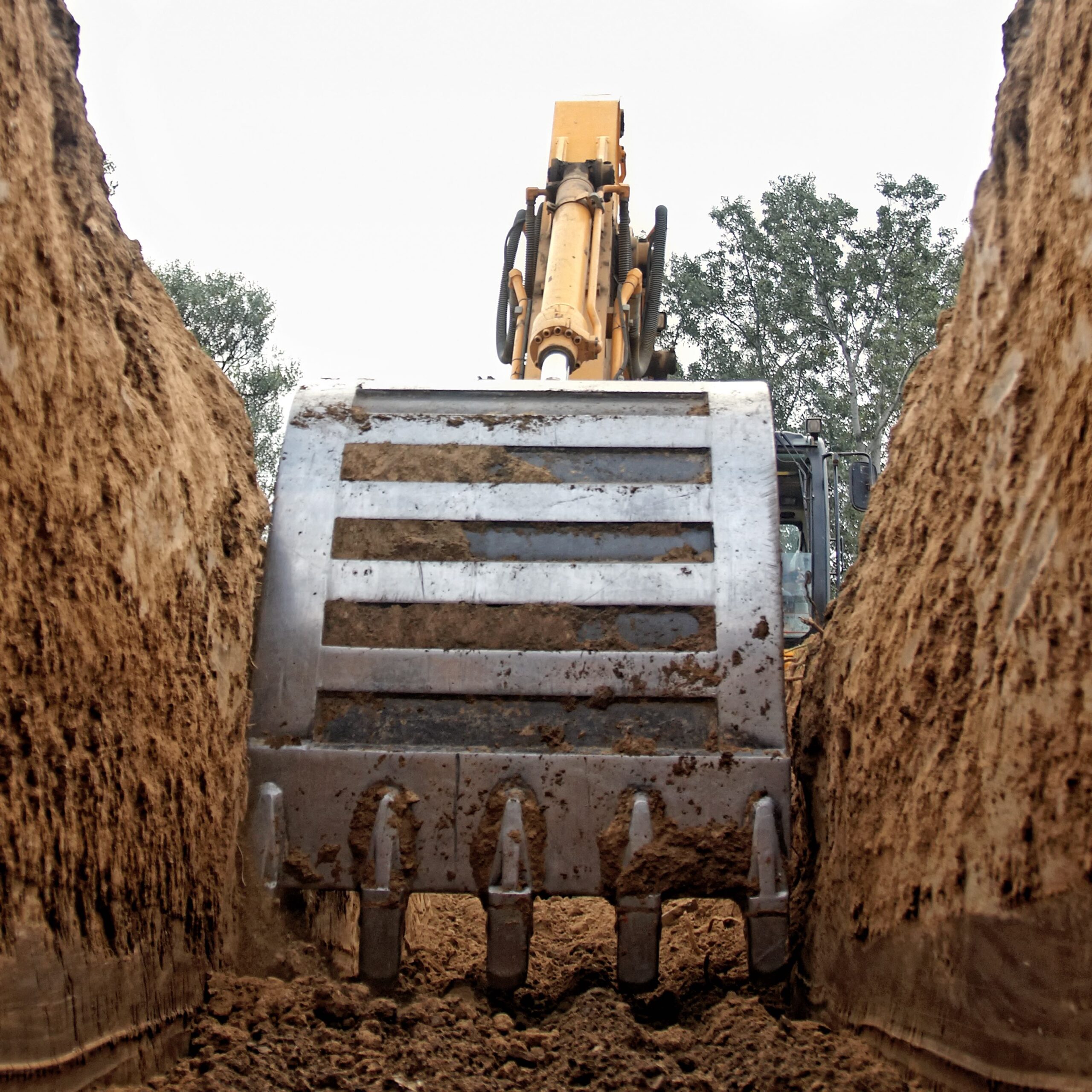
Even if you are self-employed you still carry the same duties under the legislation as the main contractor.
If a contractor, in turn, engages other businesses then they too must assume some of the responsibility for their work. A contractor is most likely to have the greatest influence and control of their own work activities and workers (or contractors).
There should be a way of recording your planning and the ways in which you share this information. All businesses should have access to information to keep themselves or their workers safe.
Your primary duty remains to prevent harm arising from your work. Identify risks that could arise and share information between relevant parties.
The following key steps should be followed by contractors:
Scope
Prequalify
Select
Appoint
Monitor
Review
Working along other businesses is a natural part of residential construction. Everyone on-site has a duty to open up the lines of communication and look out for each other.
You can read more about contractor management and overlapping duties here or if you have any questions about working with other businesses on-site, give our expert Advisory Team a call on 0800 555 339.
This strategic partnership brings together two leading systems, as construction companies across Australia and New Zealand are increasingly adopting on-site technology to ease their administrative burden and work more efficiently.
We make health and safety simple, giving more than 10,000 companies the confidence they are keeping their team and their business safe, while reducing the time they spend on paperwork. Our system provides guided digital tools as well as incident support and health and safety advice when it is needed. We’re most well known for our simple and effective site induction and scan-in solution.
“We’re pleased to be able to integrate Procore with our unique site induction and scan-in solution, making it faster and easier than ever for Procore customers to know who is on-site, and when,” said Nick Halley, Head of Product at HazardCo. “Members receive a hazard board with a unique QR code for their site fence, and everyone uses the free app to scan into site, induct themselves and accept the safety plan, with H&S docs seamlessly flowing back into Procore.”
“Our goal is to make health and safety simple. This exciting partnership between HazardCo and Procore connects construction management and health and safety together, giving building companies an out-of-the box digital WHS system that seamlessly connects with their existing workflows,” said Iain Dixon, Chief Executive at HazardCo.
He concludes, “we regularly speak to builders that are passionate about building scalable and efficient processes for their business, but health and safety continues to be a very manual and paper-heavy activity for them. There are large gains to be made by digitizing health and safety, with HazardCo members telling us they have halved the time they spend on WHS admin using our simple system. This partnership will make it easier for building companies to streamline their processes and give them the confidence they are on top of their health and safety requirements.”
Health and safety issues arise from a worker raising concern about health and safety at the workplace and that concern remains unresolved after consultation with the worker/s and the PCBU (Employer), it then becomes a health and safety issue.
For example, an issue could include a difference in opinion on whether something is a potential risk to health and safety, or whether a particular control measure is acceptable.
There are issue resolution requirements in Health and Safety legislation that outlines how a health and safety issue should be resolved, with the aim to agree on how to fix the problem, as soon as possible, to avoid further dispute or a similar future issue. If after reasonable efforts the issue cannot be resolved, then it can be referred to the regulator (WorkSafe) by completing the ‘Request Assistance to Resolve a Work Health and Safety Matter’ form available on their website.
The following details need to be taken into account when assessing the severity (risk level) of the issue, and from there deciding who needs to be involved:
An agreed H&S Issue Resolution Procedure is a process or steps for resolving health and safety issues in the workplace which has been agreed upon by directors / management / workers.
You can establish an agreed procedure for a workplace. To do this, make sure the procedure contains:
It is recommended to have a procedure in place in the event of an issue arising, or the steps provided in legislation can be followed.
Once the relevant people have been made aware of the details of the issue and the level of risk has been assessed, health and safety regulations set out the default procedure for resolving it.
Multiple people can be involved in the issue resolution process, depending on the risk of the issue, to ensure adequate consultation and the best outcome occurs. This means it could be:
If you or your worker would like to involve representatives in the issue resolution process you are able to do so. A representative does not necessarily need to have health and safety expertise. This could include people such as a designer of a piece of equipment at the workplace, or a person with workplace consultation and negotiation skills. Depending on the nature of the H&S issue, advice or assistance from a range of experts may be required to reach an appropriate and informed resolution between the involved parties.
Things to remember:
When the issue has been resolved, details of the issue and the resolution should be set out in a written agreement. If a written agreement is prepared:
If you’ve got a question about Health and Safety issue resolution or any other health and safety matter, the HazardCo Advisory Team is here to help. Give us a call on 0800 555 339.
When you’re able to get back on site after a flood or storm, here are the hazards, risks and control measures you should consider to help reduce the risk of injury and illness to yourself, your workers and others involved in the clean up and repair effort.
If you have any questions as always get in touch with the HazardCo Team
Have you been asked to complete an external prequalification and you’re scrambling for all the information that you need to get through it?
Going through a pre-qualification process helps to determine how well contractors manage health and safety. It asks businesses to demonstrate an effective health and safety management system and for information on managing specific risks.
You can also use pre-qualification as an opportunity to assist and support businesses to improve their health and safety practices.
To successfully complete a pre-qualification it is important that you have an active health and safety system. This includes evidence to show that your health and safety system is working effectively.
You only need to complete a pre-qualification if you have been asked to. You don’t need to complete a pre-qualification from an external provider unless you have been requested to, this process can easily be managed internally.
Our Advisory Team can step you through the typical questions you would see in an external pre-qualification and advise you on how the HazardCo system can support your application. E.g managing inductions on site, communicating with your workers, how to complete risk management. If you’re keen to access these resources or need assistance with completing a pre-qualification, give us a call on 0800 555 339 or e-mail advisory@hazardco.com
If you need help preparing for a pre-qualification, we can offer this through HazardCo Services in addition to your membership. We can arrange to carry out a review of your health and safety system and provide advice on areas for improvement, prior to you having to complete a pre-qualification.
We can also provide in-house support to help you complete the pre-qualification, or review your pre-qualification before it is submitted and provide recommendations to assist your application.
If you are interested in learning more about HazardCo Services you can give us a call on 0800 555 339.
When we hear the term “red flags” it means there’s a problem, it is a warning sign that something isn’t right when it comes to a particular situation. In the way of a construction site, this could be anything from a messy site, to using out of date H&S paperwork.
Some red flags are more visible or obvious than others, however it’s important to eliminate red flags on your site as they can cause injuries and other issues for you and your crew. We’ve covered some of the most common red flags and how to remove these from your site.
Not having a fence around the site perimeter could invite unauthorised entry. If your site isn’t secure, members of the public or children can enter the site, which could lead to injuries, property damage or stolen items.
Easy, ensure your site has adequate fencing set-up around the perimeter to prevent unauthorised entry. Take into consideration the height and ensure it’s not only high enough, but also check that the gap at the bottom isn’t too big where people, including children, could squeeze through underneath.
A messy site can lead to all sorts of problems. Waste and other objects left lying around can create obstacles for you and your crew. The mess could cause slip and trip injuries which can result in workers needing time off work, something you want to avoid!
Make sure your team is regularly cleaning up after themselves. Waste materials like cardboard, general rubbish and other lighter material can be placed/stored in such a way to eliminate tripping hazards and prevent them from flying off site, especially during strong winds.
Having a skip or bins available and ensuring everyone takes a moment to keep the site clear will reduce the risk of injury for everyone.
The site sign provides all of the important details including an after hours contact number.
If something happens on-site and the principal contractor needs to be contacted, it needs to be easy for anyone to find.
Display a Principal Contractor sign in a visible location which includes the following
information:
If there is no process for identifying the hazards, assessing the risks and what controls are required for a task, it could pose a significant risk to workers on-site.
A Task Analysis (TA) is required for all high risk construction work. Ensure a TA is accessible to the workers performing the task and that they are familiar with its contents.
It’s important that a TA is regularly reviewed. If the TA is not being followed due to a variation of work or conditions have changed, then work must stop until the TA is reviewed and updated.
When people are unaware of incidents or near misses occurring on site, it could lead to the same incident unnecessarily injuring people repeatedly. Also, some incidents legally need to be notified to WorkSafe. A fine can be issued if this does not occur.
Reporting injuries is also important when it comes to making sure the worker receives appropriate treatment, (e.g. medical treatment) and other support, (e.g. return to work).
When incidents, near misses, injuries and illnesses occur on-site it’s important they are reported and investigated appropriately. By recording an incident via the HazardCo App, it automatically populates an incident register on your Hub so that all the incidents are recorded in one central location.
Carrying out investigations is important as they look at why the incident occurred and what controls can be implemented to prevent them from occurring again.
H&S paperwork needs to be kept up to date to help keep your workers safe. If yours is out of date, it could contribute to an incident on-site.
Additionally, lack of H&S documentation (e.g. Risk assessment/Task Analysis) could mean you’re not complying with Legislation so you could be liable for certain prosecutions and/or fines.
If you’re old school and don’t mind filling out H&S paperwork by hand, make sure you are using something that is current, e.g. the TA is specific for the high risk task.
If you’re like us and love using a digital system, use the HazardCo App to get your H&S done quickly and simply. All of our features including the TA and site review are regularly reviewed and kept up to date, including when legislation changes.
Summer is here – longer days, sunshine, and the outdoors sound like the perfect conditions to get all that work done. It doesn’t matter what time of year it is, hazards and risks are forever present and summer brings with it its own risks. Have you thought about what you are doing to protect your team from the effects of the summer sun and heat?
“Slip, Slop, Slap and Wrap” to minimise the obvious risks of sunburn or skin cancer, but we also need to be aware of the risk of heat exhaustion, dehydration and fatigue.
Heat exhaustion occurs when our bodies overheat from the loss of water and salt due to sweating. If left untreated it can lead to heat stroke.
Heat stroke occurs when the body is no longer able to keep itself cool causing a high body temperature of 39.4 degrees or more.
Heat rash and heat cramps are earlier stages of the onset of heat exhaustion. Knowing the signs and what to do will help prevent the onset of heat exhaustion or worse, heat stroke.
If you have underlying health issues that could be affected by extreme heat make sure you let your business know.
Planning is key – With the sun at its peak between 10am-4pm, make sure you take regular breaks within this time and where possible arrange work that can be done in covered or shaded areas to be completed during this time period.
Check out this handy resource on how to protect yourself when you’re outside
Take it easy – Don’t overdo things. Keep strenuous tasks to a minimum and regularly rotate work tasks.
Listen to your body – Just because the weather is nice and you can work longer to get those jobs done doesn’t mean that you should. Fatigue affects your mental and physical capabilities making it harder for you to concentrate. When we lack concentration is when incidents can occur.
Discussing the effects of the Sun (UV and Heat) at your Safety/Toolbox meetings is a great way to remind everyone of this often overlooked environmental hazard. You can easily record your Safety/toolbox meetings using the HazardCo App.
If you have any questions or would like to discuss your work hazards give our Advisory team a call on 0800 555 339, option 4.
Most cement, lime, mortar, concrete, and plaster products are hazardous substances that contain strong alkalis.
As seen in the image above, alkalis are on the opposite end of the PH scale from acids, however, can be equally as dangerous, being extremely destructive to your eyes. The way you handle the first seconds, minutes, and hours after you get the dry powder or wet mix in your eyes, will determine the outcome.
Alkalis may start their damaging work in your eye without much pain or symptoms, but over time the damage gets worse. So beware, follow the first aid steps below even if you don’t feel pain.
Don’t become one of the statistics: in 2021, there were 56 burn injury claims to the eyes in the NZ construction sector, with 90% of chemical eye burn injuries that could have been prevented.
Every second counts! Run to the closest tap, eye wash station or water bottle and start flushing your eye. You are aiming to dilute the alkali to lessen the damage.
Wash your face and hands, you don’t want to get more cement product in your eyes. Flush your eye with a steady stream of running water. Let it pour into your eye while lifting both eyelids to rinse out all the cement granules underneath. Do not reuse the water and do not let contaminated water run into the unaffected eye.
If you do not flush your eye, or stop before you are told to do so, you may suffer from permanent eye damage, dry eyes, vision loss and more.
HazardCo’s Site Box or Emergency Box is ideal for storing your SDS files and eye wash stations on-site. You can also upload and store your SDS and other H&S documents on the HazardCo Hub to keep them all in one place.
If you have an incident where someone gets cement/concrete in their eye, remember to report this as an incident in the HazardCo App. This will automatically be added to your incident register in the HazardCo Hub, and the Advisory team will be in touch with you to discuss next steps if it is deemed to be notifiable to WorkSafe NZ.
For questions or support, contact the friendly advisory team at HazardCo at 0800 555 3339 or info@hazardco.com.
We are excited to announce our partnership with Acuite, a construction-specific reporting and analytics platform, to help small and medium-sized building companies to get on top of their health and safety.
This strategic partnership will deliver powerful new Dashboards, powered by Acuite to HazardCo members, giving them the tools to track health and safety activity and improve safety outcomes.
With so much to keep track of on-site, Dashboards are a practical way for HazardCo members to understand what health and safety activity is taking place across their business and at each project site. Often the business owner or admin staff are based in an office or moving between multiple sites. They want to be able to see at a glance what health and safety activity is taking place, view trends over time, and discover how to improve.
David Speight, Co-Founder, and CEO of Acuite Construction Intelligence says, “the Acuite founders are builders and we know it’s not easy. Through combining forces with HazardCo, we feel we can make a real difference by not only making sites safer but also improving the lives of builders through arming them with the knowledge to put them on the front foot of their projects”
Following the integration, HazardCo members can get real-time insights into key health and safety activities happening on their sites through Dashboards. These Dashboards help users to understand the areas that are performing well, and those in need of improvement in a simple and easy-to-understand way.
Iain Dixon, Chief Executive Officer at HazardCo says “We are excited to be working with Acuite because they are the best in the business for reporting, analytics, and insights. Like HazardCo, they specialise in construction, they come from the industry and keep things simple. We’ve had a great response from our members already with feedback that they are loving the quick snapshot they can get from viewing their Dashboards, and being able to see at a glance what health and safety activity is happening or not happening”.
Acuite is a reporting and analytics platform. As builders themselves, their mission is to improve the lives of those in construction by creating holistic data-driven insights as well as arming them with the knowledge, time, and transparency to make better decisions.
Mental and Physical health can often be overlooked in the construction industry, but it’s a big contributor to time off work. With 78% of workers having suffered a mental or physical injury at work and an average 32 days off work for ACC claim injuries.
Injuries in your industry may seem like they are just part of the job, but they can significantly impact your output if not taken seriously.
Strains and Sprains
The construction industry has become the number one industry for ACC claims with strains and sprains, (also known as Musculoskeletal Disorders or MSDs), making up a whopping 57% of the problem.
Common injuries for construction workers can range from sprains, strains, and contusions (bruising) which can be caused by heavy lifting, repetitive movement, poor body posture, forcefulness or muscle effort, or the vibrations from continuous use of hand tools. Symptoms of a workplace injury can range from any kind of pain and discomfort located in and around the neck, shoulders, wrists, back, and knees.
It is well known that there are a range of factors that contribute to MSDs. It’s not just one single factor, such as the lifting technique (although for industries such as scaffolding and roofing handling techniques are an important factor).
The research firmly points to four groups of factors we need to tackle when addressing MSDs in construction:
Physical factors, such as:
Individual factors such as:
Psychosocial factors such as:
Work Organisation factors such as:
It may not surprise you that physical factors often take most of the blame and focus as their connection is easy to understand, measure and observe. There are also proven strategies to overcome physical factors such as machinery, equipment, and task modifications. Combining the other factors into your approach is where the construction industry will get the most benefit. Understanding how these factors can combine and influence each other to cause problems will be crucial.
The most common solutions to dealing with MSD are:
Data shows that sprains and strains often become more problematic later in a construction worker’s career, with the largest claims in the housing construction sector. Between 2015 and 2019, 57% of ACC claims were MSD injuries, with the average cost being $3700, and a total of 1.9 million compensation days paid out, costing a total of $325m!
There is a large range of costs that surface when someone has an injury on the job, especially when they can’t return to work the next day or sometimes for weeks or months. This has a huge impact on deadlines, bottom line, skills on-site, and team dynamics.
Have you thought about other ways you could be working to alleviate the stress on your body? It could be as simple as:
It’s common practice when you work out, that you warm up and cool down, so why is working any different? Accepting the reality of MSDs helps us formulate an effective approach to combat MSDs in our industry.
Prevention and early intervention are key to maintaining a healthy musculoskeletal system so you can carry out your day-to-day duties on-site and personal activities you love to do in your own time. Ensure you keep fit and healthy; regular exercise, a good diet, and sleep can assist in keeping your body ready to take on work and recover faster.
Did you know businesses are legally required to monitor the health of their workers?
On construction sites, workers can be exposed to many hazards that can cause them harm over time.
Some common hazards are:
Continuous exposure to these hazards can cause progressively worse health issues for your workers. This is why it is important to monitor your worker’s health. Specifically their lung function, hearing, vision, and work-related musculoskeletal conditions.
If your worksite exposes your workers to environments that will cause them harm, we recommend beginning the process of monitoring your worker’s health immediately.
To further assist your health monitoring efforts, HazardCo has partnered with Habit Health, who provides nationwide medical checks. They’re experienced in health monitoring for the construction industry, and their efficient, cost-effective service is discounted for HazardCo members.
They can offer:
Did you know that nearly 1 in 4 Kiwi adults report experiencing poor mental wellbeing? This makes up a significant percentage of our workforce in New Zealand. This means that there is a good chance that you or someone you work with is struggling with or at some stage has struggled with their mental wellbeing.
We all know that work can affect your physical health. There are risks and hazards on-site that can cause you harm like slips, trips, falls, hazardous substances, dust and so many more. Working can also impact your mental health in more ways than one.
Some common workplace hazards that can affect a worker’s mental health are:
Businesses should try to prevent mental health harm at its source. Identifying risks and controlling them should be done by communicating with workers about what workplace conditions are harming their mental health. Things like low job control, low support, poor environmental conditions, and exposure to injury or harassment can increase the likelihood of mental harm.
Businesses should look to create workplaces that remove exposure to stressors, such as:
Start managing mental health at work today. Have a toolbox meeting to discuss the common issues that impact your worker’s mental health. Discuss ways to eliminate or minimise these risks. It’s good practice to keep records of your meetings, this can be done in the HazardCo App.
Get in touch with the HazardCo team if you have any questions