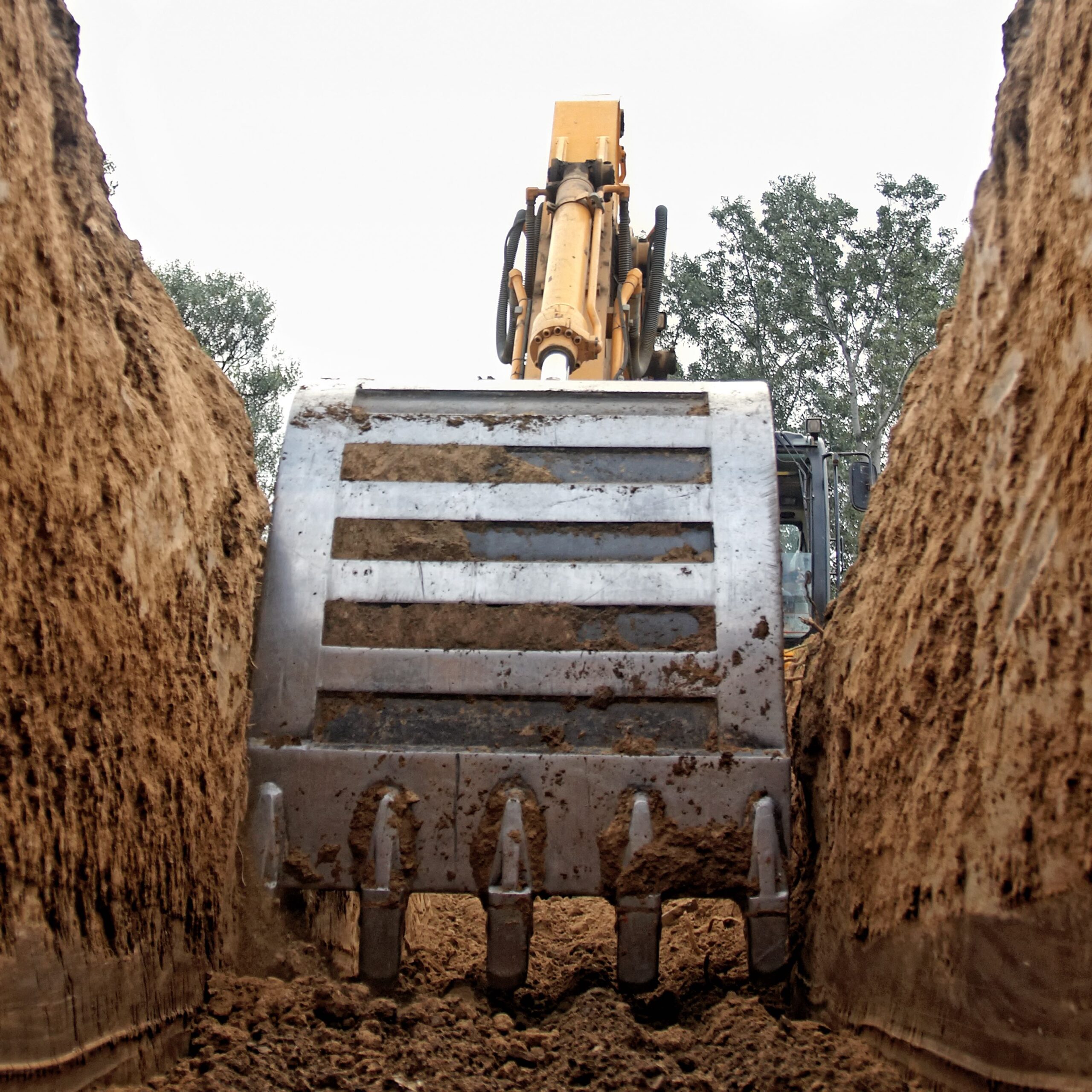
Working with heavy machinery and managing traffic on-site can be risky. But with the right checks and planning, we can keep everyone safe.
Before starting work each day, make sure your equipment is ready to go:
Visual checks (before starting the machine):
Stationary function test (with the machine on):
Moving function test:
Using your manufacturer’s checklist or the HazardCo Heavy Machinery Prestart checklist can help you cover all these points.
Keeping vehicles and people safe on-site requires a solid traffic management plan. Here’s what to consider:
Discuss this plan during site inductions so everyone knows the rules and expectations.
Heavy machinery can affect the stability of excavations if operated too close. Keep all heavy vehicles, materials, and spoil at least one meter outside the zone of influence unless specific designs support closer operations.
Uneven ground can cause machinery to tip over, leading to serious injuries. To prevent this:
If you would like more information head over to our website or to chat with one of our friendly Advisory team please give us a call on 0800 555 339.
We’re excited to announce the launch of the new HazardCo Premium plan for Agriculture, Horticulture, and Manufacturing customers. This plan is packed with extra industry-specific guided content and tools to help you confidently manage your health and safety needs, protecting both your crew and your business.
You’ll get access to these tools and content at your renewal date when you move from HazardCo Standard to Premium. If you’d like to access the new features in advance, please get in touch with us.
Your Task Analysis (TA) reports have been updated with additional guided content, tailored to your industry. This makes it quicker and easier to complete your reports, while ensuring you’ve considered all relevant hazards and implemented appropriate controls.
A Task Analysis breaks down complex jobs into smaller steps to identify and reduce risks in agricultural, horticultural, and manufacturing settings. This practical tool helps workers spot potential dangers—from equipment operation and chemical exposure to repetitive tasks—before accidents happen.
By examining each step of high-risk activities, managers can apply safety measures following a priority system: first trying to remove the hazard completely, then using safer alternatives, adding engineering safeguards, creating better work procedures, or providing protective equipment as a last resort. This organized approach not only protects workers but also ensures businesses follow safety regulations. Regular updates to these analyses keep safety measures current as work methods and equipment change across these industries.
The Safety Review report helps you conduct a thorough health and safety review of your site. It captures site activity with photos and comments, providing clear prompts on what to look for. The latest updates make the tool more tailored to the Agriculture and Horticulture industries, ensuring you’re covering all the relevant safety checks for your specific site.
For Manufacturing customers, we’ve introduced a new tool in App called Safety Walkaround. This tool is similar to the previous “Safety Review”, but with updated content specific to manufacturing. It walks you through what to look for from a safety perspective, and allows you to capture information with photos and comments to document potential hazards.
The Policy and Procedures document outlines your commitment to maintaining a safe and healthy workplace, preventing work-related injuries, and managing health and safety effectively.
Written by our health and safety advisors based on the latest legislation, it has been customised to meet the specific needs of the Agriculture, Horticulture, and Manufacturing sectors.
You can download your company’s Policy and Procedures document from the HazardCo Hub. We recommend reviewing this document with your team in a safety meeting, discussing any changes needed to ensure everyone is on the same page with your health and safety policies.
If you’ve got questions or need support, just reach out to the HazardCo team – we’re here to help.
Operating Machinery
Working with heavy machinery can be dangerous. Incorrect use or untrained operators can lead to serious injuries or worse.
Training and Supervision
Machinery should only be used by workers who are:
Regularly assess operator competency through refresher training, observations and feedback. Keep training records and verify workers have the appropriate licenses.
Before using any machinery, complete a daily prestart check. These checks must be done by a trained and competent person.
Visual checks (before turning the machine on):
Stationary test (machine is on but not moving):
Moving test (short drive):
Use the manufacturer’s pre-start checklist, the HazardCo Heavy Machinery Prestart Checklist or the HazardCo App Plant/Machinery Pre-start tool to guide your checks. Making sure to keep a record of your completed checks.
Quick Hitches, Safety Locks, and Exclusion Zones – Take the time to get it right
Quick hitches help you swap attachments fast – but can be dangerous if not properly secured.
Before operation:
All quick hitches must clearly show:
Store spare locking pins with the machine, and only use attachments that match the correct pin size.
Cover any machinery risks and controls in your task analysis and share it with everyone on-site.
Don’t cut corners on safety
Missing a step like skipping a daily check or rushing an attachment change can have serious consequences.
Taking five minutes to do it right can prevent serious injuries and keep your sire running safely.
If you have any questions, get in touch with the HazardCo Team today
Digging into the ground might seem straightforward, but excavation work is actually one of the most dangerous parts of construction. That’s why it’s important to plan ahead and put the right safety measures in place to keep everyone safe on site.
Before you get started, take time to plan things out. Planning means identifying the hazards, assessing the risks, and deciding suitable controls – with input from the team. Make sure an emergency plan is in place in case something goes wrong. Every site is different, so take its unique features into account when planning.
Keeping yourself and your team safe is what matters most. Make sure you’re clear on your responsibilities when it comes to managing excavation risks.
Need a hand? The HazardCo App has helpful resources for site reviews and risk controls. And if you’ve got questions or need support, just reach out to the HazardCo team – we’re here to help.
We get it — figuring out what to do after an incident or near miss on-site can feel a bit overwhelming. One of the most common things our Advisory Team hears is, “Do I need to report this?” If it’s a notifiable event, you have a legal duty to let WorkSafe NZ know – Sounds like a lot of paperwork right? Not with HazardCo, our App makes it easy to log an incident or near miss and we’re here to guide you with what to do next!
If someone needs immediate medical treatment beyond on-site first aid, someone’s health and safety was put at serious risk, it might be classed as a notifiable event. When you report it through the App, we’ll let you know if you need to give WorkSafe a call.
Every time you report an incident or near miss, you’re helping make the site safer. It’s not about pointing fingers — it’s about learning from what happened and stopping it from happening again. Everyone on-site has the right to know about any risks, and we all play a part in keeping each other safe.
Creating a culture where everyone feels comfortable reporting issues means better communication and fewer surprises.
It’s easy:
Your report is saved in the Hub and kept on file while you’re a HazardCo member
The App will prompt you to give us a call if needed. Our Advisory Team gets a copy and will:
We recommend:
Keep records
You’re legally required to keep these records for at least 5 years. Logging everything in the App means it’s all saved in the Hub, organised and easy to access if you ever need it.
No one wants accidents to happen on site, but being prepared makes all the difference. Stay calm, follow the steps, and give us a call if you’re unsure. Our Advisory team is available 24/7 for serious incidents.
Got a question? Reach out to us today — we’re here to help.
Dust is a common hazard in the construction industry, especially during demolition or refurbishment. When buildings are demolished they can release materials that create hazardous dust (airborne contaminants) which can be hazardous to workers’ health. Understanding the risks will help you to identify how best to manage the risks.
Why is dust dangerous?
Exposure to hazardous dust can lead to serious health conditions, including:
Health and exposure monitoring
As a business, you have a duty to monitor your workers’ health when they’re exposed to dust and other hazardous materials. Regular health monitoring helps identify early signs of illness and ensures that the dust control measures in place are working effectively.
Health monitoring process should include:
It is important that you get your worker’s consent to monitor their health and engage them in this process.
Health monitoring should be carried out by a trained and competent person. For more information or if you’d like to organise health monitoring for your business contact our partner Habit Health.
How to Control dust exposure on-site
Controls to minimise the exposure to dust in the workplace could include:
Making sure your workers have the right tools and information to complete the job safely includes training and understanding the risks involved, what to do if anything should go wrong, as well as the correct use, storage, and maintenance of PPE.
Other controls to consider are:
Complete a Task Analysis for your demolition work through the HazardCo APP. This helps assess the risks and plan safe work processes. Involve your team so everyone can contribute and understand the plan.
Our team of health and safety experts are just a call away if you have any questions or would like to discuss further.
When it comes to working at height, understanding the difference between fall prevention and fall arrest is critical. Fall prevention, also called fall restraint, stops you from being able to fall in the first place. Think of it as keeping you safely away from the edge. Fall arrest, on the other hand, is a backup plan, it doesn’t prevent the fall from happening, but catches you if one happens, reducing the risk of death to injuries that are survivable, depending on what you hit.
This blog explores fall arrest systems, covering the gear, techniques, and best practices to prevent falls or reduce injuries if a fall happens. To make it even easier to follow, we’ve included short videos demonstrating each step. Let’s break it all down.
Not all gear is created equal! In fall arrest situations, quality isn’t optional – it’s life-saving. In New Zealand and Australia, fall arrest equipment must meet at least AS/NZS Standards.
Before anything else, confirm that your equipment complies with these standards, and if it’s something else like EN or ISO standards stop and ask questions, if you’re not sure who to ask then call us on 0800 555 339. Look for labels or certifications and ensure you’re using gear designed for fall arrest and not just general-purpose climbing equipment, because yes, there is a big difference!
A fall arrest system is only as strong as its weakest point. Just like building a house, the foundation must be solid. Your anchor point must be able to withstand the forces generated during a fall – this typically means being rated for at least 15kN (1,500kg) for 1 person 21kN (2,100kg) for 2 people.
Ask yourself:
Connectors are often overlooked, but they’re a vital part of your system. Use auto-locking karabiners over traditional screw gates – they’re faster to secure and less prone to accidental opening. As can be seen in the video showing the differences between manual and autolocking gates.
Be mindful of your connector positioning to avoid “roll-out.” Roll-out occurs when a karabiner rotates under pressure, such as a fall! Forcing the gate open. The video here should get you thinking…. Am I actually protected? Or do I just look protected?
The key takeaway is to ensure:
When selecting the thing between yourself and the anchor, you have three main options:
Each material type has its unique advantages and limitations, so consult an expert if you’re unsure about the best choice for your work situation.
Fall Arrest Devices come in 3 types. Most commonly you will see the “roofers kits” in the safety shops, these have a type 1 device that will move towards your anchor but not away from it without your input.
A type 2 is much like a seatbelt, they are Self Retracting Lanyards also known as SRLs, these are pretty easy to understand, and they will have their limitations printed on the device.
Type 3 fall arrest devices are like type 2 but the key difference is that they are retractable, these are what most people use for confined space entries where the entrant may have to be “winched” to safety if they pass out
All Lanyards that are the link between you and the device must include a shock absorber also known as a personal energy absorber. It’s like the brakes on a car, it slows your fall gradually, reducing the impact on your body. Without one, it would be like using a concrete wall to stop your car! Stopping that fast can generate forces over 4kN (400kg), which is enough to seriously injure or even kill by doing serious damage to your neck.
Shock absorbers are designed to limit the force put through your body to less than 4kN (400kg), protecting your neck, spine, and internal organs.
Your harness is a major piece of the puzzle, and proper fit is everything! Harnesses come in different sizes (S, M, L, XL), so check the manufacturer’s instructions for their size chart to ensure it’s the right size so you can fit it properly.
Key fitting tips:
A poorly adjusted harness can turn a fall arrest into a painful or life-threatening situation.
When working at height, it’s not just your safety that’s at stake – it’s the safety of everyone around you. One small slip of a tool can lead to serious injuries, property damage, or expensive delays.
Here’s why it matters:
In fall arrest scenarios, gravity isn’t your friend! Because your fall is uncontrolled, there’s the risk of striking whatever objects are in your path on the way down. A standard hard hat simply won’t cut it here. Use a safety helmet with a modified chin strap to keep it securely in place during a fall. A good helmet can make all the difference between walking away and serious injury that stays with you for life.
Setting up a fall arrest system isn’t just about having the right gear or looking good.
It’s about understanding how each component works together to keep you safe. Follow the steps above, inspect your equipment regularly, don’t cut corners, and never work alone when using harnesses as you will need a solid rescue plan!
If you’re unsure about which equipment is right for your situation or need help finding out about setting up your systems, get in touch with our qualified H&S advisors.
It’s better to ask questions now than face the consequences later.
We are here ready to talk when you are 0800 555 339
advisory@hazardco.com
Health and safety regulators in New Zealand, are WorkSafe (the main regulator) Maritime NZ, and the Civil Aviation Authority (CAA) is here to work with you, and your workers, to keep everyone safe and healthy. Their goal is simple: to ensure that New Zealand businesses are safe and healthy places to be.
Visits to your workplace can be either pre-arranged or unannounced. Inspectors are allowed by law to show up at any reasonable time, regardless of whether or not you’re there. So, what should you expect when they come a-knocking?
Typically being inspected by WorkSafe follows a four-step process:
A friendly chat isn’t that scary, right? When the WorkSafe inspector first arrives, they’ll sit down with you and have a conversation. This discussion is a two-way street where they’ll want to learn about your business, the risks you have, and the steps you’re taking to minimise them. It’s also a great chance for you to ask any questions you may have.
If there’s nothing urgent that catches their attention, the inspector will typically focus on areas aligned with WorkSafe’s current KPI’s, as outlined in their latest strategy.
Worksafe has outlined three key areas of focus in their strategy:
Following the chat, the inspector will take a walk around your worksite to see if what they’ve heard from you matches up with what they actually see happening. The best thing that you can be during this, is curious. It may feel uncomfortable at times and that’s ok, discomfort just means that there’s space to grow. You’ll know you’re nailing it when it’s just a comfy casual coffee walk around.
If the inspector sees anything concerning during their walkabout, they will follow up with you to dig deeper, understand the root cause, and work out how it can be resolved.
When this happens, they will ask you a range of questions. To keep it simple, focus on the actual question being asked and remind yourself “respond, don’t react”. No matter what they point out, their questions will essentially boil down to these three:
It’s okay if you need clarification – Never feel like you can’t ask them to clarify a question further for you so that you can give them the most accurate answers you can. And if you don’t have an answer right away, it’s perfectly fine to say “I’ll come back to you with that”. Write the question down, involve your team, and follow up with the requested information. This shows the inspector that you have systems in place and are actively using them to ensure safety.
At this stage, the inspector might ask to see what kind of systems and processes you keep. This could include anything from your worker’s licenses or training certificates, machine maintenance logs, to incident reports. The focus will be on whether your records and systems support good health and safety practices for your worksite, workers and business.
That’s where your HazardCo records can make a big difference! Having a clear history of Risk Assessments, Task Analysis, Site Reviews and Toolbox Talks can go a long way in showing that you are proactive about workplace safety.
Outcomes:
If the inspector does find an issue, you’ll discuss together what needs to be done to address it.
The three main outcomes that may be issued by an inspector are as follows:
As mentioned earlier, you’ll know you’re on the right track when your interaction with the inspector doesn’t feel like an argument but more like a constructive discussion. The goal is to leave the conversation with a clear understanding of how your “referee” wants to call the game, while the inspector walks away knowing that your business isn’t one of the ones driving New Zealand’s harm statistics.
Using HazardCo can make this even easier—cutting your health and safety admin time in half while guiding you through the steps needed to keep your crew and business safe.
If you have any questions or need support, don’t hesitate to call us at HazardCo on 0800 555 339. We’re here to help!
The holiday season is over and now it’s time to get back into the swing of things. Coming back to work and reopening your site is just as important as shutting it down. The New Year is the perfect opportunity to refocus and set the tone for the year ahead. Coming back to work after a couple of weeks off can give some people a serious case of Mondayitis, so consider taking the following steps on the first day back:
Rather than diving straight into work, start with a kick-off toolbox talk. This is an essential step to rebrief your team on the SSSP (Site-Specific Safety Plan) and emergency procedures. Use this time to check that all workers are fit for work and mentally prepared after the break.
Perform a site review to identify any new hazards or potential risks that may have emerged during the downtime. Check that fences are still secure and containers are locked.
After a break, it’s crucial to ensure all structures and scaffolds are intact. Inspect scaffolds, check excavations, and assess other infrastructure that may have been affected by weather conditions during your time off. Ensure everything is in working order before resuming normal operations.
Before use, inspect all tools and equipment to confirm they are in good condition. It’s also vital to pre-start mobile plant to ensure it’s functioning correctly.
Consider a soft start to your operations. Allow your team the time to properly check their work areas, inspect equipment, and remind everyone that safety is the number one priority. This includes keeping in mind workers don’t overheat after spending the last couple of weeks in air conditioning, relaxing, and indulging. They may not be acclimatised to working in the heat.
As the weather heats up, so can risk on-site. Make sure that workers are provided with adequate protection from working in the heat so that they can do their work safely and comfortably. Here are some steps to help mitigate these risks:
If temperatures are dangerously high, it’s sometimes best to stop work until conditions improve. Consider shifting physical tasks to machinery for tasks such as lifting or digging, reducing the exposure to extreme heat.
Safety is a shared responsibility. Encourage your team to keep an eye on each other and to report any symptoms of heat stress. Prevention is key, but swift action can prevent more severe conditions from developing. For the early stages of heat-related illness, first aid can often be effective, but you should always seek medical assistance if in doubt, or if the person’s symptoms are severe. Symptoms to look out for are:
Be prepared this summer and make sure to keep the health, safety, and well-being of workers front of mind. Refer to the below resources for more information:
If you have any questions you can contact our Advisory Team on 0800 555 339.
The holiday season is almost upon us and we’re all eager to have a bit of a rest, recharge, and spend quality time with our families. As we wind up 2024, it’s a demanding time as we try to complete jobs before the holiday shutdown. This can make it tempting to take shortcuts, however, it can also lead to an increase in incidents, with the last two months of the year seeing a spike in workplace incidents.
Common factors can include time pressure, working in the heat, and fatigue. It’s important to keep the health, safety, and well-being of workers front of mind.
It’s necessary to start preparing for the holiday shutdown so you don’t have any interruptions during your break or come to a nasty surprise on your first day back.
Unsecured areas could be hazardous to members of the public, especially children. Children are unaware of the dangers so keeping them out and away from harm is key.
Download our Site Security Checklist for a comprehensive list.
Taking the time to prepare for the holiday shutdown period can help to make sure you get to spend uninterrupted time with your family and friends.
If you have any questions or would like to discuss your Health and Safety please give our Advisory team a call on 0800 555 339 or email info@hazardco.com.
We hope you have a safe and enjoyable break over the holiday season!