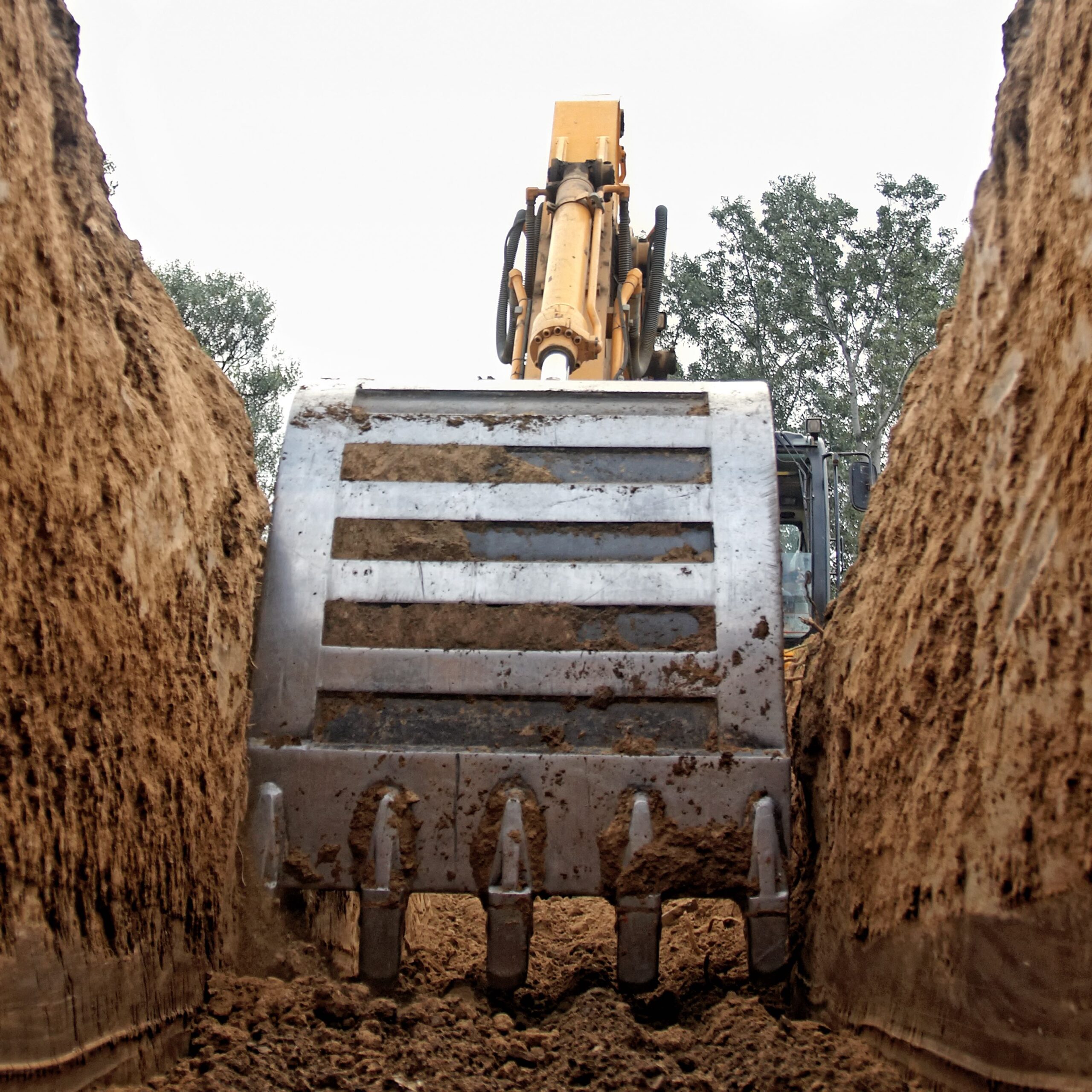
Businesses (PCBUs) that work together will often share health and safety duties in relation to work done. Businesses especially have a legal duty to consult, cooperate with, and coordinate activities with all other businesses they share overlapping duties with.
What does this mean and how can you ensure that people are not harmed, and you are complying with your legal obligations? Here are some expectations:
The following key steps should be followed by Main Contractor:
Scope
Prequalify
Select
Appoint
Monitor
Review
Working along other businesses is a natural part of residential construction. Everyone on-site has a duty to open up the lines of communication and look out for each other.
You can read more about contractor management and overlapping duties here or if you have any questions about working with other businesses on-site, give our expert Advisory Team a call on 0800 555 339.
Even if you are self-employed you still carry the same duties under the legislation as the main contractor.
If a contractor, in turn, engages other businesses then they too must assume some of the responsibility for their work. A contractor is most likely to have the greatest influence and control of their own work activities and workers (or contractors).
There should be a way of recording your planning and the ways in which you share this information. All businesses should have access to information to keep themselves or their workers safe.
Your primary duty remains to prevent harm arising from your work. Identify risks that could arise and share information between relevant parties.
The following key steps should be followed by contractors:
Scope
Prequalify
Select
Appoint
Monitor
Review
Working along other businesses is a natural part of residential construction. Everyone on-site has a duty to open up the lines of communication and look out for each other.
You can read more about contractor management and overlapping duties here or if you have any questions about working with other businesses on-site, give our expert Advisory Team a call on 0800 555 339.
Health and safety issues arise from a worker raising concern about health and safety at the workplace and that concern remains unresolved after consultation with the worker/s and the PCBU (Employer), it then becomes a health and safety issue.
For example, an issue could include a difference in opinion on whether something is a potential risk to health and safety, or whether a particular control measure is acceptable.
There are issue resolution requirements in Health and Safety legislation that outlines how a health and safety issue should be resolved, with the aim to agree on how to fix the problem, as soon as possible, to avoid further dispute or a similar future issue. If after reasonable efforts the issue cannot be resolved, then it can be referred to the regulator (WorkSafe) by completing the ‘Request Assistance to Resolve a Work Health and Safety Matter’ form available on their website.
The following details need to be taken into account when assessing the severity (risk level) of the issue, and from there deciding who needs to be involved:
An agreed H&S Issue Resolution Procedure is a process or steps for resolving health and safety issues in the workplace which has been agreed upon by directors / management / workers.
You can establish an agreed procedure for a workplace. To do this, make sure the procedure contains:
It is recommended to have a procedure in place in the event of an issue arising, or the steps provided in legislation can be followed.
Once the relevant people have been made aware of the details of the issue and the level of risk has been assessed, health and safety regulations set out the default procedure for resolving it.
Multiple people can be involved in the issue resolution process, depending on the risk of the issue, to ensure adequate consultation and the best outcome occurs. This means it could be:
If you or your worker would like to involve representatives in the issue resolution process you are able to do so. A representative does not necessarily need to have health and safety expertise. This could include people such as a designer of a piece of equipment at the workplace, or a person with workplace consultation and negotiation skills. Depending on the nature of the H&S issue, advice or assistance from a range of experts may be required to reach an appropriate and informed resolution between the involved parties.
Things to remember:
When the issue has been resolved, details of the issue and the resolution should be set out in a written agreement. If a written agreement is prepared:
If you’ve got a question about Health and Safety issue resolution or any other health and safety matter, the HazardCo Advisory Team is here to help. Give us a call on 0800 555 339.
When you’re able to get back on site after a flood or storm, here are the hazards, risks and control measures you should consider to help reduce the risk of injury and illness to yourself, your workers and others involved in the clean up and repair effort.
If you have any questions as always get in touch with the HazardCo Team
When we hear the term “red flags” it means there’s a problem, it is a warning sign that something isn’t right when it comes to a particular situation. In the way of a construction site, this could be anything from a messy site, to using out of date H&S paperwork.
Some red flags are more visible or obvious than others, however it’s important to eliminate red flags on your site as they can cause injuries and other issues for you and your crew. We’ve covered some of the most common red flags and how to remove these from your site.
Not having a fence around the site perimeter could invite unauthorised entry. If your site isn’t secure, members of the public or children can enter the site, which could lead to injuries, property damage or stolen items.
Easy, ensure your site has adequate fencing set-up around the perimeter to prevent unauthorised entry. Take into consideration the height and ensure it’s not only high enough, but also check that the gap at the bottom isn’t too big where people, including children, could squeeze through underneath.
A messy site can lead to all sorts of problems. Waste and other objects left lying around can create obstacles for you and your crew. The mess could cause slip and trip injuries which can result in workers needing time off work, something you want to avoid!
Make sure your team is regularly cleaning up after themselves. Waste materials like cardboard, general rubbish and other lighter material can be placed/stored in such a way to eliminate tripping hazards and prevent them from flying off site, especially during strong winds.
Having a skip or bins available and ensuring everyone takes a moment to keep the site clear will reduce the risk of injury for everyone.
The site sign provides all of the important details including an after hours contact number.
If something happens on-site and the principal contractor needs to be contacted, it needs to be easy for anyone to find.
Display a Principal Contractor sign in a visible location which includes the following
information:
If there is no process for identifying the hazards, assessing the risks and what controls are required for a task, it could pose a significant risk to workers on-site.
A Task Analysis (TA) is required for all high risk construction work. Ensure a TA is accessible to the workers performing the task and that they are familiar with its contents.
It’s important that a TA is regularly reviewed. If the TA is not being followed due to a variation of work or conditions have changed, then work must stop until the TA is reviewed and updated.
When people are unaware of incidents or near misses occurring on site, it could lead to the same incident unnecessarily injuring people repeatedly. Also, some incidents legally need to be notified to WorkSafe. A fine can be issued if this does not occur.
Reporting injuries is also important when it comes to making sure the worker receives appropriate treatment, (e.g. medical treatment) and other support, (e.g. return to work).
When incidents, near misses, injuries and illnesses occur on-site it’s important they are reported and investigated appropriately. By recording an incident via the HazardCo App, it automatically populates an incident register on your Hub so that all the incidents are recorded in one central location.
Carrying out investigations is important as they look at why the incident occurred and what controls can be implemented to prevent them from occurring again.
H&S paperwork needs to be kept up to date to help keep your workers safe. If yours is out of date, it could contribute to an incident on-site.
Additionally, lack of H&S documentation (e.g. Risk assessment/Task Analysis) could mean you’re not complying with Legislation so you could be liable for certain prosecutions and/or fines.
If you’re old school and don’t mind filling out H&S paperwork by hand, make sure you are using something that is current, e.g. the TA is specific for the high risk task.
If you’re like us and love using a digital system, use the HazardCo App to get your H&S done quickly and simply. All of our features including the TA and site review are regularly reviewed and kept up to date, including when legislation changes.
Summer is here – longer days, sunshine, and the outdoors sound like the perfect conditions to get all that work done. It doesn’t matter what time of year it is, hazards and risks are forever present and summer brings with it its own risks. Have you thought about what you are doing to protect your team from the effects of the summer sun and heat?
“Slip, Slop, Slap and Wrap” to minimise the obvious risks of sunburn or skin cancer, but we also need to be aware of the risk of heat exhaustion, dehydration and fatigue.
Heat exhaustion occurs when our bodies overheat from the loss of water and salt due to sweating. If left untreated it can lead to heat stroke.
Heat stroke occurs when the body is no longer able to keep itself cool causing a high body temperature of 39.4 degrees or more.
Heat rash and heat cramps are earlier stages of the onset of heat exhaustion. Knowing the signs and what to do will help prevent the onset of heat exhaustion or worse, heat stroke.
If you have underlying health issues that could be affected by extreme heat make sure you let your business know.
Planning is key – With the sun at its peak between 10am-4pm, make sure you take regular breaks within this time and where possible arrange work that can be done in covered or shaded areas to be completed during this time period.
Check out this handy resource on how to protect yourself when you’re outside
Take it easy – Don’t overdo things. Keep strenuous tasks to a minimum and regularly rotate work tasks.
Listen to your body – Just because the weather is nice and you can work longer to get those jobs done doesn’t mean that you should. Fatigue affects your mental and physical capabilities making it harder for you to concentrate. When we lack concentration is when incidents can occur.
Discussing the effects of the Sun (UV and Heat) at your Safety/Toolbox meetings is a great way to remind everyone of this often overlooked environmental hazard. You can easily record your Safety/toolbox meetings using the HazardCo App.
If you have any questions or would like to discuss your work hazards give our Advisory team a call on 0800 555 339, option 4.
Most cement, lime, mortar, concrete, and plaster products are hazardous substances that contain strong alkalis.
As seen in the image above, alkalis are on the opposite end of the PH scale from acids, however, can be equally as dangerous, being extremely destructive to your eyes. The way you handle the first seconds, minutes, and hours after you get the dry powder or wet mix in your eyes, will determine the outcome.
Alkalis may start their damaging work in your eye without much pain or symptoms, but over time the damage gets worse. So beware, follow the first aid steps below even if you don’t feel pain.
Don’t become one of the statistics: in 2021, there were 56 burn injury claims to the eyes in the NZ construction sector, with 90% of chemical eye burn injuries that could have been prevented.
Every second counts! Run to the closest tap, eye wash station or water bottle and start flushing your eye. You are aiming to dilute the alkali to lessen the damage.
Wash your face and hands, you don’t want to get more cement product in your eyes. Flush your eye with a steady stream of running water. Let it pour into your eye while lifting both eyelids to rinse out all the cement granules underneath. Do not reuse the water and do not let contaminated water run into the unaffected eye.
If you do not flush your eye, or stop before you are told to do so, you may suffer from permanent eye damage, dry eyes, vision loss and more.
HazardCo’s Site Box or Emergency Box is ideal for storing your SDS files and eye wash stations on-site. You can also upload and store your SDS and other H&S documents on the HazardCo Hub to keep them all in one place.
If you have an incident where someone gets cement/concrete in their eye, remember to report this as an incident in the HazardCo App. This will automatically be added to your incident register in the HazardCo Hub, and the Advisory team will be in touch with you to discuss next steps if it is deemed to be notifiable to WorkSafe NZ.
For questions or support, contact the friendly advisory team at HazardCo at 0800 555 3339 or info@hazardco.com.
The Toolbox Meeting feature on the HazardCo App means you’ll no longer have to carry around paperwork for your meetings. Our app makes it easy for you to keep energy levels high and hold everyone’s attention with short and focused talks. With the HazardCo App running on your smartphone, you can easily move the meeting to the most relevant place on-site. One man band? No worries, you can use the toolbox feature to capture conversations when you talk to other subbies on-site.
On the HazardCo App, the Toolbox Meeting feature guides you through a team chat with an easy to follow guide that helps you cover all the necessary points and capture key details as you go. It means you don’t need to do any special preparation for your toolbox meeting, just make the time, follow the app, and you’ll get a completed report on the Hub at the end which you can download or email to others. Plus, save yourself some time by using your voice to text feature on your phone which comes as part of most Android and iPhone devices, look for the microphone icon on the keyboard pop up. You can also record attendees with a photo.
Using HazardCo Toolbox Meetings gives you another easy way to keep the team involved too – simply get someone different to run the meeting each week. It keeps everyone thinking more about health and safety, and it shares the admin around. And did you know that the Toolbox Meeting feature isn’t just for toolboxes, you can also use it to conduct safety meetings, pre-start meetings, and committee meetings.
Toolbox Meetings are a vital component of keeping your site safe, and with HazardCo in the palm of your hand, you have all the tools you need for great toolbox meetings with your wider crew.
Noise is a very common risk across many different types of worksites. One of the most common sources of loud noise is machinery and equipment.
Machinery and equipment operate at high speeds and generate a great force that can generate significant noise. In certain worksites, this noise can be at increased volumes for long periods of time. Noise poses a risk to workers as it can cause long-term and irreversible damage to their hearing. Once the risk to workers hearing is identified it should be managed by either removing or minimising the risk.
It is recommended to control noise at the source. Some examples of how you can control and reduce noise are:
Hearing protection should only be used when extra protection is needed after using the above noise controls. If hearing protection is required:
Workers should be aware of the risk that exposure to excessive noise has to their hearing. Talk about managing noise during your safety meetings and keep a record of it in the HazardCo App. Make sure workers are provided with the appropriate training in the correct use, maintenance and storage of hearing protection. A Training Register template is available on the HazardCo Hub which can be downloaded and filled out.
You can view these resources below:
Is your work too noisy?
WorkSafe NZ’s Hierarchy of controls for noise video
If you have any questions about noise in the workplace, give HazardCo a call on 0800 555 339.
Using machinery and equipment for work on-site puts workers in close contact with powerful and fast moving tools. This makes getting the job done easier and more efficient but it does also present some risks to workers health and safety. If a worker comes into contact with machinery or equipment in an unsafe way, it can cause significant harm or injury. It is common practice to use guarding on machinery and equipment to create a barrier between the workers and the moving parts that can cause harm or injury.
Machinery and equipment guarding is designed to eliminate or minimise the risk of workers being harmed while completing their work. It is important to assess the hazards and risks involved with all the machinery and equipment used in the workplace. If machinery and equipment is not guarded properly, workers can sustain significant injuries due to coming in contact with moving parts.
Some common injuries are:
Because there is potential for serious harm when using machinery and equipment, it is necessary to plan a safe approach when conducting a job. This will help identify the hazards of working with machinery and equipment.
The hazard management process includes:
There are many different types of guards that can be used to protect workers from being harmed when using machinery and equipment. Here are some common types of guarding and examples of when they are used:
When choosing a guard, It is important to make sure the guard can actually prevent an operator from reaching into the dangerous parts of machinery and equipment. To make sure the operators are protected from the dangerous parts, the safest guarding must take into account an operator’s ability to reach into or come in contact with moving parts.
There are many different types of guards to choose from. It is important to choose guards that eliminate the potential for harm. If this is not possible, then guards should be chosen that isolate or minimise the risk to workers. It is very important that guarding is not removed or tampered with as this will increase the risk of harm to workers.
Control hierarchy:
Workers should be trained to competently complete the work they are required to do. Workers should be trained and educated on the purpose and function of the different types of guarding in the workplace. Make sure that workers have the appropriate training, supervision, and qualification (if required) to safely use the necessary machinery and equipment. Keep an up-to-date register of what machinery and equipment workers are trained on and competent in using. A Training Register template is available on the HazardCo Hub which can be downloaded and filled out.
If you have any questions about guarding machinery and equipment, give HazardCo a call on 0800 555 339.