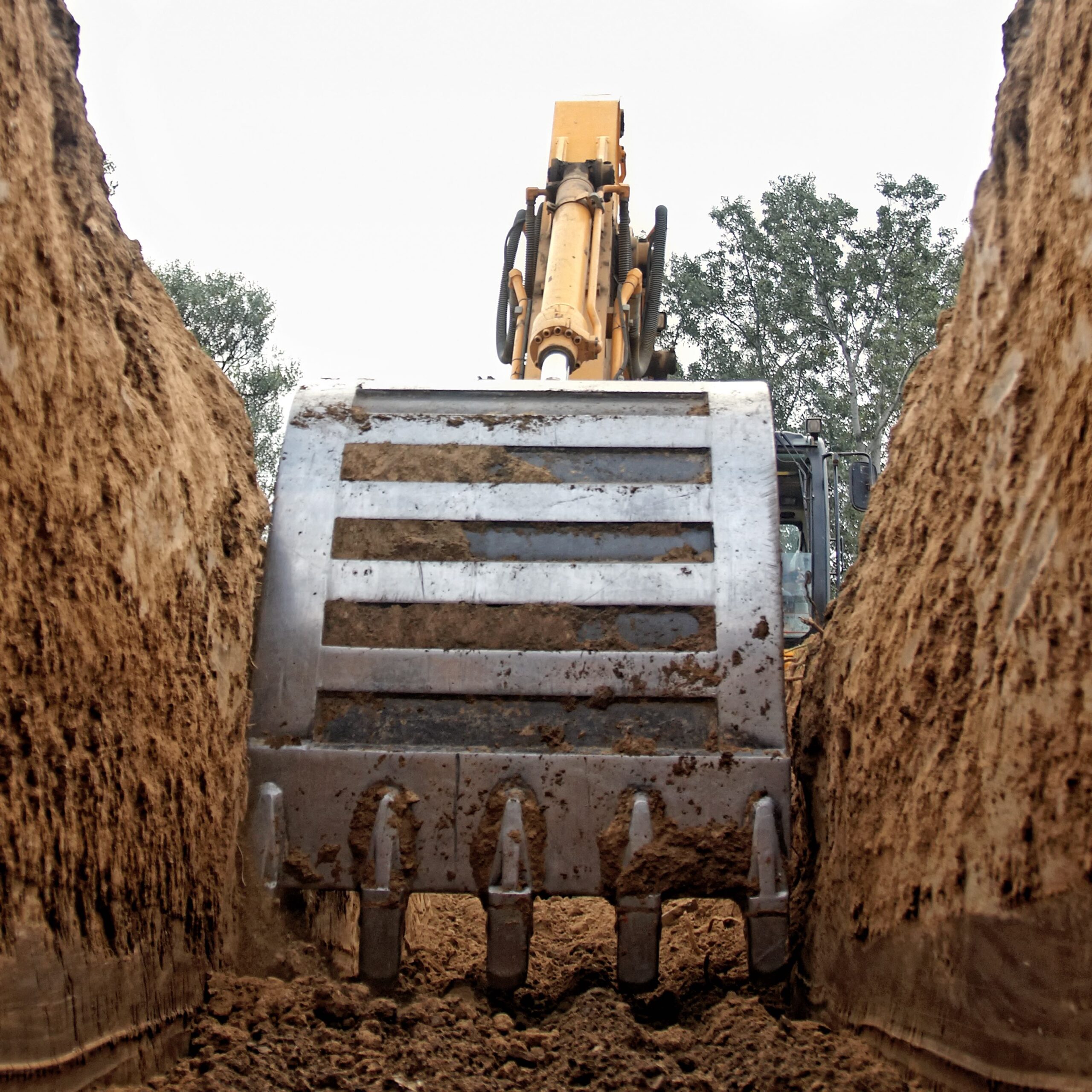
We have previously shared content on what to expect when your workplace is inspected by WorkSafe/SafeWork. Now – what happens in the event that your business has received a Regulator’s Notice from WorkSafe?
If the inspector does find an issue, you and the inspector will discuss what needs to be done to fix it. The three main outcomes issued by the inspector are an improvement notice, a prohibition notice or an infringement notice.
We’ve put together our top recommendations on what you can do after receiving a regulator notice.
Carefully read the notice and follow all the instructions listed in the notice. This is particularly crucial if it’s a prohibition notice, as it means certain work must be stopped immediately. Work is not to continue until the Inspector is satisfied certain action has been taken to make the activity/area safe.
Make sure the site entry report and associated notice/s are provided to the Director/ Owner of the Business. We also recommend sharing the notice with other project sites /areas of the business so that they can assess their area to see if similar issues are present or where there is room for improvement. This is a great way to improve health and safety across all areas and sites of the business and to demonstrate Health and Safety is a top priority for all.
Bring the notice to the attention of all persons whose work is affected by the notice (e.g. conduct a toolbox talk and record it in the HazardCo app). Discuss how the business will address the items and by when. We recommend you provide regular updates to the workers on this matter. If you have any Health and Safety Representative (HSRs) who represents workers whose work is affected by the notice, make sure a copy is provided to them.
Make sure a copy of the notice is put up and displayed in a prominent place at or near the part of the workplace where the affected work is being performed (and we recommend you communicate to workers where this can be located).
Promptly discuss with relevant suitable persons who will be involved in addressing the notice (e.g. conduct a meeting with management, supervisors etc) and prepare an action plan to address all items that have been highlighted in the notice. Regularly track action items for timely closeout.
Ensure you document and record discussions, meetings, and agreed actions. Record and track health and safety actions by creating and assigning tasks on the HazardCo Hub or on the App.
Collate all the evidence requested by the notice that will demonstrate you have addressed all the items listed and provide it to the Inspector prior to the due date for their review.
Remember HazardCo is here to help. Give us a call on 0800 555 339 and speak to our Health and Safety Advisory support team for further guidance.
Common incidents on-site: The more often you are exposed to a risk, the less your brain perceives the significance of the risk. The level of risk has not changed. Remember how your first time on a busy worksite felt, all those things going on around you. That level of danger is still there. As you have become constantly exposed to it your mind starts to ignore things it thinks are no longer relevant so you have to consciously pay attention to the ever-changing worksite environment. This is how many of the common injuries happen, the brain switches off and you go into ‘autopilot’.
Hit body on object – corrective actions and recommendations
Manual handling – corrective actions and recommendations
Staple/nail gun – corrective actions and recommendations
Hand Tools – corrective actions and recommendations
Slip/Trips – corrective actions and recommendations
Of course, reach out to HazardCo and speak to one of our expert Health and Safety Advisors if you have any questions or need more support on ways to combat common incidents on-site. You can contact us on 0800 555 339.
Timber frame standing and truss erection can be back-breaking work! It is often high risk work with some serious potential injuries. We recommend these three steps are completed prior to every install. And ensure that everyone understands the process and their role, from when frames and trusses arrive on-site all the way through to standing.
Here are 3 recommendations to ensure that your site is safer during the arrival and installation of frames and trusses:
The development of Risk Assessments and Task Analysis are crucial to your workers to ensure their safety throughout the build. To make these processes easy, you can complete these on the HazardCo App.
Some things to think about when creating a Risk Assessment for frame and truss delivery and erection are:
Is the work area secure?
Clients, visitors, and members of the public cannot enter the area and workers are aware that they should only enter if they are required for the tasks.
Have all site inductions been carried out and an emergency plan developed for any at height work?
Have all workers who work at height been trained to do so? Is access to height suitable and is fall protection in place?
Have all workers been provided with the correct PPE? Are all tools and equipment available and in suitable working order for the task?
The purpose of a Task Analysis is to go into detail for each of the tasks to be carried out. Thinking about the hazards at each step and how they can be appropriately controlled.
You should think about:
The results from the Risk Assessment, Task Analysis, and control measures should be discussed with all workers prior to work starting.
On paper, this sounds like a lot of work – but it is made simple by using the HazardCo App, and creating Task Analysis templates that you can save as templates and amend again and again. You’re not having to start from the beginning for tasks that you complete regularly. Do remember to check over your templates before approving them as different sites can present different hazards that you don’t want to miss (overhead power lines as an example).
When working at height, either on a second story or setting trusses you need to ensure that your workers are safe, not just from falling, but from tools, equipment, or product falling too.
Scaffolding
Once the lower level frames have been stood/braced appropriately, safe working platforms should be installed such as scaffolding. Scaffolding over 5m should be erected by a trained and competent person and all scaffolding should be checked by a competent person regularly.
Edge protection
If the potential of a fall cannot be eliminated when working on a roof, some form of edge protection should be used to isolate workers from a fall. This includes working on single-story buildings and structures. Using the existing scaffolding as edge protection is often the simplest solution. If this is not practicable, then elevating work platforms or temporary work platforms should be used. Toe boards should be fixed to temporary edge protection as a way of containing all materials, including debris and loose tools.
Safety netting
Safety netting can be installed to protect workers, tools, and equipment from falling.
Only safety netting that has been installed correctly can be relied on to support the weight of a worker so that it can resist the force of a person falling onto it. Tests for UV deterioration of safety nets must be done at least every 12 months and a current test label must be displayed on all safety nets older than 12 months.
Worksite traffic can be a major cause of harm on work sites. When it’s close to having your frames and trusses delivered to site and you’re considering dates with the delivery company, it is essential to communicate the traffic management plan with them. This provides the company and drivers involved with a clear picture of how the site has been structured and can assist the delivery company in selecting the correct sized vehicle for the delivery, taking into account the site size and structure.
Ensuring that you implement the above can prevent many injuries on site, as well as regular toolboxes, making plans for ‘what if’ situations (rescue plans) and discussing these with your workers to keep them alert so they’ll know what to do if an incident occurs on-site. For some useful information on the safe installation of roof trusses please view this resource from WorkSafe
Below you will find guidance on what to do in the event of an attack or site emergency involving an assault or an armed offender, including some practical advice on minimising the chances of an attack on-site.
Check:
Speak Up:
Ensure:
It’s important to be aware of Critical Incident Stress (CIS)
A “critical incident” is an event that can be so emotionally intense that it can be hard to handle using our usual ways of coping. These could include situations like a sudden death, serious injury, or a physical or psychological threat to the safety or well-being of an individual, workplace or community regardless of the type of incident.
Typical symptoms of Critical Incident Stress include:
There are some techniques and professional assistance you can reach out for:
Informal debrief with peers post-event:
This can be done with supervisors, senior team members, or just work colleagues. Try and assess those team members who may need further support. Keep assistance within your training, and reassure colleagues that support is there for them with the provision of support numbers or how to access EAP services if available.
Employee Assistance Program (EAP)
EAP Services provides brief, solution focused support, to help workers deal with any difficulties they may be experiencing and to minimise the impact on their life. Counselling is available via video, over the phone or face to face. It’s important for employers to ensure that they have EAP services organised for their employees before an incident occurs.
Seek professional assistance to help you run a Crisis Management Briefing (CMB)
A Crisis Management Briefing (CMB) is one of the most highly utilised and versatile crisis intervention techniques. A CMB is a structured group meeting designed to provide information about the event.
Critical Incident Peer Support Groups use CMB’s as a way to share education about typical stress reactions and to provide information about basic stress management and coping techniques and resources.
Seek professional assistance and run a Critical Incident Stress Debriefing (CISD)
Following trauma exposure, an individual can experience multiple emotional, mental, and physical symptoms that impact their well-being. CISD is a practice that allows survivors to process and reflect on the traumatic events they’ve experienced and gain personal control over the incident.
Helplines that could be useful:
Reinforcing steel can be used in many ways on a building site. Terms commonly used are rebars or waratahs. They are steel bars or mesh wires used to support walls, concrete, or other stone structures.
Workers can fall on the protruding bars which can result in deep lacerations or even life-threatening injuries, so it’s important that preventive measures are in place to reduce the risks.
Some of the hazards include;
Safety Caps
Safety caps are made of plastic so they are a cost-effective way of covering the protruding steel rods. Even though they are small, the safety caps effectively protect against injuries and potential impalement.
Their bright fluorescent colour increases visibility which lessens the chance of the worker walking into, or tripping over them by accident. They are also cost effective, quick and easy to install.
Control access
In addition to using safety caps, access should be restricted to areas where there are protruding ends.
Injuries can happen when workers are not paying attention to the hazards around them, so ensure that your workers are aware of their surroundings, or physically prevent them from entering the area altogether by using barricades or tape to control access to those areas with hazards.
Keep a clean and tidy site
Ensure that you have a clean and tidy worksite. Gather and remove debris to keep the site free from scraps, and potential trip hazards.
Reinforcing steel scraps lying unattended can rust and pose a safety risk for workers, therefore, make sure you arrange prompt and proper disposal of the scrap materials.
PPE
PPE for people working with reinforcing steel may include;
Best Practices
Construction can be dangerous. There are hazards in all worksites, which can result in life-threatening injuries. Carry out regular site reviews using the HazardCo App to ensure that hazards presented by reinforced steel are correctly controlled.
Of course, reach out to HazardCo and speak to one of our Health and Safety experts if you have any questions or need more support on avoiding reinforcing steel hazards.
Asbestos related diseases is New Zealand’s number one work-related killer. Approximately 220 people die each year from preventable asbestos-related disease.
We’d like to give you some basic information on the dangers of asbestos, where it can be found and what you can do to avoid it.
There are two types of asbestos:
Inhaling asbestos fibres can cause a range of irreversible damage and diseases.
One of the most common asbestos related diseases is asbestosis. This causes severe scarring of the inner lung tissue. People usually have pain and severe difficulty breathing. Although this isn’t directly fatal in itself, it can lead to respiratory or heart failure.
Damage from asbestos may occur in as little as five years, or take as long as 40-50 years after exposure for symptoms to appear. Unfortunately, many people do not realise they have been exposed until it’s too late.
It is vital you don’t attempt to remove asbestos yourself, unless you are trained, certified where required, and fully competent – we cannot stress the importance of this enough!
If you’re planning to renovate or partially demolish a building, have a survey done first to identify if Asbestos Containing Material is present. If it is, contact your local asbestos removalist.
Any building constructed up until the year 2000 has a high probability of containing asbestos. View the posters created by WorkSafe on locations where Asbestos can be found on industrial and residential buildings. It is useful to familierise yourself and your workers with the areas relevant to your work. If it is not expected that asbestos would be present and you see unidentified asbestos while working, stop work immediately and arrange for an assessment of the Asbestos Containing Material (ACM) to be carried out.
Yes, there is. Disposal must meet strict guidelines. Bagging and wrapping asbestos pieces is essential in any sort of removal – and dumping asbestos-containing materials can only be done in authorised locations. It is important to check with your local council for specific disposal locations and requirements. Wherever possible, leave this to the asbestos specialists.
Removal of ACM greater than 10m² can only be performed by a licensed removalist. Clearance certificates are documented records of the removal and correct disposal. Keep these records on-hand with the other site documentation.
Recognition means everything when it comes to asbestos, signage on-site, equipping your team with knowledge of asbestos dangers, using the HazardCo App to assess risks, and educating your workers could be the difference between life and death.
For additional education and training on Asbestos we have partnered with two training providers, Safety N Action and BeSafe which both provide Asbestos courses. Check out your HazardCo’s Perks and Partners page for further information. There is a course available for whatever your asbestos needs.
What’s more, as a HazardCo customer with a current membership, you’ll get a 10% discount on any courses you undertake through these partners. Just advise them you are a HazardCo customer upon booking.
Remember to also undertake health monitoring for any workers who work with airborne contaminants (such as asbestos or silica dust). See Habit Health a national health monitoring provider – and again, as a HazardCo customer you receive a 10% discount on any services engaged.
HazardCo’s Advisory Team can help with any asbestos questions or other health and safety matters – give us a call on 0800 555 339.
Risks change, all day, everyday. That’s the reality of life on site. Managing risk needs to be apart of life onsite.
Methods change because of different training and experience, people on the job change, there are differences in machinery and materials used, as well as environmental changes from hour to hour.
It’s a lot.
Risk is a product of the work processes being carried out. So, if the work doesn’t happen, the risk isn’t present.
But, if a work process is defined then risk can be recognised and taken into account.
The key question tradies and supervisors need to be asking themselves is:
How do I adapt my task when a change occurs?
It’s not about mountains of paperwork. It’s about 4 simple steps:
A change occurs. Repeat.
Plan. Do. Check. Act.
Repeat.
(You get the picture)
We should all be working towards a heightened sense of awareness on site. And of course, treating risks as priority should be a collective mindset. Reinforced by supervisors who should be adapting plans and guiding teams to take account of the constantly evolving risk environment.
The power of change in risk can kill, the power of change in process can save a life.
Be the change you want to see.
If you have any questions please reach out to the Hazardco team today
The construction industry is known for its potential hazards and risks, and unfortunately, incidents sometimes occur. Having an incident on-site can be alarming, but your response is crucial in reducing its impact and making sure the team is safer in the future.
Remember, if you’re a HazardCo member we will support you throughout this process, just give us a call.
Incidents can range from very minor, to serious incidents. The steps below can be scaled up or down depending on the seriousness of the incident. If you have a near miss on-site, this is also considered an incident. Learn more about reporting near misses.
The health and safety of the people involved in the incident should be the main concern. Immediately assess the situation to identify any ongoing dangers and take appropriate action to eliminate or minimise risks. Evacuate affected areas if necessary and provide medical assistance to injured personnel. Remember, health and safety should always come before anything else.
Once the immediate safety concerns are addressed, you may need to secure the scene to prevent further incidents or unauthorised access. Erect physical barriers, post warning signs and restrict entry if needed.
Maintaining clear and effective communication during and after an incident is really important.
Notify all the relevant people about the incident as soon as possible. This includes workers, supervisors, managers and contractors.
Using the Report Incident feature on your HazardCo App, fill out the fields to capture what happened. Your reported incident will be added to your incident register in the Hub, and HazardCo retains this for as long as you’re a member.
It’s important to note that some incidents are required to be notified to WorkSafe. These are referred to as notifiable incidents. A notifiable incident is:
In the event of a notifiable incident, you need to preserve the incident site until a WorkSafe inspector arrives or WorkSafe directs you otherwise. This doesn’t prevent you from helping an injured person or making the site safe.
For more information on what to do when it comes to notifiable incidents, head over to the WorkSafe website.
Investigating will help to find out exactly what happened and why. We recommend talking to the people involved as well as any witnesses. For a serious incident, it’s best to speak to everyone individually.
Document all your findings in a report, including photos and relevant data. In the report, you should look at immediate causes as well as bigger issues and potential improvements to prevent future incidents. HazardCo members can use the guided Investigation Report in the Hub to identify any shortcomings or gaps that may have contributed to the incident and implement corrective actions. This may involve improving training programs, modifying procedures, upgrading equipment, or implementing new safety technologies.
Pass on what you have learned to everyone involved. This is your opportunity to emphasise a culture of continuous improvement and learning to prevent similar incidents in the future.
Encourage open communication and create a supportive environment that encourages workers to report near misses and potential hazards without fear of repercussions.
When an incident occurs on a construction site, a swift and effective response is crucial to reduce risks and ensure the health and safety of your crew. Prioritising safety, establishing clear communication channels, securing the scene, communicating and investigating the incident can continuously improve the health and safety of everyone on-site. At the end of the day, these measures protect lives, as well as contribute to the long-term success of the project and your business.
While many industries seem to have recovered post-pandemic, the construction sector is still battling tough conditions.
It’s important to keep on top of your business processes to reduce headaches later down the track. Whether it’s your invoicing, your insurance, or your health and safety, neglecting these things can really hurt later on. Some businesses are choosing to take this time to invest in their current systems and processes, to help them to build a more resilient business that can respond to the market.
If your business has scaled back a bit, such as cutting back on help, switching to smaller renovation projects, or you plan to really tighten the belt on the budget for a while, we’re here to remind you to prioritise your H&S. As long as you or your team are on the tools, you need to manage health and safety effectively. This means:
The HazardCo system helps you to manage your health and safety in the simplest way possible, so you’ll feel confident you are keeping your team and your business safe. The system is designed especially for home builders, and comes with all the reports and templates you need, loaded up with advice provided by experts
Key benefits include:
Health and safety should never take a back seat. It’s still as crucial as it’s ever been and HazardCo’s here to keep you out of strife.
Get a free 7-day trial of the HazardCo health and safety system.
Nail guns are used frequently on construction jobs, including in residential construction. Like all power tools, nail guns can cause serious injury. Nail gun injuries can happen due to accidental discharges whilst moving, carrying, and repositioning. Injury can also happen when fired nails strike other nails or timber knots causing them to ricochet. Incidents also occur when workers accidentally place themselves into positions where they are directly exposed to the projectile path of a nail gun.
The risk of a nail gun injury is greatly increased when using a contact trigger (bump fire or multishot) compared to using a full sequential trigger (single-shot). Most injuries occur when the nail gun is set to ‘bump fire’ mode, resulting in penetrating wounds to the operator or nearby workers.
It’s important you review the type of nail gun trigger system and the extent of information, instruction and training given to workers, particularly inexperienced and young workers.
There are a number of ways to reduce the risk of injuries. We have put together a few suggestions below and we encourage you to consult with your workers about how you can work together to ensure safe nail gun use on-site:
Note: Bump-fire nail guns potentially may be used to reduce the risk of musculoskeletal injuries (e.g. strains and sprains) for jobs that involve high volume production and repetitive tasks. In these circumstances, ensure only highly experienced and skilled workers use these types of nail guns and implement other additional control measures to reduce the risk of injury.
If you have any questions please reach out to the HazardCo Team