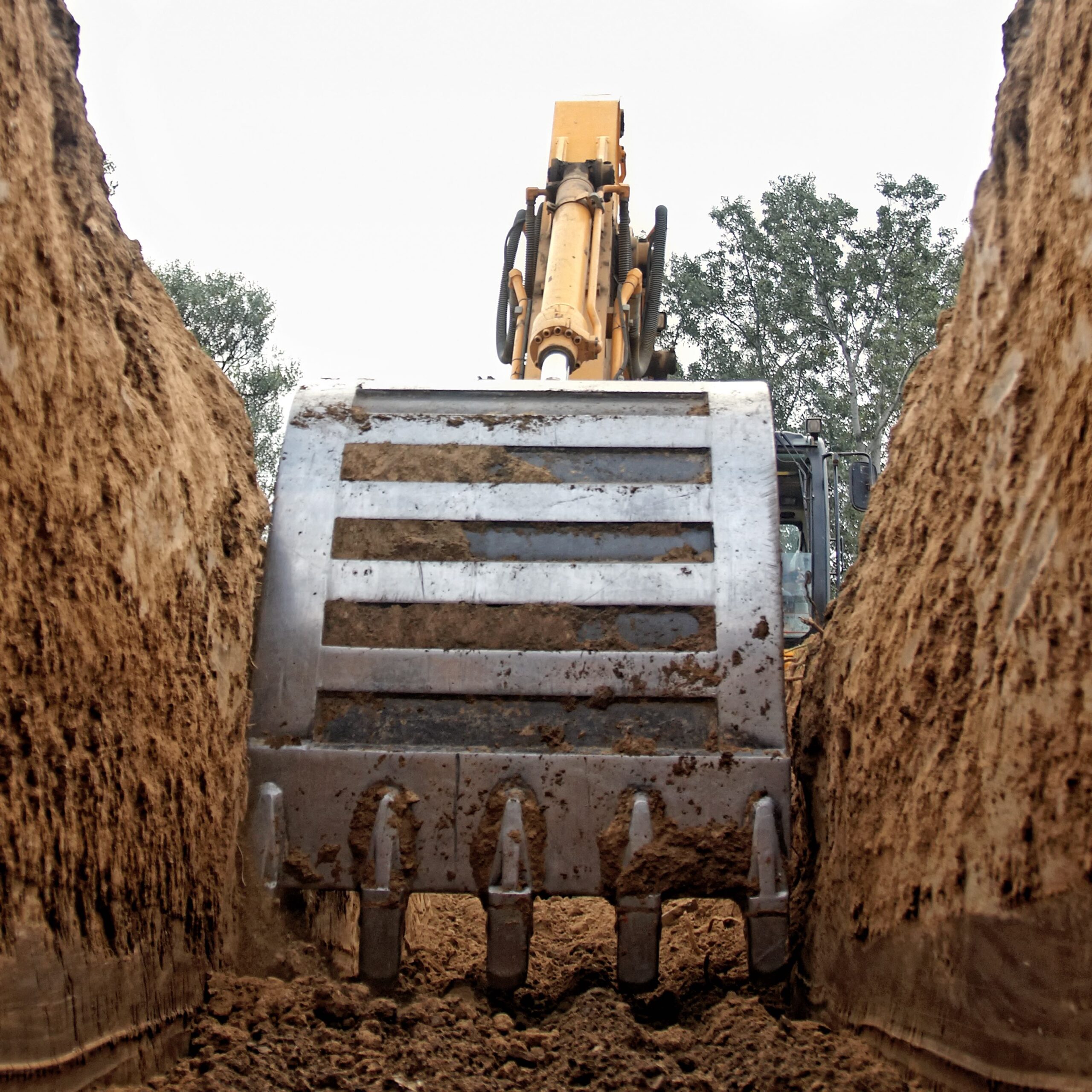
We want to make sure that you have everything you need to work safely in a COVID-19 world. With this in mind, ensure you complete a COVID Task Analysis (you can use this as your COVID-19 Plan) and make sure you share it with your team before turning up to site.
Download yours below, which includes our advice on how to operate on-site safely:
A COVID Task Analysis is a simple and effective tool that helps you identify COVID hazards, risks, and the appropriate controls. All workers involved should discuss the Task Analysis so they understand the controls that will be put in place to minimise the risk of COVID on-site.
It’s important to us that you’re healthy and safe during this time, so get in touch if you’d like to chat about how HazardCo can support you, you can give us a call on 0800 555 339 or email info@hazardco.com.
What is Hi-Vis?
Hi-Vis is a form of Personal Protection Equipment (PPE) designed to minimise the risk of personal injury by making the wearers visible.
The New Zealand legislation has standards around the criteria that hi-vis needs to meet, the types available, and when they should be worn.
As a business owner, you must manage the risks associated with your workplace activities and in doing so follow a process to control those risks. If you cannot eliminate a risk, you must implement measures to reduce the level of risk, provide training to workers, and provide PPE – which can include hi-vis.
Protective clothing is one of many control measures used to mitigate risk, however, it is the ‘last line of defense’, and all other reasonably practicable control measures should be in place first before relying on protective clothing. It is up to the PCBU if hi-vis clothing is a control that will be implemented on-site. However, we do recommend that it should always be worn around moving vehicles, plant and machinery.
Types of Hi-Vis
There are many types of hi-vis clothing available in New Zealand, and it is important to understand the different types., what is appropriate for your workplace, and ensure that you supply hi-vis that meets the standards. The only two hi-vis colours that are acceptable in NZ are yellow and red-orange.Red is only allowed if it is in the orange spectrum. Otherwise, it cannot be considered a hi-vis colour, because it is not easily visible for some people with a specific type of colour-blindness.
Maintaining Hi-Vis
It is important that the correct hi-vis is selected and used correctly. Your workers should know:
Hi-vis should be maintained to ensure that it remains effective, over time the materials can fade which will affect the performance of the tape and fabric. It should be regularly checked for wear and tear, fading, and ensure that there are no additional fabrics, logos, or pockets impacting the functionality of the hi-vis in accordance with the standards AS/NZS 4602 and AS/NZS 1906.4.
If you have any questions get in touch with the HazardCo team
HazardCo was created by tradies, for tradies. We understand that on-site risks change, all day, every day, and have experienced what happens when they aren’t well managed first hand. So we formed HazardCo to help tradies get their health and safety sorted – and help you to feel confident that you’re doing the right thing.
HazardCo’s digital health and safety solution uses everyday technology to help you complete all your health and safety requirements – all from your back pocket. Plus, HazardCo helps you to cut back on paperwork and saves you time by using straightforward templates and reports, which are full of tips and suggestions to give you the confidence you have it all covered.
You can use the HazardCo App on your smartphone to create a Toolbox Meeting, Site Review, Risk Assessment, Incident Report, Vehicle Checklist, and more. The app is packed with simple-to-use tools that guide you through each of these activities, making them super quick and easy to complete. The HazardCo App enables our members to feel confident that they are on top of their health and safety from anywhere, at any time – whether they’re on-site, taking a coffee break, or even at home after a long day at work.
HazardCo takes the hassle out of getting your team on board because the app is free to download for everyone on-site; this includes subbies, your team, and also visitors to your site. This means that at the site Hazard Board all they need to do is use the app or your camera to scan the QR code when they sign in and out which gives you the visibility of knowing who has been on-site and when, without having to be there in person. Plus, there’s no need for loads of paperwork and meetings the first time someone arrives on-site – all they need to do is scan in and complete their induction on their smartphone. It’s simple, smart, and time-saving while also giving you the confidence of knowing you have your bases covered.
Along with the app, being a HazardCo member also gives you access to the HazardCo Hub – our digital tool for setting up new projects. All of the information you need is stored online meaning that you can login from anywhere, at any time. Plus, you can use the hub to view, download, and review activity reports, including site reviews, risk assessments, and inductions.
Good health and safety practices are about more than just following the rules; they’re about doing the right thing to keep you and your team safe. HazardCo’s smart digital tools save you time and paperwork, giving you the confidence that you’re doing everything you can to keep your team safe.
Any questions, get in touch with the HazardCo team today
When it’s not possible to work from the ground, the use of scaffolding is highly recommended to complete those at height tasks. Generally, any building, demolition, or at height repair works will require scaffolding.
There are other height equipment available such as;
Doing a thorough risk assessment is key to determining what the right equipment for the job will be. Use this table as a guide for your choice of height equipment.
As always if you would like to discuss your health and safety requirements further please call our Advisory team on 0800 555 339, extension 4.]
Working at height for work such as building a house, renovations, painting, decorating, or roof work? Scaffolding could be the safest piece of height equipment to use for the job as it provides workers with a flat-level working platform and of course fall protection.
There are different types of scaffolds and the type you will use will depend on the environment you are working in and what is best suited to your task. The common types of scaffolding are proprietary and prefabricated, tube and coupler, and suspended scaffold. If you want to know more about these systems, click here.
Anyone involved in the installation of scaffolding is required to have the knowledge and skills to do so. Scaffolding up to 5 metres should be installed by a competent person. Competent means someone who has the knowledge and skills to carry out a particular task like installing scaffolding. The easiest way to gain this knowledge and skills is through training, qualification, experience or a combination of all three.
It is important that you know that scaffolding greater than 5 metres must be installed by a person who holds the appropriate class of certificate of competence (COC) for the type of scaffolding. Scaffolding over 5m is also notifiable to WorkSafe. This can be done online here.
We have a Scaffolding Task Analysis (TA) that you can use. This TA outlines the hazards, risks and controls that need to be put in place when it comes to installing and using a scaffold. Also available is a pre-start checklist for you to conduct your daily checks before use. These can both be found in the templates section of the HazardCo HUB. We will touch on in week 3 about the when, what, how and why when it comes to checking scaffolds.
Musculoskeletal disorders (MSDs) are the most common workplace injury and cause of lost time at work, so spending time to focus on it makes good business sense.
Research has shown that the old approach of teaching a person how to lift correctly has not been effective in reducing these problems. Many workplaces pay to bring various experts into the workplace to help them address Musculoskeletal disorders but a lot can be done inhouse by those leading the business.
1. Survey your workers for discomfort pain and injury using a body map:
To start a discussion around MSDs print and hang a poster of a body on a whiteboard or wall (see body map at the end of this article). Next to the poster, provide a marker or stickers for the workers to use to place crosses on the body parts where they have experienced pain or other MSD symptoms in the past week or month. Each worker can also make a mark at the bottom of the poster to indicate that they have contributed. When there is the same number of marks at the bottom as the number of workers, or it’s been established that everyone who wants to contribute has done so, the patterns that emerge from the poster can be used for a toolbox discussion and brainstorming session.
2. Ask your workers to take photos of things they think contribute to discomfort, pain, and injury at work:
Ask workers to take photos using their mobile phones over a two-week period. Each person (workers and managers) should take two or three photos of something that they perceive as risky or that they find triggers MSD symptoms at work. They can also take pictures of work situations or equipment that they perceive as helping to prevent MSDs. The quality of the photos doesn’t matter and they don’t have to be self-explanatory. Ask each worker or manager to provide brief explanations of their photos. To give an example of a photo of a risk, it might show the height of a ladder on a vans roof rack (which requires force and an awkward body position for workers to reach). An example of a picture of something that helps to prevent MSDs might be a photo of colleagues helping each other during a pressured time. Each person can be helped to print out their photos and stick them to a board (e.g. in a lunchroom or meeting room). Once the photo shoot is over, arrange a toolbox talk at which all the photos are on display and the topics raised can be discussed. The aim is to establish a shared understanding of what the photos represent.
3. Think about the physical and mental demands on your workers
There are well known physical and mental demands of work that lead to MSDs and lower productivity. Identify if you have any of these issues in your business:
Aim to address these demands by:
4. Where possible get work up off the ground:
Working and handling at ground level places strain on our bodies which overtime can develop into MSDs. Take photos of tasks that require stooping and bending to complete at your workplace. Look for items that are stored on the ground. During toolbox talks discuss ways which the task can be redesigned by raising the work off the ground for example with a trestle, pallets or providing a table. If it can’t be raised, can we extend our tools or modify our position to compensate?
5. Where possible eliminate overhead work:
Jobs that require overhead work are 2 to 3 times more likely to result in a shoulder injury. Overhead work becomes more hazardous when the arms are elevated over 60 degrees. Use a toolbox talk and photos to identify where overhead work is required. Where possible aim to eliminate it and where it must remain look to design alternative ways to complete it. This includes reducing the force required, using lighter and smaller tools, keeping the arm below 60 degrees and using frequent rest breaks.
If you have any questions get in touch with the HazardCo Team today
These days everything is digital. Your payroll is managed online, you keep your team organised via email, and you can even order lunch straight to your site with just a few taps. So why are you still getting bogged down by Health and Safety paperwork?
HazardCo helps reduce the H&S burden with smart online tools to help you cut back on paperwork. Plus, it’s a time saver with its straightforward templates and reports which are full of tips and suggestions to give you the confidence that you have all your bases covered.
You can create a Risk Assessment, Toolbox Meeting, Site Review, Incident Report, or Vehicle Checklist using the HazardCo App on your smartphone or tablet. The app has tools to guide you through each of these tasks, making them a breeze to complete anywhere, and at any time. No longer will H&S be a taxing task because HazardCo members can stay on top of their H&S whenever it works for them, whether that be on-site, while grabbing a morning coffee, or pretty much anywhere that works for them.
We’ve found that people who have embraced going digital as part of their H&S strategy have seen it remove roadblocks, distractions, and excuses – because when you have H&S in the palm of your hand, you can’t not do it. Plus it leads to a safer worksite when H&S is the focus of people’s thoughts and actions.
At HazardCo, we understand the importance of H&S for keeping your team engaged, on track, communicating, and most importantly, safe.
If you haven’t gone digital with your H&S there’s no better time than now. Builders and tradies can start their free seven day trial today and see the difference that HazardCo can make for your H&S plan.
You know that old saying… “no pain, no gain’”. Well this is not true! Just because you work in the construction industry doesn’t mean that you need to be affected by short or long term pain.
Aches and pains are some obvious symptoms of musculoskeletal disease (MSD), but have you thought about what impacts MSD are having on you outside of work in your personal life?
What if constantly performing the same repetitive movement all day is causing you acute pain that means you aren’t able to kick the football around with your kids after work, or play golf on the weekend with your mates? Do you really want your work to impact your personal life, or your workers lives when there are some simple steps that could prevent it from happening?
As a business owner have you thought about the hidden costs?
Data shows that strains and sprains often become more problematic later in a construction worker’s career, with the largest claims in the housing construction sector. Between 2015 and 2019, 57% of ACC claims were MSD injuries, with the average cost being $3700, and a total of 1.9 million compensation days paid out, costing a total of $325m!
There is a large range of costs that surface when someone has an injury on the job, especially when they can’t return to work the next day or sometimes weeks or months. This has a huge impact on deadlines, bottom line, skills on-site and team dynamics.
Risky work that can cause MSD’s can be as simple as overhead or floor level work, manual and hand intensive work.
Have you thought about other ways you could be working to alleviate the stress on your body? It could be as simple as:
It’s common practice when you work out, that you warm-up and cool down, so why is working any different?
Accepting the reality of MSDs helps us formulate an effective approach to combat MSDs in our
Industry. There are a lot of myths out there about MSD, such as its caused by poor manual handling techniques. The trouble with myths is they create unnecessary fear and hinder progress so they need to be challenged. Over time, new evidence emerges to help us understand the reality of the situation and
our understanding of MSDs has changed significantly over the years. For example Len Rings saying “Don’t use your back as a crane” is no longer repeated as we now know you need to move your spine through its whole range of motion regularly to keep it healthy and strong.
Check out CHASNZ top five MSD myths in construction.
Let’s do our bit and raise awareness on-site around MSD. Next week we will give you some exercises that you can do to avoid being affected by MSD and if you are hurt how physiotherapy can help you.
If you have any questions reach out the the HazardCo team
Do you know what you need to do before you demolish or refurbish a property, building or structure? Find out what the asbestos regulations mean for you before doing any work.
Identifying Asbestos
Planning is key to identifying all potential hazards and the risks involved when doing any sort of demolition or refurbishment work. Asbestos can be found in buildings constructed or renovated before the year 2000 and as such it is more than likely to be present at your next job. You can find out more about where asbestos can be found in this WorkSafe resource.
Asbestos or asbestos containing material (ACM) must be identified and removed by a competent person before the demolition or refurbishment is started (unless demolition is required to gain access to the asbestos). Things to consider when planning your work:
If the competent person is unsure whether asbestos is present it must be assumed that it is and all steps taken to mitigate the asbestos risks. If asbestos is identified you must notify all parties involved such as the homeowner, landlord, occupant and/or the contractor in control of the site.
Asbestos Management Plan
Any works where asbestos has been identified will require an asbestos management plan. This outlines where any asbestos or ACM has been identified. Your plan must contain the following:
Other information may be included in the asbestos management plan, such as:
Emergency Planning
An emergency plan is required for demolition work where plant and structures contain asbestos. When developing the emergency procedure, you should consider:
The procedure should include:
The emergency procedure must be carried out if there is an emergency.
If the plant or structure is not structurally sound or is going to collapse, WorkSafe NZ should be notified as soon as possible.
Disposal of Asbestos
Before demolition starts, think of how you are going to dispose of the waste. Having a good waste containment and disposal process is just as important as having safe processes for working with asbestos.
Asbestos is considered special waste and special waste needs to be handled, buried, pre-treated or tested before it can be disposed of at the landfill. You need to make an application if you want to dispose of special waste.
Applications are often called special waste disposal declarations. Contact your local landfill to enquire about what they require before taking any material to them.
Not all landfills or transfer stations are authorised disposal sites, check with your local council to find out where your local authorised site is.
Double-bag all waste, all waste including single use masks and coveralls, cloths and plastic sheets should be double-bagged in heavy duty plastic bags. Twist the top of bags tightly, fold the necks over and seal with adhesive tape. Clearly mark the outer bag as asbestos waste.
Check with your receiving landfill for further details especially around handling details. There are often restrictions around how the material is offloaded.
If using skip bins or wheelie bins on site, be aware that many providers of these bins do not allow asbestos to be disposed of in them. Check your provider first for approval.
Document your disposal process in your Asbestos management plan and Asbestos Task Analysis (TA) considering the above.
As a HazardCo member you have access to a library of TA forms located in your Hub, which include demolition and the removal of non-friable asbestos for anything less than 10m2. Use of these resources will help you to identify the hazards and risks in your workplace and the recommended controls.
Our team of Health and Safety Advisors are here to help you with anything you are unsure of, give us a call on 0800 555 339, option 4.
Demolition is not just the knocking down of buildings or structures, it also includes smaller maintenance and renovation work such as the dismantling of parts of structures (e.g. one part of a steel-framed building) or the removal of walls.
When planning your works you need to first identify the hazards and manage the risks:
When demolition is involved there is always the potential for the collapse of the structures. Ensure structural / supporting elements are identified before demolition (you may need to seek structural engineers’ help identifying these, and in what order to take them down).
Make sure you have the following documents completed and available for your demolition work:
You can find these in your Templates Library in your Hub. You can login to your Hub here.
These should be tailored to the task at hand and regularly updated as changes occur.
If you have any questions reach out to the HazardCo team