can this be done
- Have I confirmed with my state safety regulator that they need to be informed of the proposed ACM removal works?
If the competent person is unsure whether asbestos is present it must be assumed that it is and all steps taken to mitigate the asbestos risks. If asbestos is identified you must notify all parties involved such as the homeowner, landlord, occupant and/or the contractor in control of the site.
Asbestos Management Plan
Any works where asbestos has been identified will require an asbestos management plan. This outlines where any asbestos or ACM has been identified. Your plan must contain the following:
- the identification of asbestos and ACM (eg where any signs and labels are located)
- decisions, and reasons for the decisions, about how the asbestos risks are managed (eg safe work procedures and control measures)
- procedures for recording incidents or emergencies involving asbestos in the workplace
- information about the workers carrying out work involving asbestos, including
- information and training that has been or will be provided
- their roles and responsibilities
- any health monitoring that has been or will be conducted.
Other information may be included in the asbestos management plan, such as:
- a timetable for managing asbestos exposure risks (eg priorities and dates for removal, reviews, circumstances and activities that could affect the timing of action)
- procedures, including a timetable for reviewing and (if necessary) revising the asbestos management plan and asbestos documentation
- waste disposal
- air monitoring procedures, if required.
Emergency Planning
An emergency plan is required for demolition work where plant and structures contain asbestos. When developing the emergency procedure, you should consider:
- the work being done in the workplace or home
- hazards in the workplace or home
- the workplace or home’s size and location (eg remote location, multi-level site with shared services)
- the number of workers and other people who might be at the work site (eg workers on shifts, maintenance and cleaning personnel, customers, people working alone).
The procedure should include:
- how to respond effectively to an emergency
- evacuation procedures
- notifying emergency services
- getting help, including medical treatment
- effective communication between the person the PCBU authorises to co-ordinate the emergency response and the people at the work site
- provisions for regularly testing the procedure
- what information, training and instruction will be given to relevant workers about how to put the emergency procedure into effect.
The emergency procedure must be carried out if there is an emergency.
If the plant or structure is not structurally sound or is going to collapse, make the area as safe as practical and notify your state safety regulator immediately.
Disposal of Asbestos
Before demolition starts, think of how you are going to dispose of the waste. Having a good waste containment and disposal process is just as important as having safe processes for working with asbestos.
Asbestos is considered special waste and special waste needs to be handled, buried, pre-treated or tested before it can be disposed of at the landfill. You need to make an application if you want to dispose of special waste.
Applications are often called special waste disposal declarations. Contact your local landfill to enquire about what they require before taking any material to them.
Not all landfills or transfer stations are authorised disposal sites, check with your local council to find out where your local authorised site is.
Double-bag all waste. All waste, including single-use masks and coveralls, cloths and plastic sheets should be double-bagged in heavy duty plastic bags. Twist the top of bags tightly, fold the necks over and seal with adhesive tape. Clearly mark the outer bag as asbestos waste.
Check with your receiving landfill for further details especially around handling details. There are often restrictions around how the material is offloaded.
If using skip bins or wheelie bins on site, be aware that many providers of these bins do not allow asbestos to be disposed of in them. Check your provider first for approval.
Document your disposal process in your Asbestos management plan and Asbestos Safe Work Method Statement (SWMS) considering the above.
As a HazardCo member you have access to a library of SWMS located in your Hub, which includes demolition and the removal of non-friable asbestos for anything less than 10m2. Use of these resources will help you to identify the hazards and risks in your workplace and the recommended controls.
Our team of Health and Safety Advisors are here to help you with anything you are unsure of, give us a call on 1800 954 702, option 4.
What is excavation work?
Moving or removing earth or other materials with tools or equipment is generally classed as excavation work. Excavations are used in a number of different situations, such as during the construction of buildings, building retaining walls, and installing underground utilities.
It is important that you use the Dial before you Dig service before carrying out excavations to identify any underground utilities or services.
Some common types of excavations used in residential construction are cut and fill excavating, pile holes, potholing, and trench excavation:
Cut & Fill
Cut and fill excavation, also known as stripping excavation, is the method used to clear and prepare large areas. This method involves removing all of the material such as rock, sand, and topsoil that would be unstable to work on.
Pile Holes
Pile holes are usually excavated using methods including backhoe digger, drilling or hydro excavation. Pile holes should be covered and barricaded as soon as possible and only those involved in the works allowed nearby. Water buildup should be monitored and pumped out.
Potholing
Potholing is simply a small excavation or hole to inspect and find underground services. It’s important that potholes are covered or barricaded when they are not being used to prevent anyone from being hurt.
Trenching
Trenching is an excavation method used to prepare or replace underground utilities, build retaining walls, or investigate what is beneath the surface.
Trenches are long narrow excavations, and are deeper than they are wide. Conducting trench excavation is subject to many different factors including its size, the likelihood of underground utilities, and materials. This means that the most effective method of excavation changes from project to project, and should always be treated with caution.
Due to the scale of some of these operations, it is common that they usually require large excavation vehicles and good controls around traffic management should be in place.
Managing the risk
No matter how deep the excavation is, if there is a risk of collapse, you need to carry out a Risk Assessment and put controls in place to prevent this. You will also need to complete an excavation SWMS in your Hub. Excavation work is classed as high risk, so it is important that if you are completing excavations, that you are familiar with the guidance for Excavations Safety.
The SafeWork Australia Excavations Code can be found here
The Worksafe Victoria Excavations Code can be found here
Covering or bridging.
When covering holes or bridging shallow trenches on building sites, ensure that the material used to cover or bridge is made from a suitable material. Heavy-duty plywood designed for weight-bearing, steel plates, or other products specifically designed for that purpose.
For holes, ensure they are fully covered and the covering cannot easily move. Avoid slip and trip hazards by ensuring walkways around these hazards are managed.
Water hazards after rain can create a drowning risk, especially for children. It can also increase the risk of sidewall collapse.
Types of barriers
A secure site is very important with any open excavation. You need to consider how long the excavations will stay exposed, and if an excavation is to be left unattended overnight, then consider plating, fully enclosing with a safety fence, or backfilling to minimise the risks. Barricades, cones, plastic mesh netting not supported by a solid frame, and hurdles are not sufficient to adequately protect from excavation risks. We recommend safety fences for internal fencing for long-term or unattended worksites where excavation hazards are present
Understand your competency level
Any type of excavation work requires some level of competency to manage it safely. As a guide
For excavations up to 1.5m deep, you should have recent experience in carrying out or supervising excavation work of this type
1.5m – 3m deep you should have recent experience in carrying out or supervising excavation work at these depths, technical or trade qualification (eg a civil engineer or drain layer)
3m and more you should have a Technical or trade qualification (eg a civil engineer or drain layer). Experienced temporary works designer able to judge whether it is safe.
Make sure you are aware of your requirements for managing the risks of excavation.
If you need a hand getting started or would like more information, get in touch with the friendly HazardCo team today – we’re always happy to help.
With the HazardCo App, it’s as easy as picking up a smartphone to stay on top of on-site health and safety activity. And that’s the case for absolutely anyone on-site, from the foreman or site supervisor, to team members, contractors and their crew, as well as any site visitors.
There are two key parts to the HazardCo system, the Hub and the App:
- The Hub is your record of everything and everyone in one place – your online tool for managing and viewing H&S across all of your projects.
- The App puts H&S in the palm of your hand – and everyone else’s hands on-site too. App Users on your account use the App to complete H&S activity for your site, following the straight forward guides and forms to ensure they’ve ticked all the boxes when it comes to identifying and managing H&S risks. And everyone else on-site including contractors and visitors, scans on and off site and completes site inductions with the HazardCo App – simply scanning the QR code on the HazardCo Hazard Board.
As the business owner, a lot of responsibility for H&S sits with you. However, with HazardCo’s digital system, it’s easy to add key team members to your account as App users, meaning any one of you can use the App to complete on-site H&S activity and those day-to-day tasks can be delegated or shared with others. All completed activity lands back in the Hub under your Project Overview, which you can review from anywhere and at any time.
The App features all of the key H&S activities you should be doing on-site, including SWMS, Risk Assessment, Site Review, Toolbox Meeting, Vehicle Checklist, or to Report an Incident. What’s more, if your subbies are also HazardCo members, they can use the App to scan onto your site and share any of their completed H&S activity directly to your Hub using the QuickShare feature on the App.
Learn more about all of the features on the HazardCo App and see just how straightforward it makes H&S for you and the team… this video overviews the HazardCo App, showing you all you need to know. Nothing beats the feeling of confidence you’ll get from being a HazardCo member.
Homes built or renovated between 1950 and 2000 are likely to contain some asbestos. Therefore, every tradesperson is likely to come into contact with asbestos at work sooner or later. That’s why it’s important for you to understand how to manage the risk from working with or near asbestos, and how to protect yourself and others from exposure to airborne asbestos fibers.
Surveying and Testing
Areas that we recommend getting tested are cladding, roofing, vinyl, fibre cement sheeting, internal ceilings, and plumbing lagging.
There are 3 main types of testing or surveying; Management, Refurbishment, and Demolition, and each of these is designed for a specific purpose.
- Asbestos Management Survey: Are designed to locate asbestos in a property. This survey is typically used prior to minor maintenance work or to help manage any potential risks associated with asbestos.
- Asbestos Refurbishment Survey: Are designed to locate asbestos in a property before major work commences.
- Asbestos Demolition Survey: Are designed to locate asbestos in a property before it is demolished. This survey is also designed to give clearance to the area once demolition has been completed.
It is important that when you are conducting work that requires planning permission, it is likely that you will require a demolition or refurbishment survey to search for asbestos present. As the contractor, you have a legal requirement to ensure asbestos is identified and removed before any work begins that may disturb the asbestos in your client’s home.
You can refer to the SafeWork Australia website for more details on asbestos here
Discovering Asbestos
What to do if you or your workers uncover or damage materials that may contain asbestos:
- Stop work immediately.
- Keep people away.
- Minimise the risk of spreading contamination to other areas.
- Get advice from an expert such as an asbestos assessor or a suitably qualified health and safety consultant. You can call our advisory team on 0800 555 339 and we will guide you through your next steps.
Removing asbestos
- All friable asbestos removal work must be carried out by a licensed asbestos removalist. This includes work on asbestos lagging, asbestos insulation, and damaged asbestos board.
- If more than 10 m2 of non-friable asbestos has to be removed during a project, it must be removed by a licensed asbestos removalist.
- You can refer here for a register of Licensed Asbestos removalists .
You can view the SafeWork Australia website to find out how to apply the 10 m2 rule to an object that is not flat, such as asbestos piping and other frequently asked questions relating to Asbestos Licensing here
Hazardous substances refer to chemicals or substances which can be toxic, corrosive and can cause harm. So it makes sense that we document what’s on-site and when.
If you have hazardous substances on-site, there are processes that, by law, you need to follow to ensure they are stored, used, and disposed of correctly and to reduce the risk to anyone that uses or comes into contact with them.
On 1 January 2021, Australia began a two-year transition to the revised edition of the Globally Harmonised System of Classification and Labelling of Chemicals (GHS 7). This new system replaces the previous Approved Criteria for Classifying Hazardous Substances.
Despite the transition period, we recommend you start making the changes to labelling, SDS, and packaging as soon as possible.
You can find out more about the changes below so you can make sure you are up to date with the latest info.
There has been changes to the Hazard Classifications, and you will no longer use the following classes for your hazardous substances:
- Class 1 Explosives
- Class 2 Flammability gases
- Class 3 Flammability liquids
- Class 4 Flammability solids
- Class 5 Oxidising
- Class 6 Toxic
- Class 8 Corrosive
- Class 9 Ecotoxic
The new GHS7 for hazardous substances will be classed as a physical hazard, a health hazard or an environmental hazard, detailed below:
Physical hazards
- Explosives
- Flammable gases
- Flammable aerosols
- Oxidising gases
- Gases under pressure
- Compressed gas
- Liquefied gas
- Dissolved gas
- Refrigerated liquefied gas
- Flammable liquids
- Flammable solids
- Pyrophoric liquids
- Pyrophoric solids
- Self-heating substances
- Substances and mixtures which, in contact with water, emit flammable gases
- Oxidising liquids
- Oxidising solids
- Organic peroxides
- Corrosive to metals
Health hazards
- Acute toxicity: Oral, dermal, inhalation
- Skin corrosion/irritation
- Serious eye damage/eye irritation
- Sensitisation of the Respiratory tract or skin
- Germ cell mutagenicity
- Carcinogenicity
- Reproductive toxicity
- Specific target organ – toxicity single exposure
- Specific target organ toxicity – repeated exposure
- Aspiration hazard
Environmental hazards
- Hazardous to the aquatic environment
- Hazardous to the terrestrial environment. (This hazard class is not part of the GHS 7 classification system, but was added to ensure risks to the terrestrial environment continue to be managed.
What this means for you
You will need to ensure that your SDS, packaging and labelling of substances has been updated to reflect the new classes or you are in the process of updating. This can be done by reaching out to the supplier or manufacturer of substances.
What is a Hazardous substance register?
This is a list of all your hazardous substances (including hazardous waste) that is used, handled, or stored at any of your sites or workplaces. Having a register will ensure you know the substances you have on-site, the requirements you need-to-know, and what to do in case of an emergency.
Keeping a Hazardous substance register
Keeping your register in a central location on your site means that in case of an emergency, it can be accessed quickly by anyone who needs it. There are some key bits of information that need to be included on your hazardous substance registers. Not only do you need the information below, but you must also make sure that the register is up to date and available on-site.
- The name of the substance
- Issue date of the current safety data sheet t
- The maximum quantity that is stored at the workplace
- Where it’s located
- Specific storage requirements
- Any hazardous waste
Because the register represents the maximum amount of the substance held, it means it’s not going to be a daily task to keep it up-to-date. But if the maximum quantity changes, the register needs to reflect this. We recommend that you review your register each time you make a change to ensure it’s up to date and accurate.
Why not kick off the year by keeping your health and safety sorted, starting with a Risk Assessment via the HazardCo App? Risk Assessments help you identify hazards, assess the risk, and implement controls to help prevent incidents.
The HazardCo Risk Assessment feature is perfect to use before starting a new task or at the beginning of the day, but remember if you need to review the full building site, complete a Site Review instead. So, take a few moments to think about any major tasks coming up, and then open the Risk Assessment tool. The App gives you a number of question areas – quickly tap each topic and if the risk is not present for this task, select ‘No’. Where the risk is present, select ‘Yes’ or ‘Not Sure’ and the App will give you some options on how to control the risk – simply select any that apply. Of course, you can add your own comments and upload photos before moving to the next topic.
Once all topics are complete, hit submit and the completed assessment is saved to the Hub and available anywhere, anytime. You can also download the assessment and email to others as needed – easy as that.
The App makes completing a Risk Assessment really straight forward, and the suggestions on how to control possible risks give you confidence you’re doing all you can to keep your crew safe. Because the App is in the palm of your hand 24/7, Risk Assessments can be completed at any time… no paperwork needed.
As you get back into the swing of things, now’s the perfect time to start planning the first few weeks on-site and ensuring you start out the way you’d like the year to continue. HazardCo’s Risk Assessments help you keep your health and safety sorted and make sure everyone leaves the site safely at the end of each day.
With everyone coming back to work after a few weeks away, it is the perfect time to review your health and safety on-site. Easing back into work after the Christmas and New Year break may seem difficult with a looming mountain of work ahead of you, but before you get overwhelmed with day-to-day activities, take stock and prepare yourself for the year ahead. So, here are the top suggestions from the HazardCo team to help you start the year with the right mindset.
Catching up on where things are at is a good place to start. Refresh yourself on priorities for your current projects and plan out the next few months to make sure you’re on top of key milestones. Before you crack into any work, conduct a site review – after a few weeks away, you never know what might have happened on-site, so be sure to check it thoroughly and brief the team on any new hazards or site changes.
It’s also a great time to action change, so think about how your projects have gone over the past year… is there anything you want to be doing more of or doing differently? Setting new goals can be really motivating. Some popular health and safety goals amongst our HazardCo members include:
- Reduce the number of serious site incidents
- Increase the amount of reported near misses – big or small it doesn’t matter. (The more near misses identified, the safer your site)
- Increasing the frequency of Site Reviews, Risk Assessments, and/or Toolbox Meetings. Per site, aim to complete at least 2 Site Reviews and 2 Toolbox Meetingsper month.
- 100% of subbies and direct team members, scanning in and out of site 100% of the time
Make sure your health and safety goals are achievable and measurable. Don’t forget to celebrate when you achieve a goal – it can help you and your team build more confidence in yourselves as you see progress, and that keeps you all motivated and inspired to continue trying to improve.
We challenge you to create new routines, such as a weekly Toolbox Meeting that you can do with everyone who is present on-site every Monday morning – as a group talk about current hazards, progress, key activities happening that week, and how you’ll all work together to manage them. The HazardCo App makes it super convenient to complete reviews and conduct meetings from anywhere on-site – so you can get your health and safety sorted from the palm of your hand, and even hold the meeting where the hazards can be seen at the same time. Simple, regular routines can be a great way to build the team and effect change.
It doesn’t take a lot of time to plan how you’d like to approach the year, yet it can have a significant impact on your achievements and your crew’s job satisfaction. Whatever your goals are, the team at HazardCo wishes you a safe and successful year, and we look forward to working with you on your health and safety goals this year.
Looking for something in particular?
Working with heavy machinery and managing traffic on-site can be risky. But with the right checks and planning, we can keep everyone safe.
Daily machinery checks
Before starting work each da...
Digging into the ground might seem straightforward, but excavation work is actually one of the most dangerous parts of construction. That’s why it’s important to plan ahead and put the right s...
When you're able to get back on site after a flood or storm, here are the hazards, risks and control measures you should consider to help reduce the risk of injury and illness to yourself, you...
Dust is a common hazard in the construction industry, especially during demolition or refurbishment. When buildings are demolished they can release materials that create hazardous dust (airbor...
The holiday season is over and now it’s time to get back into the swing of things. Coming back to work and reopening your site is just as important as shutting it down. The New Year is the per...
The holiday season is almost upon us, and we’re all eager to have a bit of a rest, recharge, and spend quality time with our families. As we wind up 2024, it is a demanding time for constructi...
Electricity is essential on construction sites, but if the risks are not managed properly, it can pose serious dangers to people and property. Proper controls must be in place wherever electri...
Health and safety is a core part of any business but incidents and injuries on the job can still happen. According to SafeWork Australia, in the construction industry alone there were 15,877 s...
You’re probably across the recent engineered stone ban, but did you know SafeWork Australia has just come out with new rules to further protect workers from crystalline silica found in other b...
HazardCo understands that on-site first aid is about more than just sending someone on a course every few years. As an employer or principal contractor on-site, you have a legal and moral obli...
It's important for young people starting out in construction to understand how to stay safe at work. Young workers lack experience and might not know about all the hazards yet, which could put...
Tools, vehicles, and heavy equipment all create vibrations that can affect your body. This is a normal part of any tradie's day, whether you're picking up power tools or jumping in the ute. It...