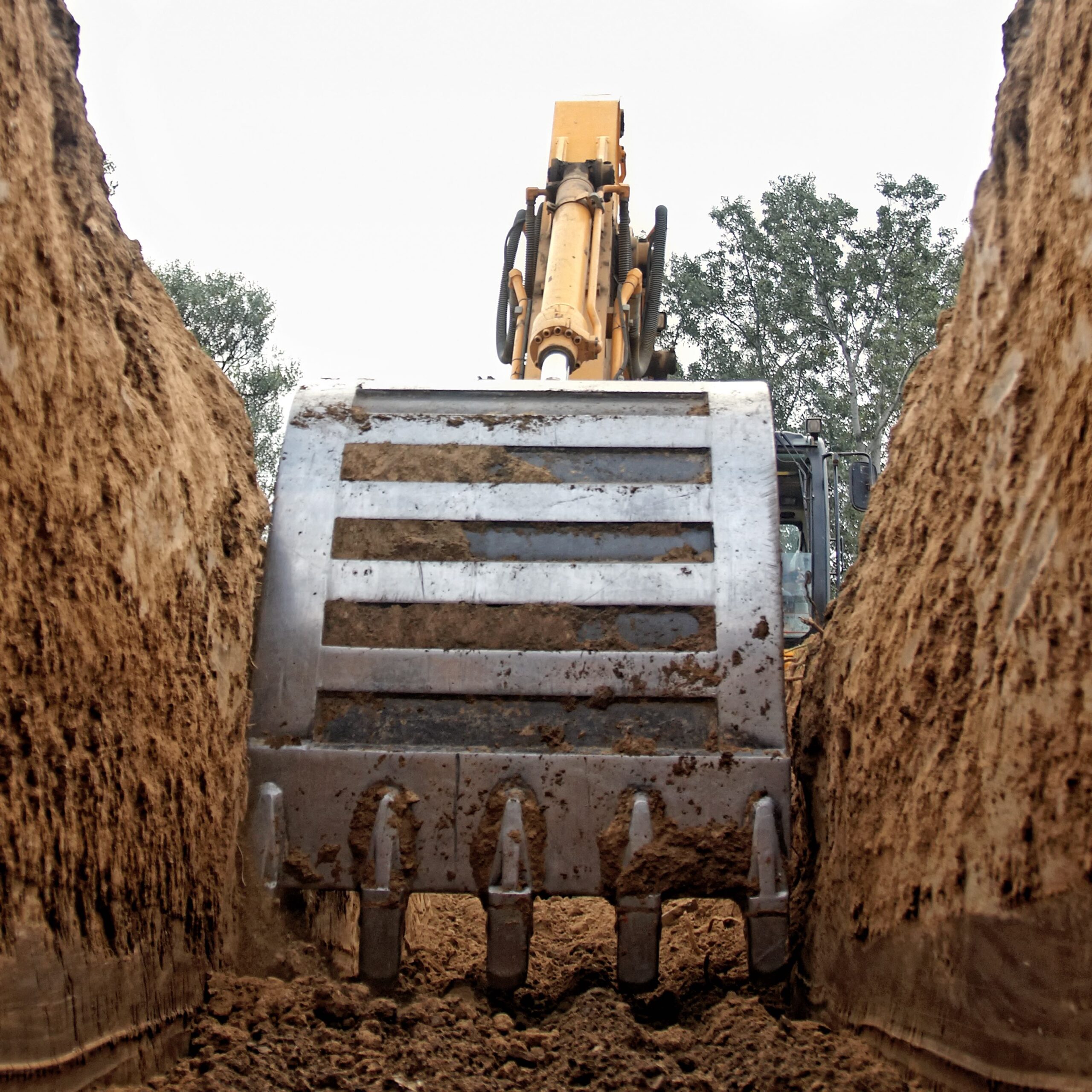
Machinery and equipment are used everyday on the worksite. Machinery and equipment are designed to make work easier, more efficient, and can generate great amounts of power and speed. This is really handy when there is a job to be done, but this also means there is a greater potential for harm and injury. When there is a potential for harm, especially in the workplace, it needs to be managed to prevent incidents or injuries. A great place to start is by identifying the hazards and risks involved with the machinery and equipment being used so that you can put controls in place to effectively manage them.
Many pieces of machinery and equipment use force and motion to cut, bend, join or shape materials. This force and motion can harm workers in many different ways such as crushing, cutting, puncturing and burning.
It is good practice to identify the risks to workers’ safety. When machinery and equipment is identified as a hazard in the workplace, the next required step is to manage the hazard. Begin by assessing the risks that these hazards pose to workers. A risk assessment in relation to the machinery and equipment can be completed in the HazardCo app to record hazards and the controls put in place to manage these risks. Keep a list of the common hazards in the workplace and how they are controlled in a hazard register. A Hazard Register template available in the HazardCo Hub.
It is also good practice to complete Standard Operating Procedures (SOP) for your machinery and equipment. The SOP should document instructions on the safe operation and maintenance of and training for any machinery or equipment. Ensure that the SOP is created using the manufacturer’s instructions so that it is specific to the machinery and equipment used. A few example SOP’s and a template are available in the HazardCo Hub that can be used to create SOPs for all the machinery and equipment in the workplace.
Machinery and equipment are often used in harsh working environments, and on a daily basis. These two factors mean that eventually machinery and equipment can become faulty, damaged or break down over-time. If and when this happens, it can pose a risk to the workers who are using or working closely to the machinery or equipment. It is good practice to manage these risks by doing daily pre-start checks before beginning work. This ensures that the machinery and equipment are inspected and are in good working order before beginning the works. These pre-start checks should be recorded and the records should be kept. There are Pre-start Checklist templates available on the HazardCo Hub.
Workers should be trained to competently complete the work they are required to do. This is especially important when using machinery and equipment as there is an increased potential for harm when it is not used correctly. Make sure that workers have the appropriate training, supervision and qualification (if required) to safely use the necessary machinery and equipment. Keep an up-to-date register of what machinery and equipment workers are trained on and competent in using. A Training Register template is available on the HazardCo Hub which can be downloaded and filled out.
If you need a hand with managing the hazards and risks involved with using machinery and equipment, give HazardCo a call on 0800 555 339.
What is Hi-Vis?
Hi-Vis is a form of Personal Protection Equipment (PPE) designed to minimise the risk of personal injury by making the wearers visible.
The New Zealand legislation has standards around the criteria that hi-vis needs to meet, the types available, and when they should be worn.
As a business owner, you must manage the risks associated with your workplace activities and in doing so follow a process to control those risks. If you cannot eliminate a risk, you must implement measures to reduce the level of risk, provide training to workers, and provide PPE – which can include hi-vis.
Protective clothing is one of many control measures used to mitigate risk, however, it is the ‘last line of defense’, and all other reasonably practicable control measures should be in place first before relying on protective clothing. It is up to the PCBU if hi-vis clothing is a control that will be implemented on-site. However, we do recommend that it should always be worn around moving vehicles, plant and machinery.
Types of Hi-Vis
There are many types of hi-vis clothing available in New Zealand, and it is important to understand the different types., what is appropriate for your workplace, and ensure that you supply hi-vis that meets the standards. The only two hi-vis colours that are acceptable in NZ are yellow and red-orange.Red is only allowed if it is in the orange spectrum. Otherwise, it cannot be considered a hi-vis colour, because it is not easily visible for some people with a specific type of colour-blindness.
Maintaining Hi-Vis
It is important that the correct hi-vis is selected and used correctly. Your workers should know:
Hi-vis should be maintained to ensure that it remains effective, over time the materials can fade which will affect the performance of the tape and fabric. It should be regularly checked for wear and tear, fading, and ensure that there are no additional fabrics, logos, or pockets impacting the functionality of the hi-vis in accordance with the standards AS/NZS 4602 and AS/NZS 1906.4.
If you have any questions get in touch with the HazardCo team
HazardCo was created by tradies, for tradies. We understand that on-site risks change, all day, every day, and have experienced what happens when they aren’t well managed first hand. So we formed HazardCo to help tradies get their health and safety sorted – and help you to feel confident that you’re doing the right thing.
HazardCo’s digital health and safety solution uses everyday technology to help you complete all your health and safety requirements – all from your back pocket. Plus, HazardCo helps you to cut back on paperwork and saves you time by using straightforward templates and reports, which are full of tips and suggestions to give you the confidence you have it all covered.
You can use the HazardCo App on your smartphone to create a Toolbox Meeting, Site Review, Risk Assessment, Incident Report, Vehicle Checklist, and more. The app is packed with simple-to-use tools that guide you through each of these activities, making them super quick and easy to complete. The HazardCo App enables our members to feel confident that they are on top of their health and safety from anywhere, at any time – whether they’re on-site, taking a coffee break, or even at home after a long day at work.
HazardCo takes the hassle out of getting your team on board because the app is free to download for everyone on-site; this includes subbies, your team, and also visitors to your site. This means that at the site Hazard Board all they need to do is use the app or your camera to scan the QR code when they sign in and out which gives you the visibility of knowing who has been on-site and when, without having to be there in person. Plus, there’s no need for loads of paperwork and meetings the first time someone arrives on-site – all they need to do is scan in and complete their induction on their smartphone. It’s simple, smart, and time-saving while also giving you the confidence of knowing you have your bases covered.
Along with the app, being a HazardCo member also gives you access to the HazardCo Hub – our digital tool for setting up new projects. All of the information you need is stored online meaning that you can login from anywhere, at any time. Plus, you can use the hub to view, download, and review activity reports, including site reviews, risk assessments, and inductions.
Good health and safety practices are about more than just following the rules; they’re about doing the right thing to keep you and your team safe. HazardCo’s smart digital tools save you time and paperwork, giving you the confidence that you’re doing everything you can to keep your team safe.
Any questions, get in touch with the HazardCo team today
When it’s not possible to work from the ground, the use of scaffolding is highly recommended to complete those at height tasks. Generally, any building, demolition, or at height repair works will require scaffolding.
There are other height equipment available such as;
Doing a thorough risk assessment is key to determining what the right equipment for the job will be. Use this table as a guide for your choice of height equipment.
As always if you would like to discuss your health and safety requirements further please call our Advisory team on 0800 555 339, extension 4.]
Working at height for work such as building a house, renovations, painting, decorating, or roof work? Scaffolding could be the safest piece of height equipment to use for the job as it provides workers with a flat-level working platform and of course fall protection.
There are different types of scaffolds and the type you will use will depend on the environment you are working in and what is best suited to your task. The common types of scaffolding are proprietary and prefabricated, tube and coupler, and suspended scaffold. If you want to know more about these systems, click here.
Anyone involved in the installation of scaffolding is required to have the knowledge and skills to do so. Scaffolding up to 5 metres should be installed by a competent person. Competent means someone who has the knowledge and skills to carry out a particular task like installing scaffolding. The easiest way to gain this knowledge and skills is through training, qualification, experience or a combination of all three.
It is important that you know that scaffolding greater than 5 metres must be installed by a person who holds the appropriate class of certificate of competence (COC) for the type of scaffolding. Scaffolding over 5m is also notifiable to WorkSafe. This can be done online here.
We have a Scaffolding Task Analysis (TA) that you can use. This TA outlines the hazards, risks and controls that need to be put in place when it comes to installing and using a scaffold. Also available is a pre-start checklist for you to conduct your daily checks before use. These can both be found in the templates section of the HazardCo HUB. We will touch on in week 3 about the when, what, how and why when it comes to checking scaffolds.
Do you know what you need to do before you demolish or refurbish a property, building or structure? Find out what the asbestos regulations mean for you before doing any work.
Identifying Asbestos
Planning is key to identifying all potential hazards and the risks involved when doing any sort of demolition or refurbishment work. Asbestos can be found in buildings constructed or renovated before the year 2000 and as such it is more than likely to be present at your next job. You can find out more about where asbestos can be found in this WorkSafe resource.
Asbestos or asbestos containing material (ACM) must be identified and removed by a competent person before the demolition or refurbishment is started (unless demolition is required to gain access to the asbestos). Things to consider when planning your work:
If the competent person is unsure whether asbestos is present it must be assumed that it is and all steps taken to mitigate the asbestos risks. If asbestos is identified you must notify all parties involved such as the homeowner, landlord, occupant and/or the contractor in control of the site.
Asbestos Management Plan
Any works where asbestos has been identified will require an asbestos management plan. This outlines where any asbestos or ACM has been identified. Your plan must contain the following:
Other information may be included in the asbestos management plan, such as:
Emergency Planning
An emergency plan is required for demolition work where plant and structures contain asbestos. When developing the emergency procedure, you should consider:
The procedure should include:
The emergency procedure must be carried out if there is an emergency.
If the plant or structure is not structurally sound or is going to collapse, WorkSafe NZ should be notified as soon as possible.
Disposal of Asbestos
Before demolition starts, think of how you are going to dispose of the waste. Having a good waste containment and disposal process is just as important as having safe processes for working with asbestos.
Asbestos is considered special waste and special waste needs to be handled, buried, pre-treated or tested before it can be disposed of at the landfill. You need to make an application if you want to dispose of special waste.
Applications are often called special waste disposal declarations. Contact your local landfill to enquire about what they require before taking any material to them.
Not all landfills or transfer stations are authorised disposal sites, check with your local council to find out where your local authorised site is.
Double-bag all waste, all waste including single use masks and coveralls, cloths and plastic sheets should be double-bagged in heavy duty plastic bags. Twist the top of bags tightly, fold the necks over and seal with adhesive tape. Clearly mark the outer bag as asbestos waste.
Check with your receiving landfill for further details especially around handling details. There are often restrictions around how the material is offloaded.
If using skip bins or wheelie bins on site, be aware that many providers of these bins do not allow asbestos to be disposed of in them. Check your provider first for approval.
Document your disposal process in your Asbestos management plan and Asbestos Task Analysis (TA) considering the above.
As a HazardCo member you have access to a library of TA forms located in your Hub, which include demolition and the removal of non-friable asbestos for anything less than 10m2. Use of these resources will help you to identify the hazards and risks in your workplace and the recommended controls.
Our team of Health and Safety Advisors are here to help you with anything you are unsure of, give us a call on 0800 555 339, option 4.
Demolition is not just the knocking down of buildings or structures, it also includes smaller maintenance and renovation work such as the dismantling of parts of structures (e.g. one part of a steel-framed building) or the removal of walls.
When planning your works you need to first identify the hazards and manage the risks:
When demolition is involved there is always the potential for the collapse of the structures. Ensure structural / supporting elements are identified before demolition (you may need to seek structural engineers’ help identifying these, and in what order to take them down).
Make sure you have the following documents completed and available for your demolition work:
You can find these in your Templates Library in your Hub. You can login to your Hub here.
These should be tailored to the task at hand and regularly updated as changes occur.
If you have any questions reach out to the HazardCo team
Are you aware of when you need to notify WorkSafe NZ of your particular hazardous excavation works?
Conducting any of the following excavation works will mean you’ll need to complete this WorkSafe NZ online notification form:
It is expected that at least 24 hours notice is given prior to commencing such excavation works.
Notifying WorkSafe of your intended works allows them to gather statistics on the number of high-risk works going on around the country, and plan their use of resources to promote the prevention of harm.
Make sure you complete a Task Analysis for your high-risk works, you can access Task Analysis Templates from the Templates tab in your Hub. This will help you to identify the hazards, and the controls needed to minimise the risk to not only those involved in the works but all those working on the site.
If you have any questions or would like to discuss your particular hazardous works please feel free to call our Advisory team on 0800 555 339, extension 4.
What is excavation work?
Moving or removing earth or other materials with tools or equipment is generally classed as excavation work. Excavations are used in a number of different situations, such as during the construction of buildings, building retaining walls, and installing underground utilities. It is important that when carrying out excavations that underground utilities are always identified first.
Some common types of excavations used in residential construction are cut and fill excavating, pile holes, potholing, and trench excavation:
Cut & Fill
Cut and fill excavation, also known as stripping excavation is the method used to clear and prepare large areas. This method involves removing all of the material such as rock, sand, and topsoil that would be unstable to work on.
Pile Holes
Pile holes are usually excavated using methods including backhoe digger, drilling or hydro excavation. Pile holes should be covered and barricaded as soon as possible and only those involved in the works allowed nearby. Water buildup should be monitored and pumped out.
Potholing
Potholing is simply a small excavation or hole to inspect and find underground services. It’s important that potholes are covered or barricaded when they are not being used to prevent anyone from being hurt.
Trenching
Trenching is an excavation method used to prepare or replace underground utilities, build retaining walls, or investigate what is beneath the surface.
Trenches are long narrow excavations, and are deeper than they are wide. Conducting trench excavation is subject to many different factors including its size, the likelihood of underground utilities, and materials. This means that the most effective method of excavation changes from project to project, and should always be treated with caution.
Due to the scale of some of these operations, it is common that they usually require large excavation vehicles and good controls around traffic management should be in place.
Managing the risk
No matter how deep the excavation is, if there is a risk of collapse, you need to carry out a Risk Assessment and put controls in place to prevent this, you can find our Task Analysis on excavation work in your Hub. Excavations work is classed as high risk, so it is important that if you are completing excavations, that you are familiar with the guidance in the WorkSafe Good Practice Guidelines for Excavations Safety.
Covering or bridging.
When covering holes or bridging shallow trenches on building sites, ensure that the material used to cover or bridge is made from a suitable material. Heavy-duty plywood designed for weight-bearing, steel plates, or other products specifically designed for that purpose.
For holes, ensure they are fully covered and the covering cannot easily move. Avoid slip and trip hazards by ensuring walkways around these hazards are managed.
Water hazards after rain can create a drowning risk, especially for children. It can also increase the risk of sidewall collapse.
Types of barriers
A secure site is very important with any open excavation. You need to consider how long the excavations will stay exposed, and if an excavation is to be left unattended overnight, then consider plating, fully enclosing with a safety fence, or backfilling to minimise the risks. Barricades, cones, plastic mesh netting not supported by a solid frame, and hurdles are not sufficient to adequately protect from excavation risks. We recommend safety fences for internal fencing for long-term or unattended worksites where excavation hazards are present
Understand your competency level
Excavations up to 1.5m deep, you should have recent experience in carrying out or supervising excavation work.
1.5m – 3m deep you should have recent experience in carrying out or supervising excavation work at these depths, technical or trade qualification (eg a civil engineer or drain layer)
3-6m Technical or trade qualification (eg a civil engineer or drain layer). Experienced temporary works designer able to judge whether it is safe.
Make sure you are aware of your requirements for managing the risks of excavation.
The HazardCo App site review resource has a list of risk controls that should be in place to minimise the risk associated with excavation work.
If you need a hand getting started or would like more information, get in touch with the friendly HazardCo team today – we’re always happy to help.
Homes built or renovated between 1950 and 2000 are likely to contain some asbestos. Therefore, every tradesperson is likely to come into contact with asbestos at work sooner or later. That’s why it’s important for you to understand how to manage the risk from working with or near asbestos, and how to protect yourself and others from exposure to airborne asbestos fibers.
Areas that we recommend getting tested are cladding, roofing, vinyl, fibre cement sheeting, internal ceilings, and plumbing lagging.
There are 3 main types of testing or surveying; Management, Refurbishment, and Demolition, and each of these is designed for a specific purpose.
It is important that when you are conducting work that requires planning permission, it is likely that you will require a demolition or refurbishment survey to search for asbestos present. As the contractor, you have a legal requirement to ensure asbestos is identified and removed before any work begins that may disturb the asbestos in your client’s home.
You can refer to the Healthy Homes NZ website for more details on asbestos testing here
What to do if you or your workers uncover or damage materials that may contain asbestos:
You can view the WorkSafe website to find out how to apply the 10 m2 rule to an object that is not flat, such as asbestos piping and other frequently asked questions relating to Asbestos Licensing here.
Our advisory experts are here to support you, so if you have any asbestos-related questions while you are conducting your renovations – get in touch or give us a call on 0800 555 339.