What to expect when your workplace is inspected by WorkSafe
Jan 22, 2025
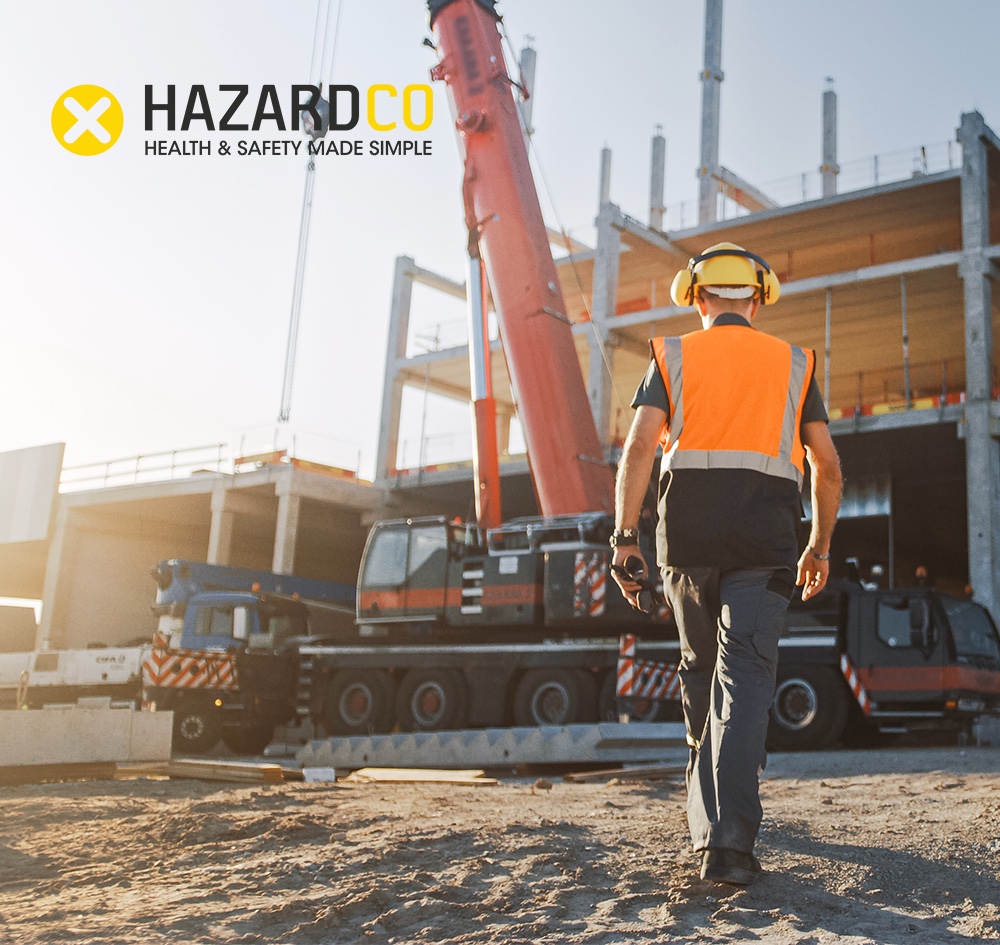
Health and safety regulators in New Zealand, are WorkSafe (the main regulator) Maritime NZ, and the Civil Aviation Authority (CAA) is here to work with you, and your workers, to keep everyone safe and healthy. Their goal is simple: to ensure that New Zealand businesses are safe and healthy places to be.
Visits to your workplace can be either pre-arranged or unannounced. Inspectors are allowed by law to show up at any reasonable time, regardless of whether or not you’re there. So, what should you expect when they come a-knocking?
Typically being inspected by WorkSafe follows a four-step process:
Step 1: Conversation
A friendly chat isn’t that scary, right? When the WorkSafe inspector first arrives, they’ll sit down with you and have a conversation. This discussion is a two-way street where they’ll want to learn about your business, the risks you have, and the steps you’re taking to minimise them. It’s also a great chance for you to ask any questions you may have.
If there’s nothing urgent that catches their attention, the inspector will typically focus on areas aligned with WorkSafe’s current KPI’s, as outlined in their latest strategy.
Worksafe has outlined three key areas of focus in their strategy:
- Acute harm – This is harm that happens quickly and directly. WorkSafe is focusing on risks related to vehicles and machinery, falls from height and falling objects, as well as chemical and electrical hazards.
- Chronic Harm – This is harm that happens over time. Current priorities include managing exposure to hazardous dusts like asbestos, silica, and wood dust (especially from treated timber), as well as exhaust fumes from vehicles and machinery, and welding fumes.
- Catastrophic Harm – These are the big, life-altering events that could result in multiple injuries or fatalities. Think of scenarios where lives are significantly and permanently impacted.
Step 2: Observation
Following the chat, the inspector will take a walk around your worksite to see if what they’ve heard from you matches up with what they actually see happening. The best thing that you can be during this, is curious. It may feel uncomfortable at times and that’s ok, discomfort just means that there’s space to grow. You’ll know you’re nailing it when it’s just a comfy casual coffee walk around.
Step 3: Examination
If the inspector sees anything concerning during their walkabout, they will follow up with you to dig deeper, understand the root cause, and work out how it can be resolved.
When this happens, they will ask you a range of questions. To keep it simple, focus on the actual question being asked and remind yourself “respond, don’t react”. No matter what they point out, their questions will essentially boil down to these three:
- Does the business have systems in place?
- Are those systems being used?
- Are they aimed at safety being the outcome?
It’s okay if you need clarification – Never feel like you can’t ask them to clarify a question further for you so that you can give them the most accurate answers you can. And if you don’t have an answer right away, it’s perfectly fine to say “I’ll come back to you with that”. Write the question down, involve your team, and follow up with the requested information. This shows the inspector that you have systems in place and are actively using them to ensure safety.
Step 4: Documentation
At this stage, the inspector might ask to see what kind of systems and processes you keep. This could include anything from your worker’s licenses or training certificates, machine maintenance logs, to incident reports. The focus will be on whether your records and systems support good health and safety practices for your worksite, workers and business.
That’s where your HazardCo records can make a big difference! Having a clear history of Risk Assessments, Task Analysis, Site Reviews and Toolbox Talks can go a long way in showing that you are proactive about workplace safety.
Outcomes:
If the inspector does find an issue, you’ll discuss together what needs to be done to address it.
The three main outcomes that may be issued by an inspector are as follows:
- Improvement notice this is the most common type of notice. It outlines what the inspector has identified, what needs to change, and the timeframe for completing the changes.
- Prohibition notice These are for more serious issues. It may require you to stop using certain piece of machinery until changes are made, or a replacement is found.
- infringement notice is rare but most severe. It isn’t limited to cases of serious harm or fatalities and can lead to persecution. If you reach this stage, it’s critical to avoid arguments and focus on addressing the inspector’s concerns immediately.
As mentioned earlier, you’ll know you’re on the right track when your interaction with the inspector doesn’t feel like an argument but more like a constructive discussion. The goal is to leave the conversation with a clear understanding of how your “referee” wants to call the game, while the inspector walks away knowing that your business isn’t one of the ones driving New Zealand’s harm statistics.
Using HazardCo can make this even easier—cutting your health and safety admin time in half while guiding you through the steps needed to keep your crew and business safe.
If you have any questions or need support, don’t hesitate to call us at HazardCo on 0800 555 339. We’re here to help!