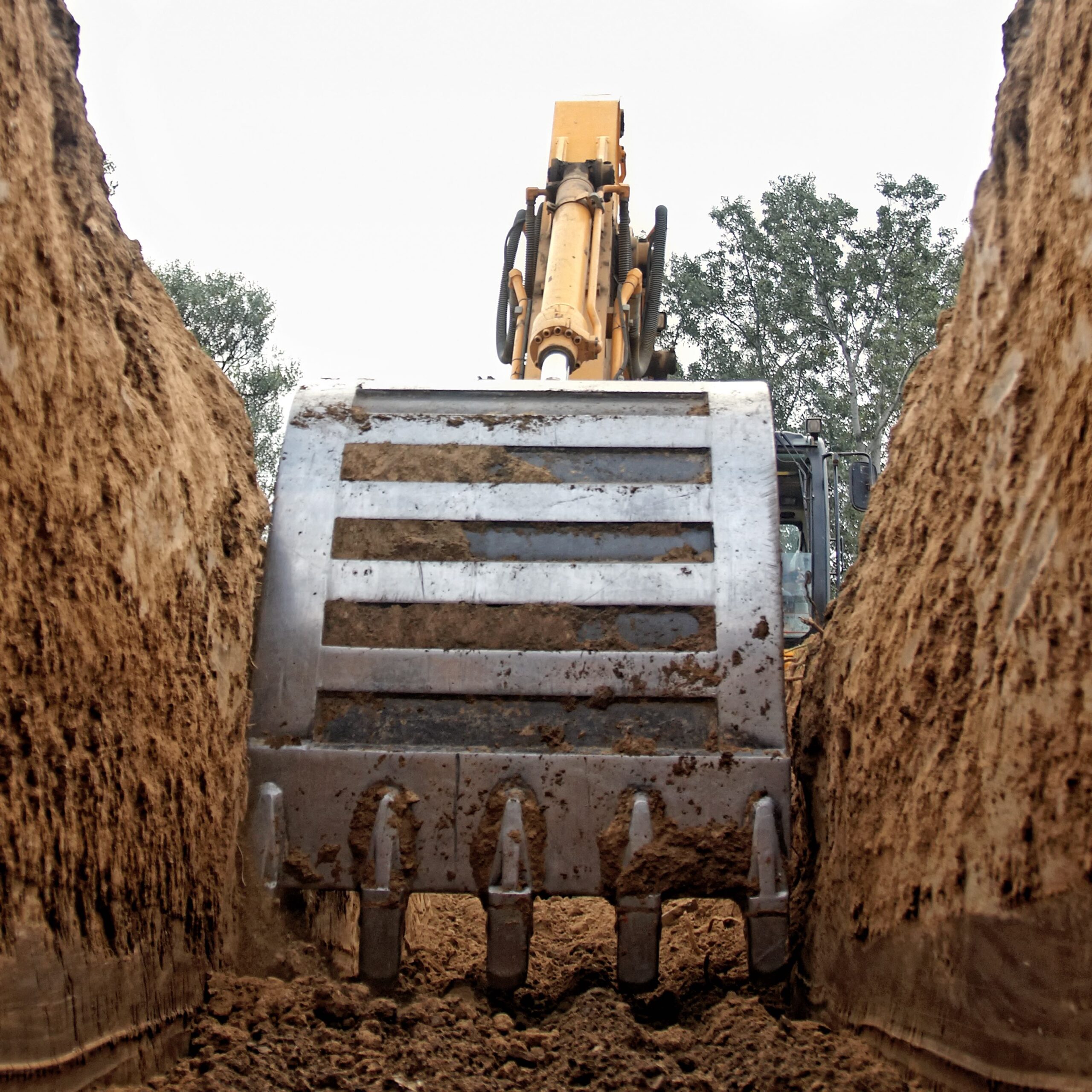
Any airborne contaminants are a cause for concern, but one of the main offenders in the dust world is wood dust.
Workplace dust is unavoidable on-site. Whether your cutting, sawing, sanding, or drilling, many day-to-day tasks produce both fine and large dust particles which, when inhaled, can be harmful to your body.
What’s the damage?
Our bodies are able to filter out any large particles that may enter our respiratory system, however the smaller particles can go deep into our lungs which overtime can lead to damage and scarring of lung tissue.
This damage reduces the lungs ability to take in oxygen, which means over a period of time, it’s going to make it harder to breathe and can cause problems such as asthma and lung cancer. It’s not just the wood that’s the issue either… glue, resin and other treatments on the wood are also harmful and increase the risk even more.
As well as our breathing, dust can also cause issues with our eyes, causing irritation and damage, and our skin, which can lead to irritation and dermatitis.
That’s why it’s important that you cover your bases, which we’ve outlined below.
Controlling wood dust in the workplace
Education is key when it comes to making sure your workers understand the risks of wood dust. To ensure you and your team are up to speed, we recommend regular training, which can be done at your weekly toolbox talks.
Mobile & tower scaffolding units are a common sight on most construction sites. Commonly used by tradies from all walks of life, they do help us with those hard to reach areas.
But with that, like anything on-site, they do come with a certain level of risk. Whether this be falling over, equipment, tools or people falling off, or even rolling away because the breaks aren’t on, these are all real threats.
Being a mobile unit means tipping over or swaying is a huge risk. The issues and potential consequences that present itself if a unit falls over can be devastating, for your team, your business and clients.
Falling over is a risk that presents itself in several circumstances, including:
While the risk of falling is a major risk, you can reduce the risk by:
Like anything that requires working at heights, mobile and towered scaffolding units come with their own unique risks. To avoid these risks becoming an issue on-site make sure you put all precautions in place. Talk to the manufacturer, have it erected by a qualified and trusted supplier, and work on and around the unit safely. This way, the site is safer for all.
If you have any questions reach out to the HazardCo team today.
Heights are not for everyone. Some people love being high above the ground, others it’s their worst fear. For some, heights are part of the job. Working on a roof or on a multi-story building is just another day at the office. But with greater heights, comes greater risk of injury or things falling. Due to these increased risks, it is critical all your corners are covered – literally – because without edge protection, you’re putting everyone in danger.
Here’s what you need to know:
Edge protection is a protective measure that helps prevent people, tools, and materials from falling. This includes:
Whenever your site involves working above the ground or on elevated surfaces.
Edge protection is required on all exposed edges of a roof, including the perimeter of buildings, skylights or other fragile roof materials, and any openings in the roof – this also includes openings and edges of floor areas, such as balconies.
Edge protection comes in a series of forms including:
Like anything, failing to plan is planning to fail. And, edge protection is no different.
If you know your site will require edge protection at some stage in the project, make sure to build it into your initial planning and considerations. Don’t wait until a few weeks before you need it, to start designing a plan.
Consider what the potential risks are, how they will impact your team, people on-site and the general public, and how it will be installed and taken down.
With proper and thorough planning you decrease the risk of anyone getting hurt or damaging property as a result of working at heights.
Get your edge protection sorted as early as possible on a job. Make sure you have a clear timeline in place for when you’ll require edge protection on-site.
And, keep everyone on-site in the loop. Let your team and other contractors know when edge protection is being installed, how long it’ll be on-site for and then when it is scheduled to come down.
There’s no use having edge protection if it isn’t doing the job. So, ensure edge protection is:
Keeping your team safe should be a top priority on any construction site – and edge protection is a huge part of that. If you’re still unsure how best to move forward and protect your team, you can get in touch with the HazardCo team today.
On pretty much every kiwi building site, you’ll see scaffolding. But, how many of us really know the correct rules and regulations around fixed scaffolding?
Below we outline the key aspects and what you should look for when using scaffolding on your current, or next, site.
Scaffolding – by definition – is a temporary platform that is used to elevate, offer support, and provide materials during a construction process for building, repairing or cleaning of a structure.
Let’s break it down:
Scaffolding can be a tricky subject, and because of this, there are many areas that we get asked to advise on. Below we outline some of the most important aspects of working with or around scaffolding.
All scaffolds must be checked by a competent person before handover. This involves tagging the scaffolding. All scaffolds, regardless of height, must have a tag clearly displaying important safety information at access points. Included on the tag:
Depending on the height of the scaffolding there are varying regulations and qualifications that determine who can construct scaffolding.
For scaffolding up to 5 metres a competent person – someone who has the knowledge and skills to carry out a particular task must erect the scaffolding. Skills and knowledge may be acquired through training, qualification, or experience.
For greater than 5 metres the person who erects the scaffold must hold the appropriate class of certificate of competence (COC) for that type of scaffolding.
Access to working platforms must be adequate and safe for the working conditions and type of work to be carried out. Plan for the number of people using a scaffold and the weight and size of materials on the platform.
Other points to consider:
Once you’re up and working on the scaffolding be aware of the following rules around the distance between you and the surface you’re working on:
Non-proprietary platforms must have a minimum bay width of 675mm wide. All platforms must allow 450mm of clear access past stacked material and obstructions.
Guardrails must be between 900 and 1100mm high with a mid-rail located halfway between the work platform and the top rail. Toeboards are also to be fitted to prevent materials falling from the platform.
Following the correct guidelines and having adequate health and safety measures in place is critical when you’re working with scaffolding. Whether you’re organising scaffolding for a site, constructing the scaffolding or working on it, the key is to take your time and be careful.
If you have any further questions regarding scaffolding, we’re always here to lend a hand. Get in touch.
Explosive. Flammable. Oxidising. Toxic. Corrosive.
When you put it like that, hazardous substances sort of sound worthy of a certificate, don’t they?
So it’s hardly a surprise that from 1 December 2019, if you store class 6 and 8 substances over certain thresholds you are now required to have a Location Compliance Certificate.
A certificate to keep hazardous substances in check. Protecting everyone on site from harm caused by toxic and corrosive materials. A location compliance certificate is issued for 1 year and is required in accordance with the Health and Safety at Work (Hazardous Substances) Regulations 2017.
If you are working with any big, bad substances on site, it’s vital you check whether you do.
To see whether a hazardous substance location exists for the substances at your site you can use this handy hazardous substances calculator. This will give you a pretty good idea of what’s what.
You’ll need to find yourself a compliance certifier who is authorised for locations and the hazardous classifications of your substances.
You can track one down by searching the compliance certifier register. Simple as.
Another step towards a safer working day on site, get your certificate sorted for a compliant Kiwi workforce you can stay proud of.