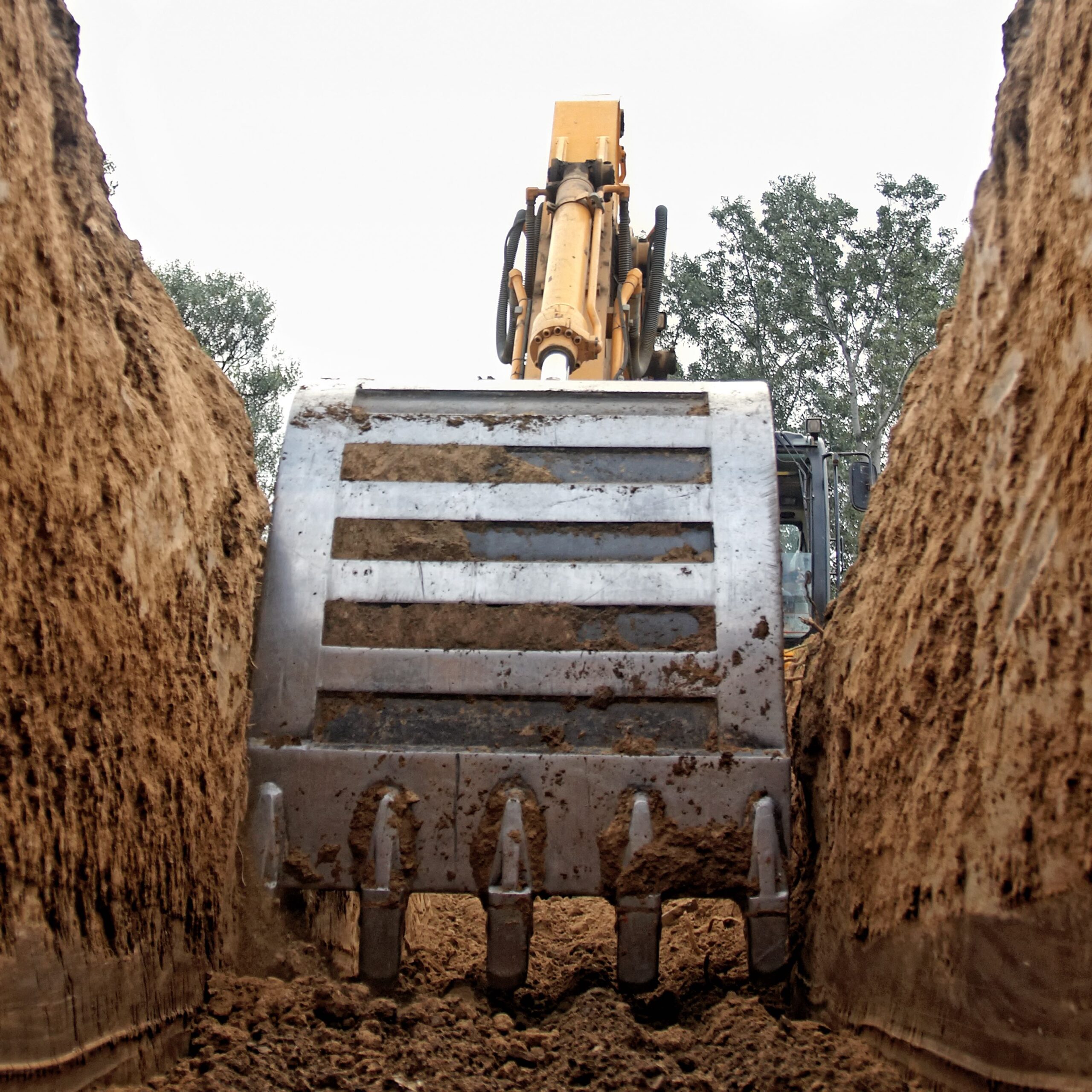
Health and safety is a core part of any business but incidents and injuries on the job can still happen. According to WorkSafe New Zealand’s 2022 – 2023 data, the construction industry had 6,240 injuries which resulted in more than a week off work. In that same year, there were 11 deaths. Construction and trades make up a significant portion of incidents and injuries at work and when you think about not only the cost of life but the time off, loss of productivity and money spent on rehabilitation it adds up to a pretty staggered sum.
From 2022 – 2023 there were 586 Notifiable incidents and 604 Notifiable injuries or work-related illnesses. With numbers like this, we need to help you find a way to improve the health and safety culture so you can make sure it’s safe and profitable as well.
The signs of poor health and safety
If you’re concerned that your health and safety policies and procedures aren’t being followed or maybe not quite up to scratch, there are a number of things you can keep your eyes peeled for:
So, how do you get your crew on board?
When it comes down to it, creating a culture of site safety isn’t as easy as putting new procedures in place and calling it a job well done – it’s up to you to involve and motivate your crew to be proactive and take safety into their own hands.
Some steps you can take include:
Communication
It seems like an obvious one but poor communication can really affect your efforts to create a safety culture. Having regular open communication with your crew about why you’re talking about all things safety is the best way to help them understand the importance.
The more transparent and clear you are, the more likely they will be to action any new initiatives. Make sure that your crew has easy access to your current health and safety guidelines so they can stay in the know about any changes.
Support your staff
If you are taking steps to improve your site safety culture, make sure you factor in both physical and mental health awareness in all that you do for your staff. By providing resources and establishing an environment where your crew feels respected and safe to open up and express themselves you’ll be able to create a support system where you can look after each other’s wellbeing and mental health.
Training
Ensuring that your crew are trained up on all the correct licenses, procedures and health and safety practices is a surefire way to make sure that they are fully knowledgeable on procedures. With the right training in place, you can have confidence that they know how to safely perform their jobs.
Be a leader
If your crew see you leading by example and taking health and safety seriously, they are more likely to as well. So lead from the front and be the one to start those open conversations about what’s going on on-site.
Reporting
You need to set the tone with your crew that reporting incidents isn’t something they need to feel anxious or uncomfortable about doing. Make it clear that reporting is a way of finding out what caused the accident or injury and what can be done to make sure it won’t happen again. By making proper reporting a core element of your crew’s job responsibilities it can become second nature to them.
Make it a team effort
Site safety impacts everyone, so it makes sense that your crew should have a hand in shaping their site’s culture. The more input they have, the more likely they are to follow precautions.
By having regular health and safety chats with your crew, you can give them the opportunity to voice their own safety concerns and opinions. By having open conversations and allowing input from your crew you’re giving them the ability to implement safety measures that affect their own jobs, ultimately making them more likely to follow processes and encourage others to do the same.
If you have any questions reach out to the HazardCo Team today
HazardCo understands that on-site first aid is about more than just sending someone on a course every few years. As an employer or contractor on-site, you have a legal and moral obligation to make sure your team has access to first aid equipment and facilities, as well as access to trained first aiders.
To determine the necessary level of first aid for your workplace, assess the site by considering:
Don’t forget to involve your workers in the process, and if you are working with multiple trades, or are the main contractor, you should share information and work together cooperatively.
Having a kit on a construction site is essential to quickly address injuries and medical emergencies. Great first aid kits can be sourced from many places – a basic kit should at least include equipment to manage:
Basic first aid kits are not always enough given the nature of construction work and increased risk of eye injury, cuts, falls etc, so you’ll need to consider what other equipment to add e.g. eye pads, eyewash, additional dressings and bandages.
Include your team and see if they think your first aid kit is sufficient for the sites hazards and team size. Make sure they know who the trained first aider is and where the first aid kit is kept! Make sure your first aid kit is clearly labeled and is made from a material that can protect the contents from dust, moisture and contamination.
Lastly, assign someone to be in charge of replenishing the kit. Make sure this happens regularly and keep a list of what’s supposed to be in the kit to make topping it up easier. At the same time, check training is up to date for your first aiders, and if your team size has changed, whether you still have enough team members trained in first aid.
Keeping first aid up to date is the right thing to do by your team, so make sure you’ve got things covered and that you’re all prepared if any sort of injury takes place.
If you have any questions please get in touch with the HazardCo Team
WorkSafe recently published a report on Workplace harm and risk in New Zealand. The whopping 106-page report is packed with valuable information on the current state of safety and highlights areas that need improvement to create a safer environment for everyone.
Our certified Health and Safety Advisor Evette has pulled out all the stuff you need to know and provided advice on the safety areas you should focus on to make the biggest impact.
Most work-related fatalities and serious injuries happen in just a few industries. Unfortunately, construction makes the list, as does agriculture, forestry & fishing, manufacturing, and transport.
Over the past two decades, there has been a significant decline in the rate of fatalities and serious non-fatal injuries, with the fatality rate dropping by more than half. However, the pace of improvement has slowed down in the last ten years.
Between 2017 and 2021, New Zealand’s work-related fatality rate was still 40% higher than Australia’s, even after taking into account economic activity and employment differences. Although the comparison with Australia is worrying, it shows us there is potential to improve our fatality rates in NZ.
This graph shows the number of injuries that resulted in more than a week off work from 2022 to 2023. The injury rate accounts for the number of people working in the industry, rather than the total number of injuries.
Construction has the highest rate of all sectors. In other words, a construction worker heading out the door for the day has a higher chance of injury than someone working in a factory, driving a truck, working on a farm, or any other industry.
When we look at workplace injuries, we can group them into five main categories:
WorkSafe found that most serious injuries and deaths occur in just a few industries. To make these workplaces safer, it’s important to have strong safety measures in place. This means better safety rules (and enforcing them), providing proper training and resources for workers, and building a culture that values safety..
Here are some ways you can proactively create a safety culture on your site today:
Lead by example: Take the initiative in promoting safety. Regularly demonstrate safe practices and make safety a priority in your daily tasks. Your actions will encourage others to follow suit.
Encourage open communication: Create an environment where everyone feels comfortable discussing safety concerns. Encourage team members to share their thoughts and ideas on how to improve safety on-site.
Regular safety meetings: Schedule regular safety meetings to discuss any potential hazards, recent incidents, and preventive measures. Use these meetings as a platform to reinforce the importance of communication and teamwork.
Encourage reporting: Make it easy and non-intimidating for workers to report safety issues or concerns. Let them know their input is valued and will be acted upon.
Collaborate on solutions: Involve workers and contractors in finding solutions to safety challenges. By working together, you can come up with practical and effective ways to improve safety on-site.
Set clear expectations: Clearly communicate safety expectations and procedures to all workers and contractors. Ensure everyone knows their role in maintaining a safe work environment.
Evaluate and improve: Continuously assess your safety communication practices. Identify areas where communication might be lacking and take steps to strengthen it.
When we all understand the biggest causes of work-related harm, we can work together to create a future where every worker in New Zealand has a safe and healthy place to work.
For more information, you can check out our Fostering a Culture of Safety blog or download our Simple Guide to Toolbox Meetings.
The Ministry of Business, Innovation and Employment (MBIE) wants to hear about your experiences with the work health and safety system – how you think it’s working now, what you think works well, and what you think should change. We will be submitting our feedback and we encourage you to share your experiences too! https://www.mbie.govt.nz/have-your-say/work-health-and-safety
Whether you’re carrying out extensions, renovations, flood remedial work, large landscaping jobs, or you are engaging contractors or have the clients living/working on-site, HazardCo can help.
First, you will need to think about how you will manage health and safety on-site and how you will communicate this with other people involved, such as the homeowner, or other contractors on-site. This will make sure that everyone is on top of the site hazards and practicing good health and safety during your project.
A HazardCo Project contains site-specific resources for that job, including:
You can also open up the App for all your contractors when they are on-site by upgrading to Project Plus – talk to the team for more information.
If you meet any of the following requirements a Project could be needed.
The Team Pack Plus is designed for those who move regularly from job to job and are not usually managing larger projects. These are great for managing client inductions and safety procedures while on the go. Our Team Pack includes:
We recommend that you use the HazardCo App and Hub to manage your on-site health and safety. At the beginning of each day, complete a Risk Assessment on the HazardCo App. This will help identify that the work area is safe and make sure that you have the correct controls in place. Due to the nature of renovation work it is important that you consider noise and dust (examples; asbestos, silica and wood) and how you control these risks. A Task Analysis (TA) should be completed for all high-risk work. You can find out more information on completing Task Analyses by clicking here.
At the end of each day, make sure that you tidy up the work area and make sure that everything is made safe. If the work area cannot be entered after hours due to work or health and safety risks then this should be clearly communicated to your client. We recommend that this is also documented to them via an email or text message so you have evidence that this has been communicated.
Remember to use the HazardCo App to report any incidents on your site and the task function to report hazards.
Also, remember to record your Toolbox Meetings with your team. We recommend that you complete at least 2 Toolbox Meetings per site, per month. This demonstrates good consultation and communication with your team.
If you have any questions about your renovation work, give our friendly HazardCo Team a call. As part of your membership, you have 24/7 incident support and advisory support during business hours via 0800 555 339, so don’t be shy – get in touch with us and we’ll help you make your site a safer one
It’s important for young people starting out in construction to understand how to stay safe at work. Young workers lack experience and might not know about all the hazards yet, which could put them in danger of getting hurt. Sometimes young people might feel like they have to impress others, or they might think they’re better at the job than they actually are, they may also forget about safety rules or be afraid to speak up if something seems unsafe. Because of this young workers have additional needs and should be supervised when working on-site.
Positive safety culture onsite comes from the top down, supervisors should be actively modeling and training young workers about safety rules, make sure they have the right gear, and encourage them to speak up if they see any problems.
There are some jobs that young workers shouldn’t do because they might not have enough experience or strength yet. Supervisors need to make sure young people can handle their tasks and keep an eye on them until they are sure they are able to do the work safely. Young workers also need to think about their own safety, listen to instructions and follow safety rules.
When everyone works together to stay safe, it helps make sure everyone goes home safely at the end of the day.
Now, let’s delve deeper into some specific measures that can be taken to ensure the safety and well-being of young workers in the construction industry:
Employing young workers in the construction industry has benefits for the young person, the company and for the industry as a whole as the next generation of builders learn and grow into future roles. By prioritising safety and investing in the well-being of young workers, employers can create a culture of safety that benefits everyone involved. Together, we can build a safer and more secure future for the next generation of construction workers.
If you have any questions, get in touch with the HazardCo team today
Exposure to silica dust has been spotlighted as one of the major risks to workers in the construction industry. According to 1 NEWS, more than 100 enforcement actions have been taken against Kiwi businesses since alarms were raised in Australia, where there have been several deaths from silica dust.
Great question! Silica dust (crystalline silica) is found in some stone, rock, sand, gravel, and clay. You’ll mostly come across it in the following products:
When these materials are worked on, a fine dust is released known as respirable crystalline silica or silica dust. And it’s this dust that is harmful when inhaled into your lungs.
You may be exposed to silica dust if your work involves:
Yes, and they can be serious if the right precautions aren’t taken. Silica dust is 100 times smaller than a grain of sand, you can be breathing it in without even knowing it.
Workers may develop a series of lung diseases from breathing in silica dust, including silicosis, lung cancer, and chronic obstructive pulmonary disease. There is also some evidence that exposure to the dust may cause kidney disease.
To follow health and safety laws, businesses should eliminate or minimise exposure to hazards by controlling the risks. For silica dust, this can be done in many ways:
Isolate work areas: Use physical barriers or computer numerical control (CNC) machines.
Look for dust control features: When buying equipment ensure dust-generating equipment has a dust collection system with a filtered air supply.
Use a H-class vacuum cleaner: Workers should not be using household vacuums to remove dust.
Set up exclusion zones: Mark the boundaries of work areas where dust is created. The signs should warn workers and specify the PPE to be used.
Personal Protective Equipment (PPE): PPE should not be the first or only control measure you consider but should be used. Seek expert advice when choosing it and consult with the worker who will be using it.
On-tool extraction: Use Local Exhaust Ventilation (LEV) that fits directly onto the hand-held machines. This is one of the most effective ways of controlling dust.
Water suppression: To be used when LEV is not suitable. Water should be used through non-electric tools to wet dust down at the point of dust generation. Also, make sure equipment and work areas are cleaned regularly with water.
Respiratory (breathing) protection: The type of respirator you choose will depend on the job and the levels of toxicity. Always choose a respirator that fully protects the worker and carry out fit testing so it is sealed tightly against the face.
Exposure and health monitoring: Provide health monitoring for all your workers who may be exposed to silica dust. You can engage with an occupational health practitioner at Habit Health – HazardCo customers even get a special discount.
Training: Health and safety starts with educating your workers. Provide them with information, training, and instruction on the control measures and the potential health impacts.
Remember employers are required to ensure the health and safety of their workers and others at their workplace, and have a duty to control the risks associated with the job.
At HazardCo, we’re all about education and equipping workers with the knowledge they need to get home safe at the end of the day. Educating everyone on-site about the danger and what we can do to reduce them creates a healthier worksite for everyone.
If you have any questions or want to know more about how to protect your team, get in touch today.
Lithium batteries are common in everyday life and on the worksite, their lightweight, long life, interchangeability and quick charge benefits mean that they are now used in everything from laptops to power tools to EVs. But did you know that they pose a significant risk and need to be a part of your health and safety plan?
Lithium batteries of all sizes have the potential to overheat and catch fire. The fire is hotter, harder to put out and the smoke from these fires is incredibly toxic. Lithium batteries generally overheat if they get wet, damaged or are used with incorrect charging equipment.
Damaged batteries can explode at any time giving off flames that burn anywhere between 500 and 1000 degrees celsius. These fires are very difficult to extinguish as both water and CO2 will only suppress the fire, not extinguish it. Even if the fire has been suppressed it can still ignite again if the battery still contains energy to burn. Lithium batteries are also prone to thermal runaway, which is where one small fault can spread quickly through the battery causing a rapid increase in temperature and potential explosion.
Because of this, lithium batteries need to be properly cared for according to the manufacturer’s instructions to minimise the risk, aside from that, you need a plan in place in case of a fire.
Hot tip: The bigger the battery the bigger the risk of fire and explosion because of the increase in stored energy being released, think energy in = energy out almost instantly so take extra care with larger battery packs – like the ones in your hand held power tools.
Never dispose of Lithium batteries in general rubbish as it can result in a fire in your bin or on the way to a transfer station, creating a risk to those transporting them. The manufacturer should be able to advise safe disposal or check out your local battery recycling centre.
Lithium batteries are going to continue playing a crucial role in our workplaces and lifestyles, so it’s necessary to recognize the potential hazards associated with them. By having awareness of these risks and good practices, we can work together to reduce the potential dangers, resulting in safer working environments where Lithium batteries are used.
If you have any questions, give the Hazardco team a call today!
Making sure your scaffolding is safe and ready for action is key. Here are the times you’ve got to give it a good once over:
All scaffolds must be checked by a competent person before handover and scaffolds taller than 5m must be erected and inspected by someone who holds the appropriate Certificate of Competence (COC). Handover checks involve tagging the scaffolding. No matter the height, all scaffolding must have a tag clearly displaying important safety information at access points. The tag should include the following:
If there’s no tag, do not use it! Get in touch with your scaffold installer to sort it out and get it tagged.
Before starting each day, a pre-start check should be done. This can be done by a competent scaffold user using the HazardCo scaffolding pre-start checklist available from the Hazardco HUB.
Every week a certified scaffolder (if over 5m) or competent person (under 5m) should be checking the scaffolding to make sure it is safe. If the inspector has found any damages or non-compliant areas of the scaffold, then the access ladders need to be removed and the tag updated stating the scaffold is not compliant and should not be used.
A thorough inspection of your scaffolding should also be conducted after any tweaks, fixes, or wild weather. And don’t forget to keep records of all these inspections.
If you have any questions get in touch with the team at HazardCo or have a look at our other working at heights blog here
Proper management of hazardous substances on-site is important to keep everyone and our environment safe. Legally speaking, hazardous substances refer to substances which have any of the following properties:
If you are using any hazardous substance in the workplace you need to make sure they are stored, used, transported and disposed of correctly, which will help to reduce the risk to anyone who uses or comes into contact with them.
To capture what hazardous substances you are using you must by law have a hazardous substance register along with the relevant safety data sheet (SDS).
This is a list of all your hazardous substances (including hazardous waste) that is used, handled, or stored at any of your sites. Having a register will ensure you know the substances you have on-site, the safety measures you need to follow, and what to do in case of an emergency.
Keeping your register in a central location on your site means that in case of an emergency, it can be accessed quickly by anyone who needs it.
Here are some key bits of information that need to be included on your register:
Not only do you need the information above, but you must also make sure that the register is up to date and available on-site.
As the register represents the maximum amount of the substance held, it means it’s not going to be a daily task to keep it up-to-date. But if the maximum quantity changes, the register needs to reflect this. We recommend that you review your register each time you make a change to ensure it’s up to date and accurate.
Creating your hazardous substance register is made much simpler with our Hazardous Substances Register, HazardCo members can access this via the HazardCo Hub in the templates section.
The purpose of a safety data sheet (SDS) is to provide key information about hazardous substances to the people who handle, use or store them or who could be exposed to them.
An SDS tells you
Remember it is the business owner’s responsibility to have an up to date SDS for each hazardous substance and make sure that their workers have access to it. The SDS must be less than 5 years old.
If you need a hand getting started with your hazardous substances register or would like more information, get in touch with the friendly HazardCo team today – we’re always happy to help.
When it comes to construction sites, ensuring the health & safety and wellbeing of everyone on-site is the top priority. It’s more than just wearing hard hats and high-vis vests. It involves careful planning and preparation of the specific needs, hazards and risks of each project. That’s where Site-Specific Safety Plans (SSSPs) come into play.
A SSSP is a detailed roadmap designed to ensure everyone stays safe from start to finish. It identifies the hazards, how you will minimise the risks, sets clear guidelines, and helps to create a culture of safety on-site.
Setting up health and safety with HazardCo Projects is quick and simple. All you need to do is log in to the HazardCo Hub and “create a Project”. You receive the completed SSSP straight away while the physical scan-in board will be sent out for you to display on-site.
Not only does HazardCo’s Project save you time at the start of your project, it saves time for everyone on the site. Once the project starts, everyone entering the site inducts themselves on-site using the QR code on the site scan-in board, and the QR scanner in the free HazardCo App. That’s right, everyone inducts themselves using their smartphone, no lengthy induction meetings or paperwork required, and you get a record of every completed induction too.
Make sure you request a Task Analysis from each of your contractors so you can include their Hazards and controls in your SSSP. This will help ensure you and others on site are well informed of all the hazards from start to end of the project.
Share the SSSP with the team. Anyone scanning into the site using your QR code and the HazardCo App will have immediate access. Every worker who sets foot on-site needs to know and understand the SSSP. This can be done during the site induction, where the workers learn about the project, potential hazards, and safety protocols, which they can do using the App. If you need more information on working with contractors you can check out this blog.
While there’s no one-size-fits-all approach to creating a SSSP, using digital tools like HazardCo can offer great time saving and streamlining benefits. Among many other benefits of using HazardCo, using it for SSSP means that you have:
Going digital with the HazardCo App means information flows more efficiently and this allows your teams to better collaborate with one another.
So, whether you’re building a multi residential, a new build or doing a big reno, remember: safety first, always. And with a solid SSSP in place, you’re one step closer to a successful and safe construction project.
For health and safety sorted in a flash, right from the very start of your new build, look no further than HazardCo Projects. It’s the smart way to maintain a safe site and have more time to focus on the job at hand.
If you would like to discuss your upcoming project please give our team a call on 0800 555 339.