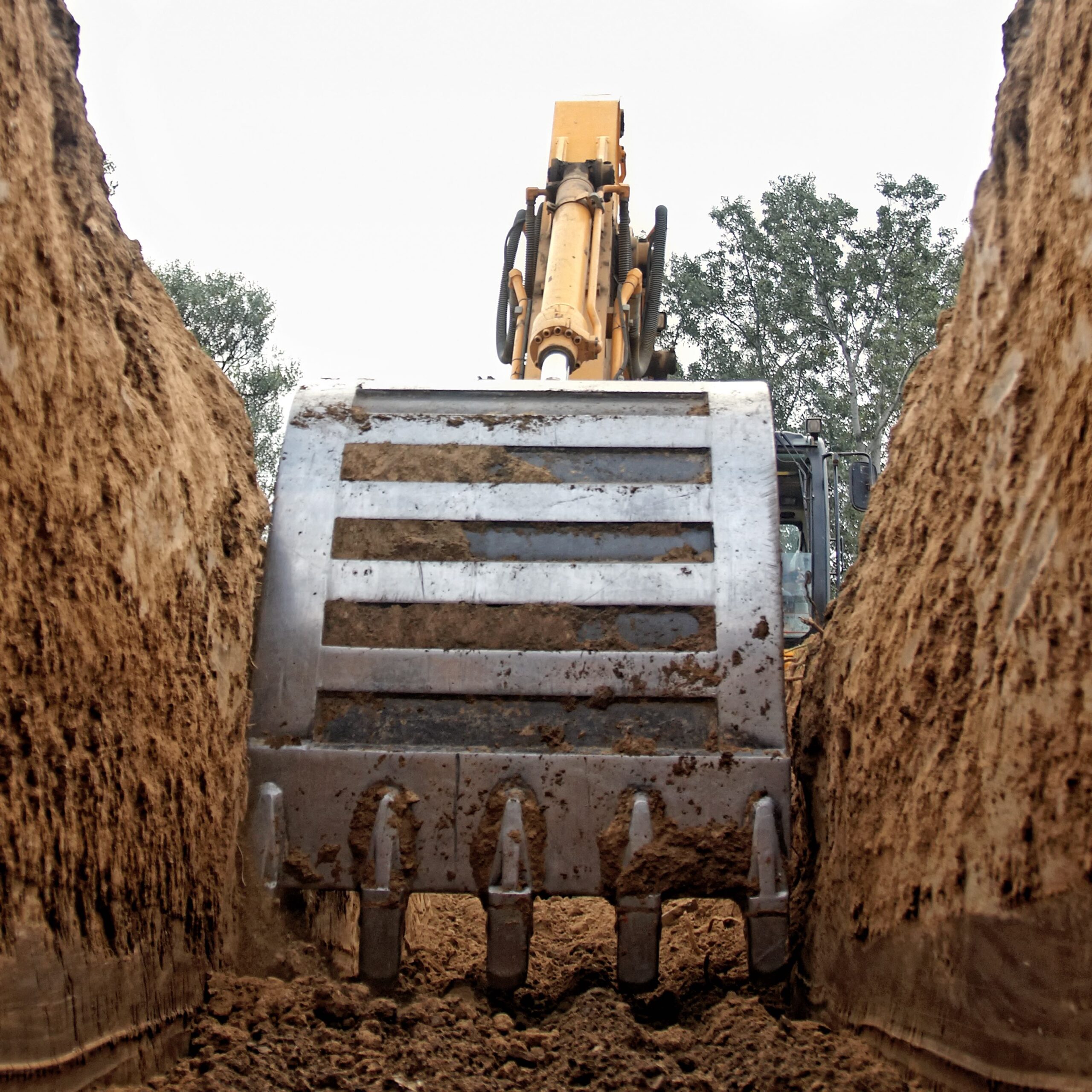
Given how close we are to our neighbours over the ditch, we compare ourselves to Australia in almost every aspect. From sports and culture to economics and lifestyle, we like to think we can keep up with our big brother and show them a thing or two. However, the stark difference in workplace safety and our fatality rate, in particular, is a wake-up call for everyone working in high-risk industries.
On average, there are 73 work-related deaths in New Zealand each year. Relative to the number of people in employment, the NZ workplace fatality rate is double the Australian rate and hasn’t shifted in many years. The NZ rate is similar to those the UK experienced back in the 1980s, making it very clear there is significant room for improvement.
The gap between New Zealand and Australia is consistent across most industries and occupations. Looking at just the construction industry, the NZ fatality rate is 4.41 workers in every 100,000 compared to 2.93 workers in every 100,000 in Australia.
Our workplace injury rates tell a similar story. NZ injury rates reported by ACC have improved over time, however, the Australian rate is 25% lower, and the UK is 45% lower.
Behind these statistics are real people, with families and friends dealing with unimaginable loss when their loved one never returns from work. There is also a very real economic impact, with New Zealand’s workplace accidents and deaths costing the country $4.4 billion. If we could improve our workplace safety performance to match that of Australia, we would reduce costs by nearly $1 billion each year. With 137,939 people out of work in 2022 and receiving weekly compensation from ACC, our high injury rate is also contributing to labour shortage issues.
The 2023 State of a Thriving Nation report says that experts have identified “several factors generate more heat in the system overseas.” For example, in both Australia and the UK, the regulatory environment sets clearer expectations and is firm with enforcement. Australia also has more active trade unions and invests more in new technology.
New Zealand’s workplace fatality statistics are a wake-up call for everyone working in the construction industry, an area that accounts for a large proportion of all fatalities.
The best way to reduce fatalities is to Plan, Do, Check, Act. Focus on the risks on-site which could cause a fatality or a life-altering injury. They are the ones that you want to manage first. Remember, managing risks is more than just using PPE or putting in an administration control.
Looking at NZ construction industry safety statistics over the last five years, the areas that contribute to the greatest number of fatalities are;
These are areas of greatest risk and therefore the areas that should be monitored and reviewed most closely.
The construction industry has additional H&S challenges arising from the volume of contractors and subcontractors from various specialties that must work together on a single site or project. This was reflected in our 2023 member survey where just 66% of building companies agreed that “workers on site (including contractors) are reliable at following H&S procedures and managing/recording H&S where applicable.”
When it comes to how to improve safety engagement with workers and contractors on site, Evette McClure, H&S Advisory & Customer Support Lead at HazardCo says, “When you break it down, ensuring safety on-site can actually be quite simple – it all comes down to communication. Communication is at the heart of all important safety procedures, and it’s the foundation of effective safety management.”
“Good communication creates a culture where everyone is aware and works together. It makes it easier for people to raise concerns and find solutions. In the end, having a culture of strong communication is vital for preventing incidents and keeping everyone safe on the construction site. Just remember, as with anything, it all starts with you. You need to lead by example, start conversations, work together, and create an environment where everyone feels encouraged to participate. You need to be the one to make the change, because if you don’t, nobody else will.”
Although the comparison of workplace safety between New Zealand and Australia is concerning, it shows us that we can and should work to improve our workplace fatality statistics.
We have previously shared content on what to expect when your workplace is inspected by WorkSafe/SafeWork. Now – what happens in the event that your business has received a Regulator’s Notice from WorkSafe?
If the inspector does find an issue, you and the inspector will discuss what needs to be done to fix it. The three main outcomes issued by the inspector are an improvement notice, a prohibition notice or an infringement notice.
We’ve put together our top recommendations on what you can do after receiving a regulator notice.
Carefully read the notice and follow all the instructions listed in the notice. This is particularly crucial if it’s a prohibition notice, as it means certain work must be stopped immediately. Work is not to continue until the Inspector is satisfied certain action has been taken to make the activity/area safe.
Make sure the site entry report and associated notice/s are provided to the Director/ Owner of the Business. We also recommend sharing the notice with other project sites /areas of the business so that they can assess their area to see if similar issues are present or where there is room for improvement. This is a great way to improve health and safety across all areas and sites of the business and to demonstrate Health and Safety is a top priority for all.
Bring the notice to the attention of all persons whose work is affected by the notice (e.g. conduct a toolbox talk and record it in the HazardCo app). Discuss how the business will address the items and by when. We recommend you provide regular updates to the workers on this matter. If you have any Health and Safety Representative (HSRs) who represents workers whose work is affected by the notice, make sure a copy is provided to them.
Make sure a copy of the notice is put up and displayed in a prominent place at or near the part of the workplace where the affected work is being performed (and we recommend you communicate to workers where this can be located).
Promptly discuss with relevant suitable persons who will be involved in addressing the notice (e.g. conduct a meeting with management, supervisors etc) and prepare an action plan to address all items that have been highlighted in the notice. Regularly track action items for timely closeout.
Ensure you document and record discussions, meetings, and agreed actions. Record and track health and safety actions by creating and assigning tasks on the HazardCo Hub or on the App.
Collate all the evidence requested by the notice that will demonstrate you have addressed all the items listed and provide it to the Inspector prior to the due date for their review.
Remember HazardCo is here to help. Give us a call on 0800 555 339 and speak to our Health and Safety Advisory support team for further guidance.
We know that getting contractors involved in H&S is a big challenge for building companies and is exposing you to additional risk. That’s why we’ve created a number of new contractor management tools that will help you to manage your contractors before they begin working with you and while they are on-site. We’ve also made it easier to monitor your contractor’s H&S activity even if you’re in the office.
We’ve developed our Contractor Management system with feedback and input from all the major players in the industry to make sure it matches what kiwi home builders and tradies need. HazardCo’s Pre-qualification tools has been supported by Construction Health and Safety NZ (CHASNZ), the organisation who launched the Totika Pre-Qualification scheme.
CHASNZ, the organisation who launched the Toitika pre-qualification industry standard says “HazardCo’s Complete Plan is an excellent solution for home builders and trades to put in place for their contractors. The HazardCo system helps to grow H&S knowledge in a simple way that’s easily understood and actioned by home builders and trades. It aligns with the Tōtika standard, so those that undertake the Totika assessment after using HazardCo’s Pre-Qualification should find the experience much quicker and simpler”
Tōtika is an ‘umbrella’ scheme created by Construction Health and Safety New Zealand (CHASNZ). Totika independently approves NZ pre-qualification assessment providers to provide a central contractor/supplier register. If you’ve recently worked on a government job, or you’re worked in the Civil or Commercial sector, chances are you’ve heard of Totika and your business may be pre-qualified with a Totika member scheme.
We see it as a great fit with Totika to continue to support the H&S maturity and knowledge in a sector that can find it, at times overwhelming
Please note, HazardCo is not a Totika member scheme. If you’ve been asked to provide a Totika pre-qualification a HazardCo pre-qualification on its own will not qualify. .
Get peace of mind your contractors are good to go, with an automated system to pre-qualify your contractors, check insurance, trade qualifications and more. Because it’s automated, you won’t have to chase contractors for outstanding documents, and you’ll even get a notification if someone scans-in who hasn’t been approved.
Get your hands on all the tools and advice you need, from managing contractors and on-site inductions to making sure the crew has easy-to-use guided tools. You’ll know everything is covered, and saved in one place. No more photocopying, filing, looking for lost paperwork, and feeling like you are in the dark about the health and safety taking place on your sites.
As always if you have any question please reach out to the team today
Common incidents on-site: The more often you are exposed to a risk, the less your brain perceives the significance of the risk. The level of risk has not changed. Remember how your first time on a busy worksite felt, all those things going on around you. That level of danger is still there. As you have become constantly exposed to it your mind starts to ignore things it thinks are no longer relevant so you have to consciously pay attention to the ever-changing worksite environment. This is how many of the common injuries happen, the brain switches off and you go into ‘autopilot’.
Hit body on object – corrective actions and recommendations
Manual handling – corrective actions and recommendations
Staple/nail gun – corrective actions and recommendations
Hand Tools – corrective actions and recommendations
Slip/Trips – corrective actions and recommendations
Of course, reach out to HazardCo and speak to one of our expert Health and Safety Advisors if you have any questions or need more support on ways to combat common incidents on-site. You can contact us on 0800 555 339.
Timber frame standing and truss erection can be back-breaking work! It is often high risk work with some serious potential injuries. We recommend these three steps are completed prior to every install. And ensure that everyone understands the process and their role, from when frames and trusses arrive on-site all the way through to standing.
Here are 3 recommendations to ensure that your site is safer during the arrival and installation of frames and trusses:
The development of Risk Assessments and Task Analysis are crucial to your workers to ensure their safety throughout the build. To make these processes easy, you can complete these on the HazardCo App.
Some things to think about when creating a Risk Assessment for frame and truss delivery and erection are:
Is the work area secure?
Clients, visitors, and members of the public cannot enter the area and workers are aware that they should only enter if they are required for the tasks.
Have all site inductions been carried out and an emergency plan developed for any at height work?
Have all workers who work at height been trained to do so? Is access to height suitable and is fall protection in place?
Have all workers been provided with the correct PPE? Are all tools and equipment available and in suitable working order for the task?
The purpose of a Task Analysis is to go into detail for each of the tasks to be carried out. Thinking about the hazards at each step and how they can be appropriately controlled.
You should think about:
The results from the Risk Assessment, Task Analysis, and control measures should be discussed with all workers prior to work starting.
On paper, this sounds like a lot of work – but it is made simple by using the HazardCo App, and creating Task Analysis templates that you can save as templates and amend again and again. You’re not having to start from the beginning for tasks that you complete regularly. Do remember to check over your templates before approving them as different sites can present different hazards that you don’t want to miss (overhead power lines as an example).
When working at height, either on a second story or setting trusses you need to ensure that your workers are safe, not just from falling, but from tools, equipment, or product falling too.
Scaffolding
Once the lower level frames have been stood/braced appropriately, safe working platforms should be installed such as scaffolding. Scaffolding over 5m should be erected by a trained and competent person and all scaffolding should be checked by a competent person regularly.
Edge protection
If the potential of a fall cannot be eliminated when working on a roof, some form of edge protection should be used to isolate workers from a fall. This includes working on single-story buildings and structures. Using the existing scaffolding as edge protection is often the simplest solution. If this is not practicable, then elevating work platforms or temporary work platforms should be used. Toe boards should be fixed to temporary edge protection as a way of containing all materials, including debris and loose tools.
Safety netting
Safety netting can be installed to protect workers, tools, and equipment from falling.
Only safety netting that has been installed correctly can be relied on to support the weight of a worker so that it can resist the force of a person falling onto it. Tests for UV deterioration of safety nets must be done at least every 12 months and a current test label must be displayed on all safety nets older than 12 months.
Worksite traffic can be a major cause of harm on work sites. When it’s close to having your frames and trusses delivered to site and you’re considering dates with the delivery company, it is essential to communicate the traffic management plan with them. This provides the company and drivers involved with a clear picture of how the site has been structured and can assist the delivery company in selecting the correct sized vehicle for the delivery, taking into account the site size and structure.
Ensuring that you implement the above can prevent many injuries on site, as well as regular toolboxes, making plans for ‘what if’ situations (rescue plans) and discussing these with your workers to keep them alert so they’ll know what to do if an incident occurs on-site. For some useful information on the safe installation of roof trusses please view this resource from WorkSafe
As we dive into the late summer season, the agriculture, horticulture, and manufacturing sectors are buzzing with activity. There’s silage, hay, and seasonal harvests going on at the farms and big amounts of processing happening in the factories. Overall, the goal is to optimize productivity and get it done safely.
At the heart of achieving this lies good communication.
At HazardCo, we make technical terms simple so let’s unpack something WorkSafe (H&S Regulator) drives at this time of year.
WorkSafe talks about the “three C’s”: Consult, Coordinate, and Cooperate.
This is something you’re legally required to do at work, let’s look at how to turn it into something powerful and useful for you and your team.
Have a minute before you take to the paddocks or the floor to figure a few things out. Ask yourself, how will we all consult with our team and the other businesses we’re working with to decide who will do what, when, and where? By being clear early on, everyone can share their thoughts on how to work in better and safer ways. You can also take this time to address any concerns. Consultation sets the stage for the way forward, whether it’s through meetings, brainstorming sessions, or digital platforms.
Coordination is about agreeing on the way forward in a coordinated way.
For example, ask yourself, how will we communicate in the work environment to keep everyone on the same page? Will we use radios for places where you can’t get reception or can’t see each other? How can we make our signage and procedures simple and clear for our manufacturing facilities? Coordination creates efficiency and clarity. By being clear on what you are using to communicate, when and what you will do, you can navigate big tasks with the ease and precision that we are so well known for in NZ.
Collaboration is essential, but so is accountability. Without it we are just saying things without action. Decide on who takes charge for where you are, and who ensures that the plan is executed effectively. Cooperation involves working together and also holding each other accountable for the results. Whether it’s appointing team leaders, conducting regular work observations, or creating and maintaining a culture of mutual support and feedback between your teams, cooperation done well results in a sense of ownership and commitment across the board.
In the agriculture and horticulture sectors, distance and terrain pose challenges, so investing in good communication tools like radios with enough power for your range or even sat comms becomes invaluable. Manufacturing is no different, overcoming obstacles like noise and visibility limitations requires proactive thought to keep teams connected, informed and flowing.
At HazardCo, we’re here to support you every step of the way. If you have any questions don’t hesitate to get in touch with our health and safety advisors.
Below you will find guidance on what to do in the event of an attack or site emergency involving an assault or an armed offender, including some practical advice on minimising the chances of an attack on-site.
Check:
Speak Up:
Ensure:
It’s important to be aware of Critical Incident Stress (CIS)
A “critical incident” is an event that can be so emotionally intense that it can be hard to handle using our usual ways of coping. These could include situations like a sudden death, serious injury, or a physical or psychological threat to the safety or well-being of an individual, workplace or community regardless of the type of incident.
Typical symptoms of Critical Incident Stress include:
There are some techniques and professional assistance you can reach out for:
Informal debrief with peers post-event:
This can be done with supervisors, senior team members, or just work colleagues. Try and assess those team members who may need further support. Keep assistance within your training, and reassure colleagues that support is there for them with the provision of support numbers or how to access EAP services if available.
Employee Assistance Program (EAP)
EAP Services provides brief, solution focused support, to help workers deal with any difficulties they may be experiencing and to minimise the impact on their life. Counselling is available via video, over the phone or face to face. It’s important for employers to ensure that they have EAP services organised for their employees before an incident occurs.
Seek professional assistance to help you run a Crisis Management Briefing (CMB)
A Crisis Management Briefing (CMB) is one of the most highly utilised and versatile crisis intervention techniques. A CMB is a structured group meeting designed to provide information about the event.
Critical Incident Peer Support Groups use CMB’s as a way to share education about typical stress reactions and to provide information about basic stress management and coping techniques and resources.
Seek professional assistance and run a Critical Incident Stress Debriefing (CISD)
Following trauma exposure, an individual can experience multiple emotional, mental, and physical symptoms that impact their well-being. CISD is a practice that allows survivors to process and reflect on the traumatic events they’ve experienced and gain personal control over the incident.
Helplines that could be useful:
A Health and safety policy is a broad “statement of intent” for your business. It states how you will manage health and safety in general, or certain specific areas e.g. your stance on drugs and alcohol use.
Health and safety procedures are the steps you will take to meet your health and safety policies, for example, “we will do XYZ”. Your procedures should be shared with your workers, as well as businesses you work closely with, so they can understand what procedures you have in place and how to follow them.
The Health and Safety Work Act says workers must “follow all reasonable policy or procedures they have been notified of,” so it’s important that you have both your policies and procedures documented and available to your staff.
These documents will outline your commitment to prompting a safe and healthy workplace and will explain how the business will operate safely and what everyone’s commitment to health and safety looks like. It will also explain what procedures are in place to manage risks, and what to do if something goes wrong.
Businesses are often asked to provide their Policy and Procedures (P&P) document to clients or employers to show their commitment to H&S. For example, a main contractor such as a building company) might ask a plumbing business to provide a copy of their P&P document before they begin working with them. Being able to showcase your standard of health and safety can help you to stand out against the competition.
To create a comprehensive policy and procedures document, you’ll need expertise in health safety, including a deep understanding of relevant legislation and best practice. Seeking assistance from a qualified health and safety advisor is the best option.
Luckily, if you’re a HazardCo member, we’ve created a combined policy and procedures document for you. It’s written by our team of health and safety experts especially for NZ tradies and builders operating in the residential construction industry. If you’re already a member, you can download your policy and procedures document from the HazardCo Hub.
The HazardCo P&P includes policies on Injury Management / Return to Work, Alcohol and Other Drugs, Workplace Discrimination, Harassment, Bullying, Mental Health and Wellbeing and Environmental.
We recommend that you read through the P&P document (make sure it all makes sense – give us a bell if it doesn’t)
The next step is to communicate and consult! Get your team together and have a toolbox meeting to make sure they are aware of all the policies and procedures, and talk to your team about what changes will need to be made within your business. This will assist with making sure that everyone is managing H&S well.
Remember it’s important to regularly monitor and review your H&S practises across the whole business including out on-site. This will help you to maintain a safe and healthy work environment for all and continually look for areas of improvement.
Reinforcing steel can be used in many ways on a building site. Terms commonly used are rebars or waratahs. They are steel bars or mesh wires used to support walls, concrete, or other stone structures.
Workers can fall on the protruding bars which can result in deep lacerations or even life-threatening injuries, so it’s important that preventive measures are in place to reduce the risks.
Some of the hazards include;
Safety Caps
Safety caps are made of plastic so they are a cost-effective way of covering the protruding steel rods. Even though they are small, the safety caps effectively protect against injuries and potential impalement.
Their bright fluorescent colour increases visibility which lessens the chance of the worker walking into, or tripping over them by accident. They are also cost effective, quick and easy to install.
Control access
In addition to using safety caps, access should be restricted to areas where there are protruding ends.
Injuries can happen when workers are not paying attention to the hazards around them, so ensure that your workers are aware of their surroundings, or physically prevent them from entering the area altogether by using barricades or tape to control access to those areas with hazards.
Keep a clean and tidy site
Ensure that you have a clean and tidy worksite. Gather and remove debris to keep the site free from scraps, and potential trip hazards.
Reinforcing steel scraps lying unattended can rust and pose a safety risk for workers, therefore, make sure you arrange prompt and proper disposal of the scrap materials.
PPE
PPE for people working with reinforcing steel may include;
Best Practices
Construction can be dangerous. There are hazards in all worksites, which can result in life-threatening injuries. Carry out regular site reviews using the HazardCo App to ensure that hazards presented by reinforced steel are correctly controlled.
Of course, reach out to HazardCo and speak to one of our Health and Safety experts if you have any questions or need more support on avoiding reinforcing steel hazards.
Everyone should make an effort to stay healthy… When it comes to construction and the health of your workers, you are likely often working in loud or dusty environments, with airborne contaminants (e.g. silica or asbestos dust). In these instances, there is a legal responsibility to monitor your worker’s health. You need to complete specific health checks to monitor the impacts on your workers health while working in these conditions.
As an employer, health monitoring is something you should provide for your workers. It is a proactive way of ensuring your workers aren’t at risk in the workplace.
It is not an alternative to effective hazard control measures, rather, it helps you understand the effectiveness of your controls being used on-site.
If a worker’s health is being affected by exposure to construction-related health risks, it’s best to find out as early as possible to prevent any further harm from occurring. It’s intended to detect the early signs of ill health or disease (e.g. silicosis, asbestosis, mesothelioma, noise-induced hearing loss) and helps you monitor and protect your workers from exposure to construction-related health risks.
Health monitoring does not include general wellbeing checks or programmes, since things like cholesterol checks and healthy living programs aren’t specific to construction work.
You’ll need a registered medical practitioner with experience in health monitoring to perform, or supervise the medical tests. To assist your health monitoring efforts, HazardCo has partnered with Habit Health who provide medical checks nationwide. They’re experienced in health monitoring for the construction industry.
Remember, like all on-site health and safety, prevention is key. To ensure you’re meeting your legal requirements when it comes to health monitoring, get on-site with the HazardCo App, and complete an updated Site Review today. This will help you identify your hazards and put effective controls in place alongside health monitoring. Your HazardCo Advisory Team is available throughout the day to guide you through this – call 0800 555 339 to talk it over.